PVC Marble Sheet Production Line
Be Green By Extrusion!
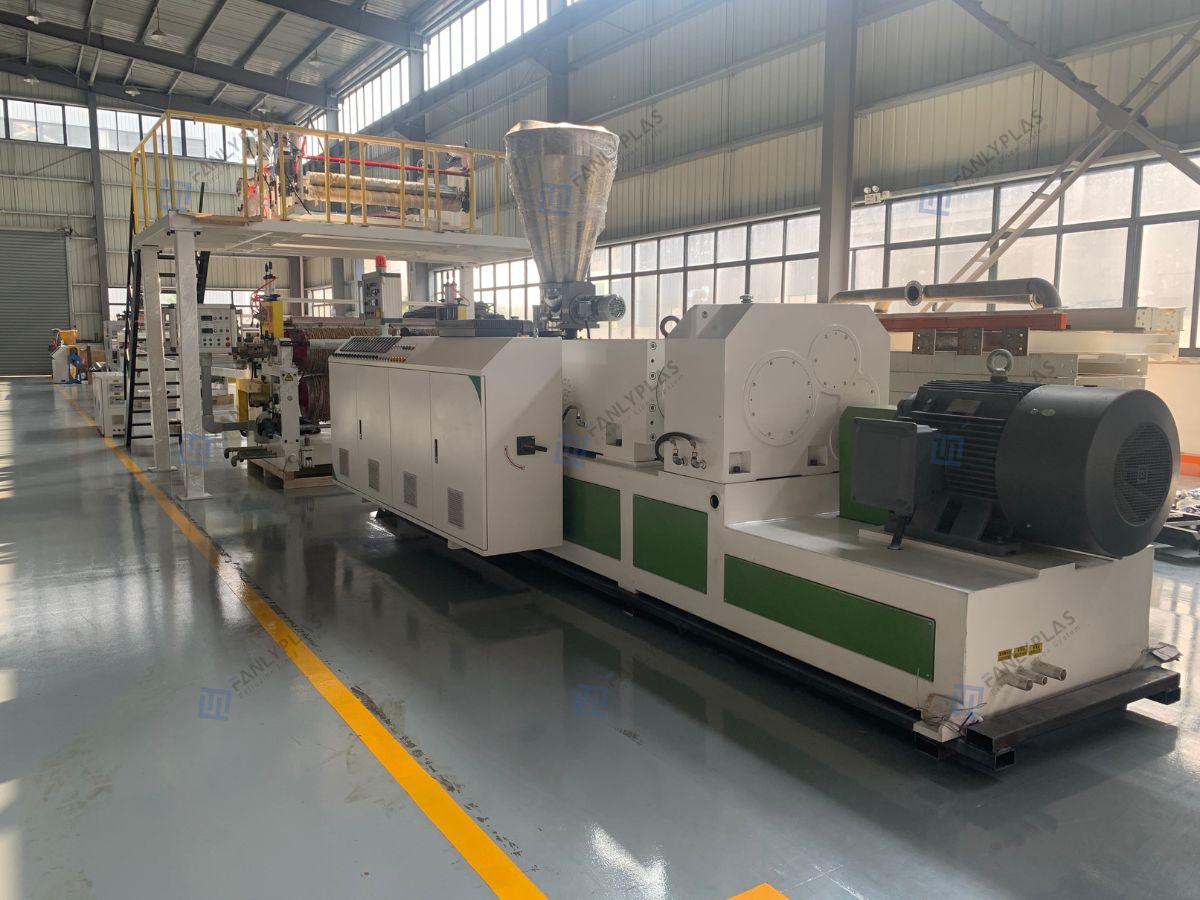
Introduction of Our PVC Marble Sheet Production Line
1
Applications : Our PVC Marble Sheet Production Line is designed to produce sheets that serve as a versatile and durable alternative to natural marble. These sheets are ideal for various applications, including wall panels, decorative boards, flooring, and furniture surfaces, offering an elegant aesthetic with enhanced practicality.
2
Production Flow : The production process begins with material preparation using crushers and millers, followed by mixing. The materials are then extruded, laminated, and shaped through calendering. Subsequent steps include cooling, cutting, stacking, and optional UV coating, resulting in the final PVC marble sheet.
3
Line Features : This production line is characterized by its automated operation, high production speed, and precise control system, ensuring efficiency and product quality. It offers production flexibility for diverse specifications, reduces costs through automation, and maintains product consistency via strict quality control.
Equipment Composition of FANLYPLAS PVC Marble Sheet Extrusion Line
FANLYPLAS offers customized PVC Marble Sheet Extrusion Line based on customer requirements, including product specifications, production volume, facility size, and desired level of automation. We provide flexible configurations to meet various needs. Below are some of the standard configurations available for FANLYPLAS PVC Marble Sheet Extrusion Line.
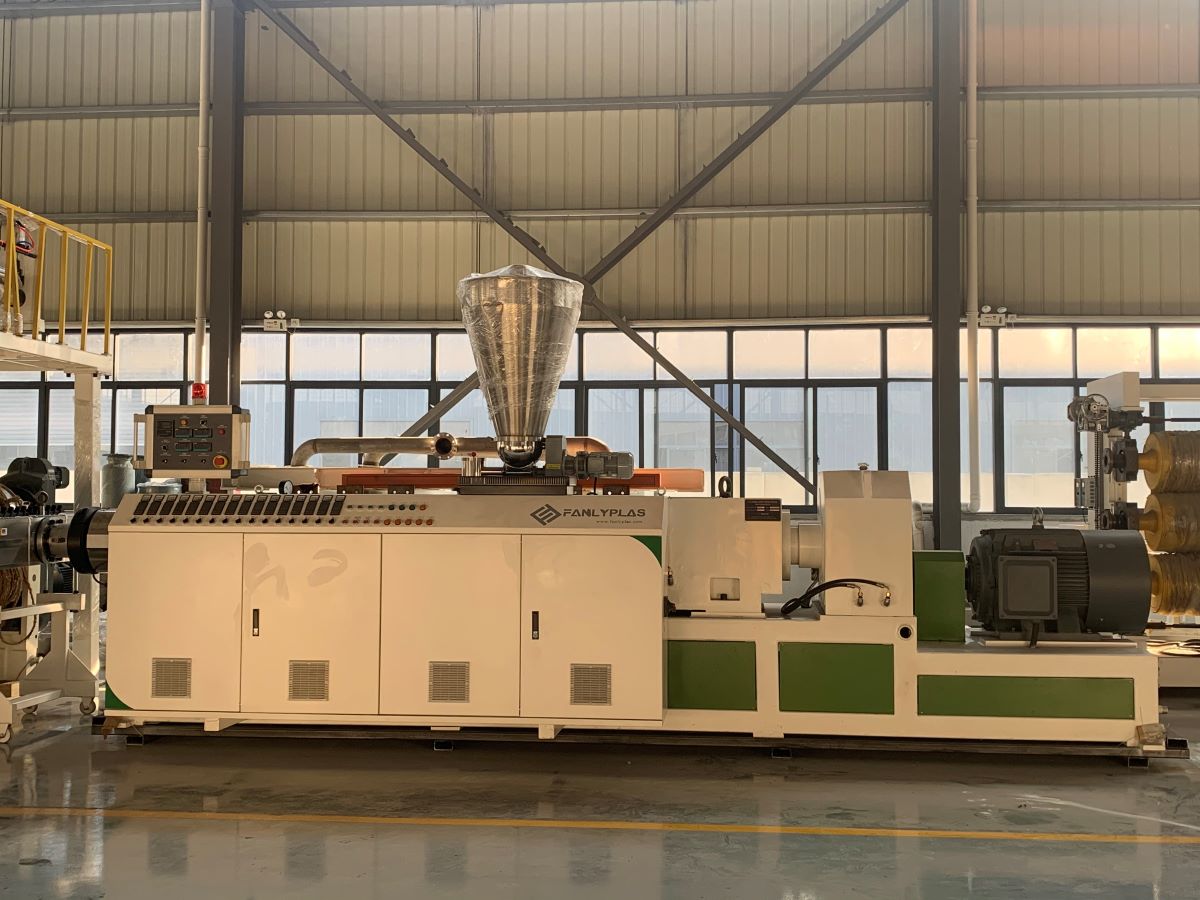
Extruder
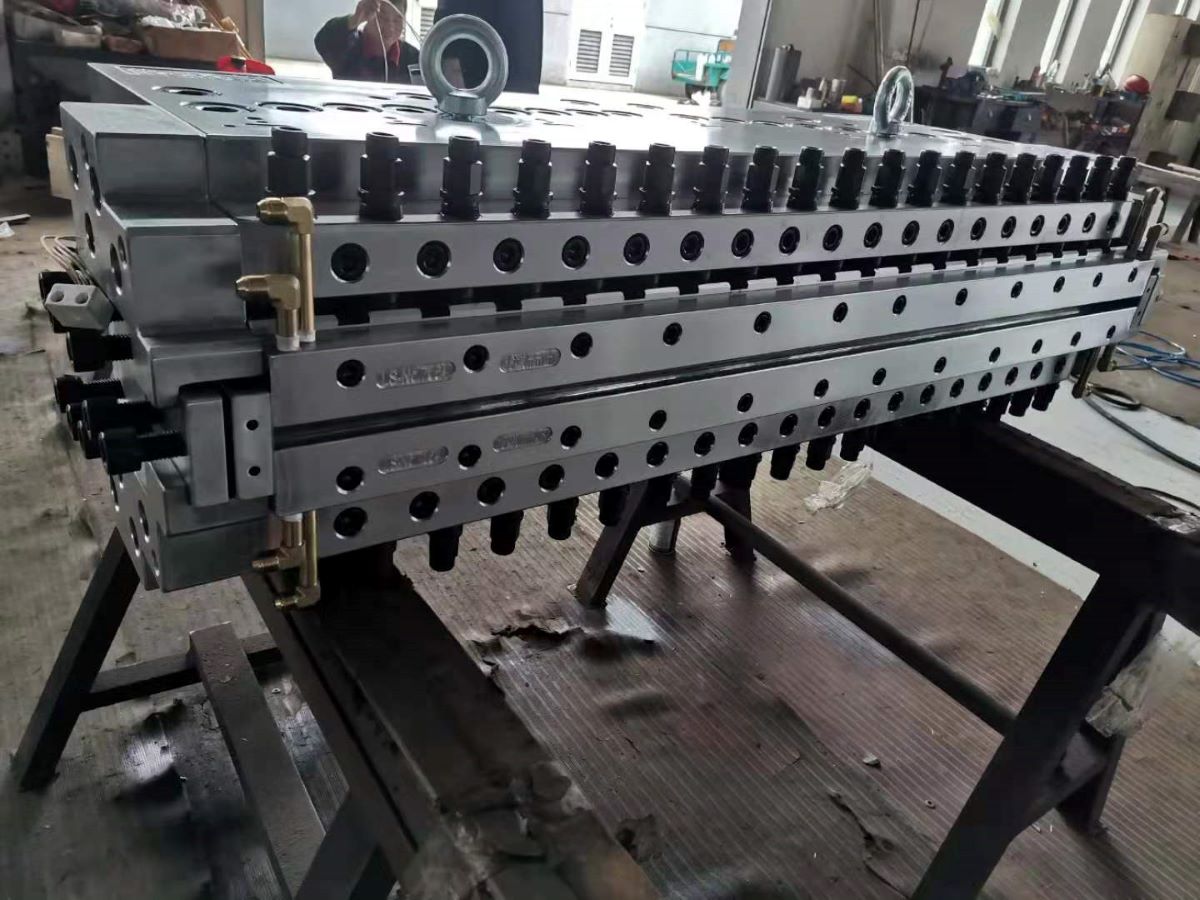
T-Die
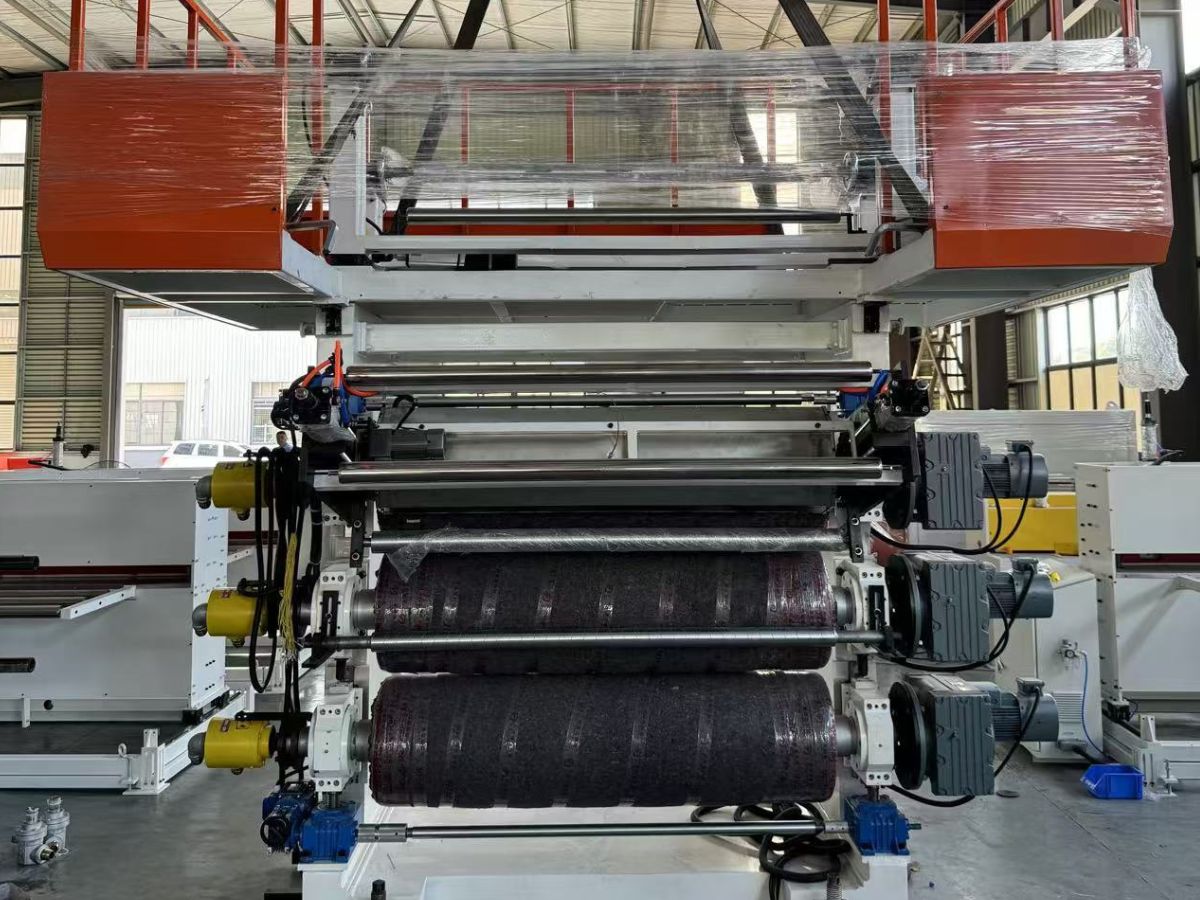
Three-roll Calender
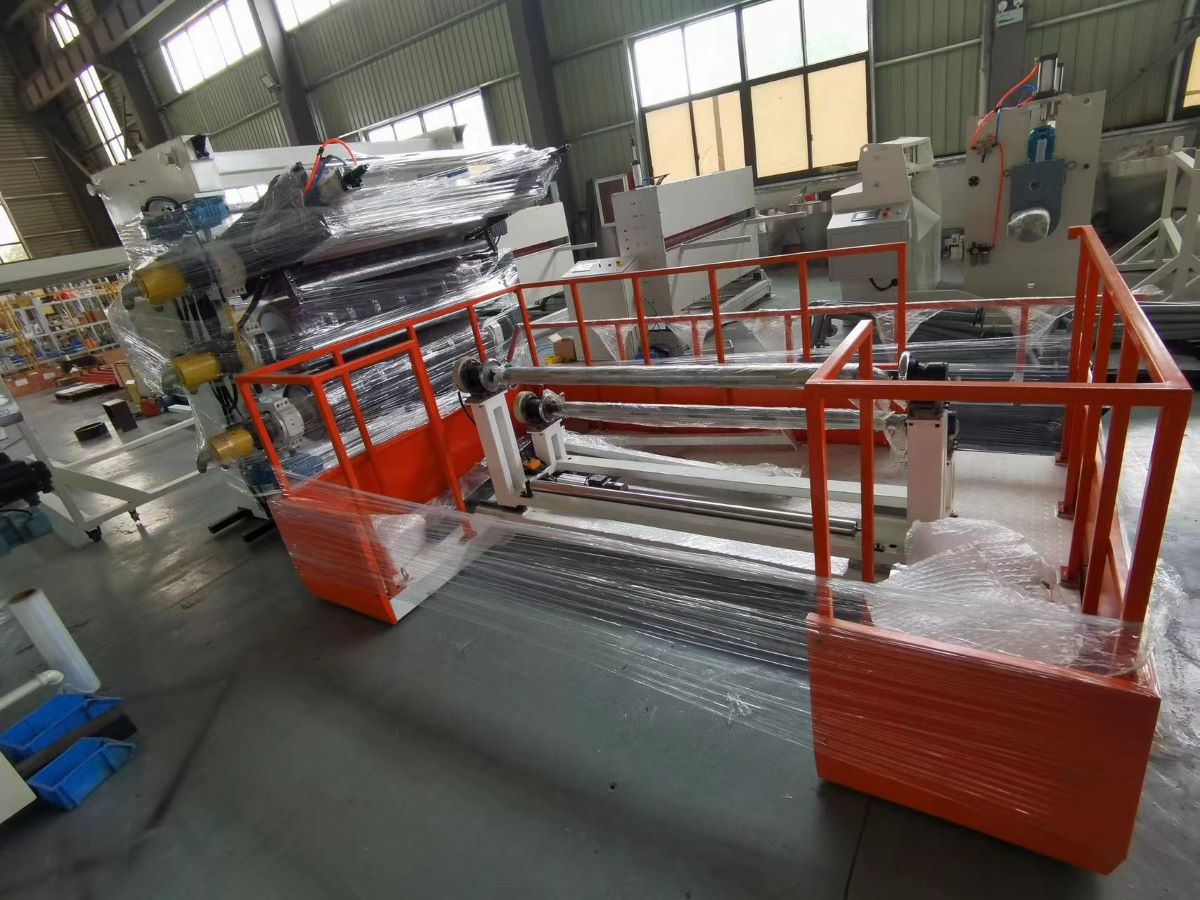
Film laminating and hot stamping device
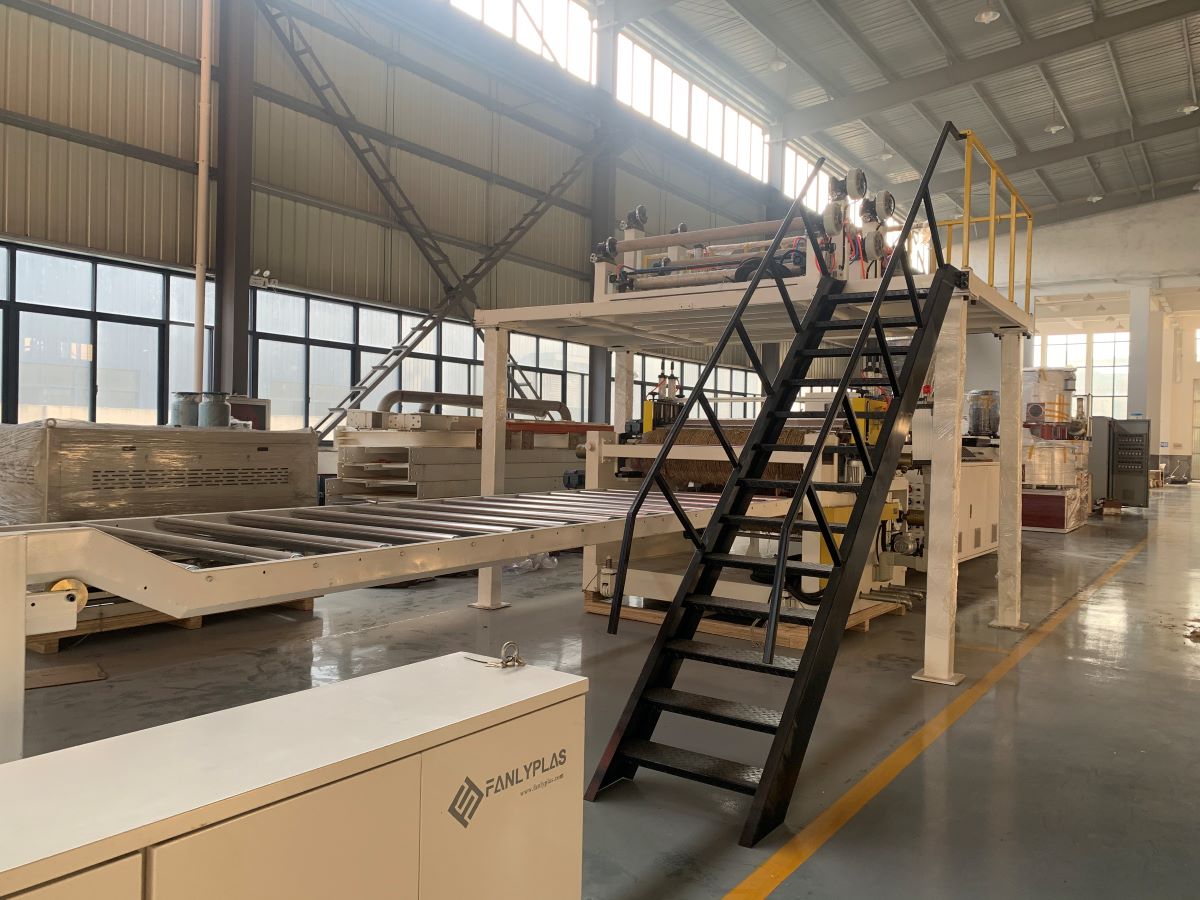
Cooling bracket and trimming cutter
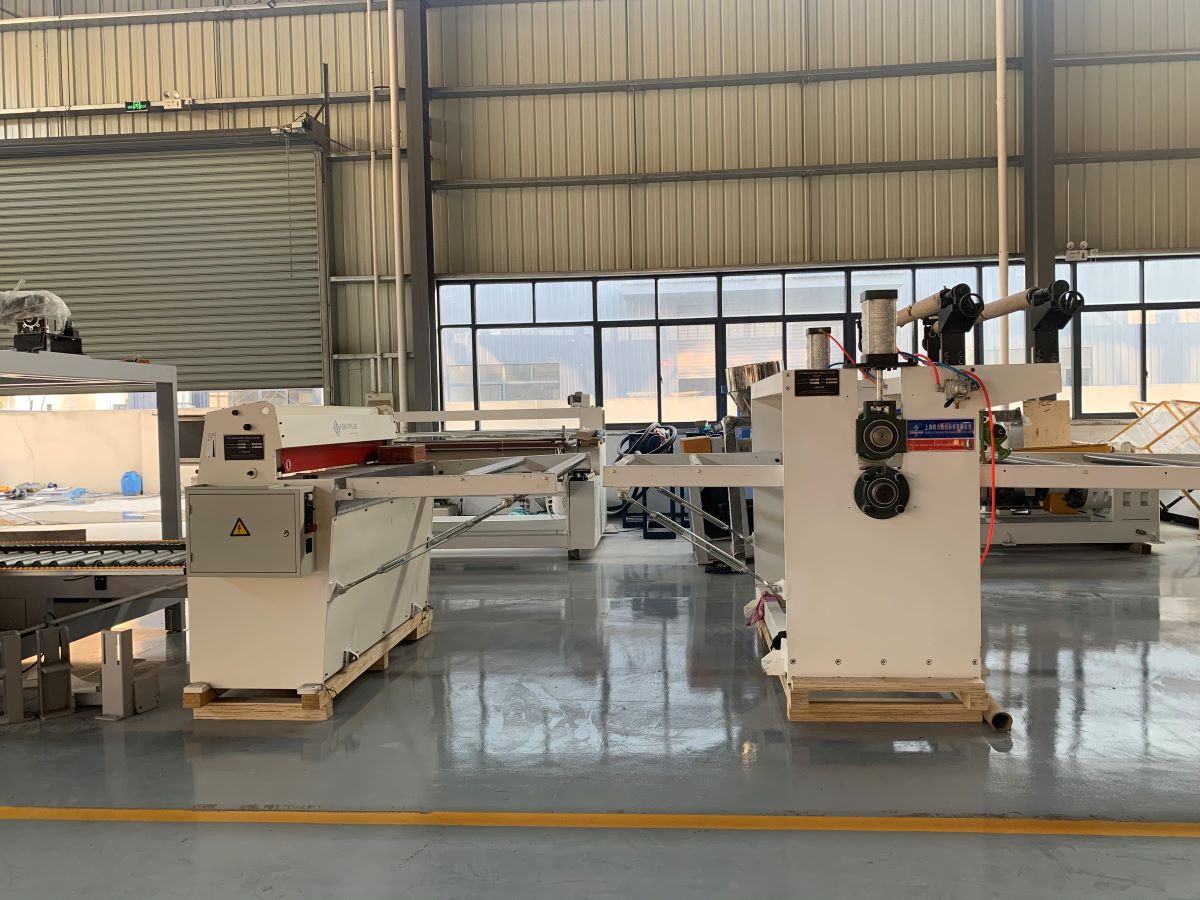
Haul off unit
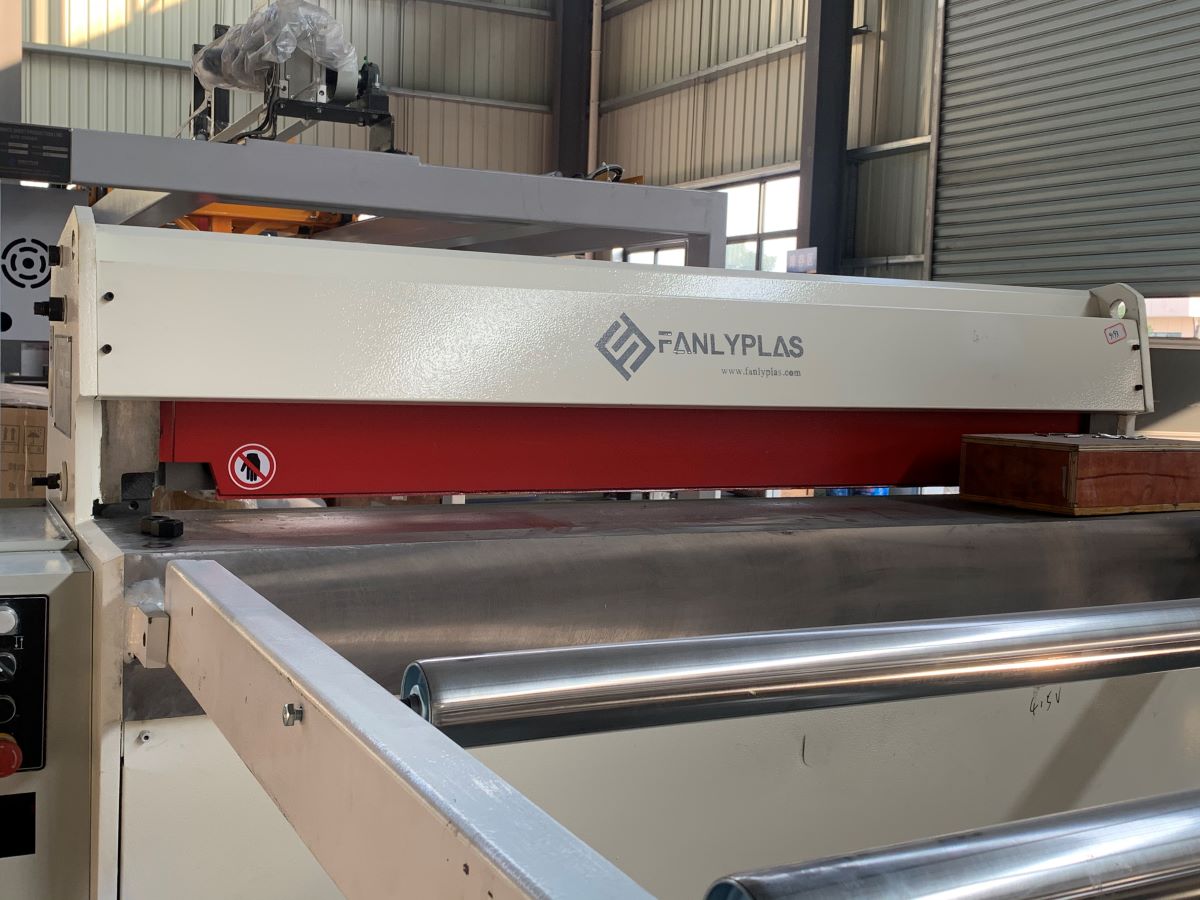
High speed shear utter
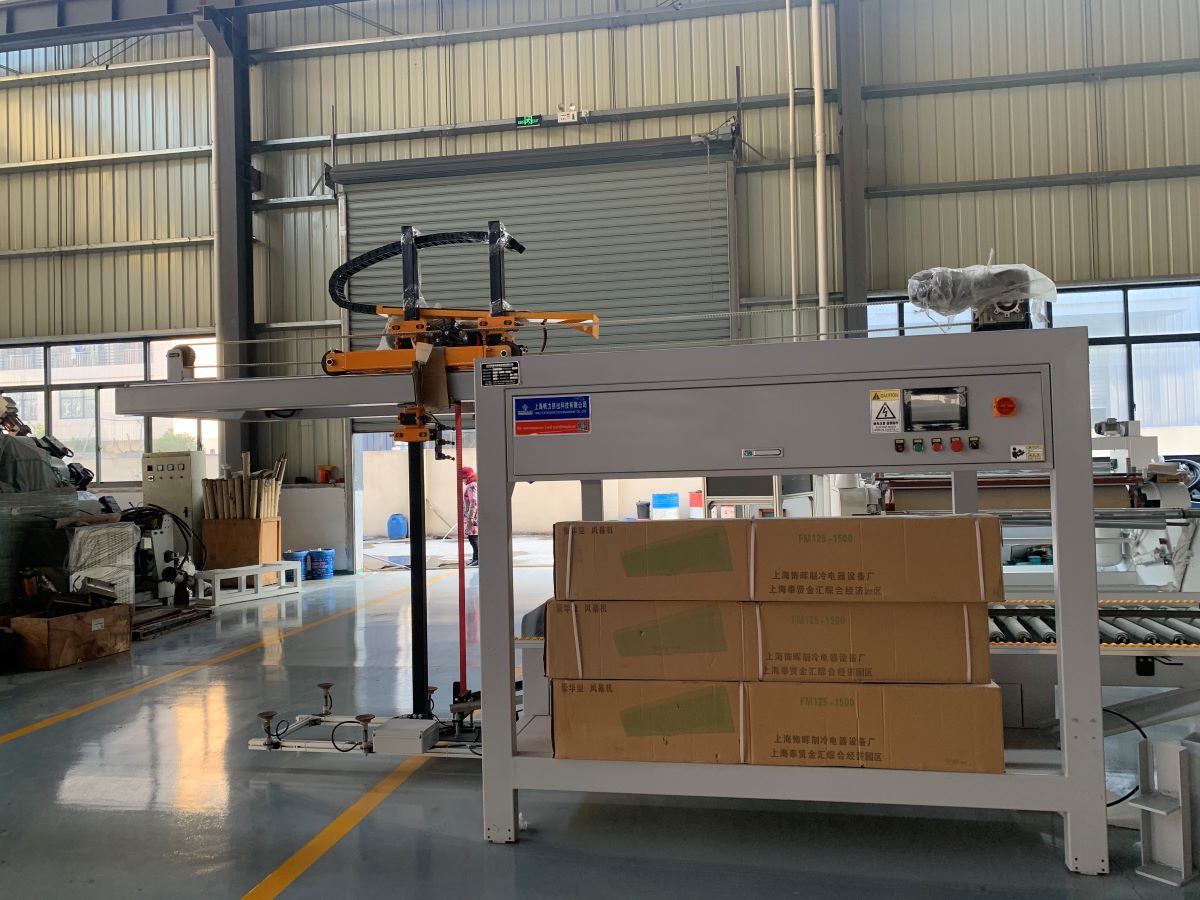
Auto stacker
Extrusion Line Workflow
1
Material Feeding
The raw material PVC powder is continuously fed into the extruder hopper through the feeder and hopper to ensure uninterrupted production.
2
Extrusion and T-Die
The extruder heats and melts the raw materials while mixing them evenly. The screw rotates to ensure even material flow, and the sheet is initially formed through the Die.
3
Laminating
The sheet passes through the three-roll calender for calendering and lamination.
4
Cooling and Haul off
Give the sheet traction, cool it down on the cooling bracket, and then cut the edges before entering the next process.
5
Shear Cutter
The sheet is cut into sheets of uniform length by the shearing machine, and the shearing is more precise through the control of the servo motor.
6
Automatic Stacking
The cut sheets are neatly stacked on pallets using automated robot. Save time and effort.
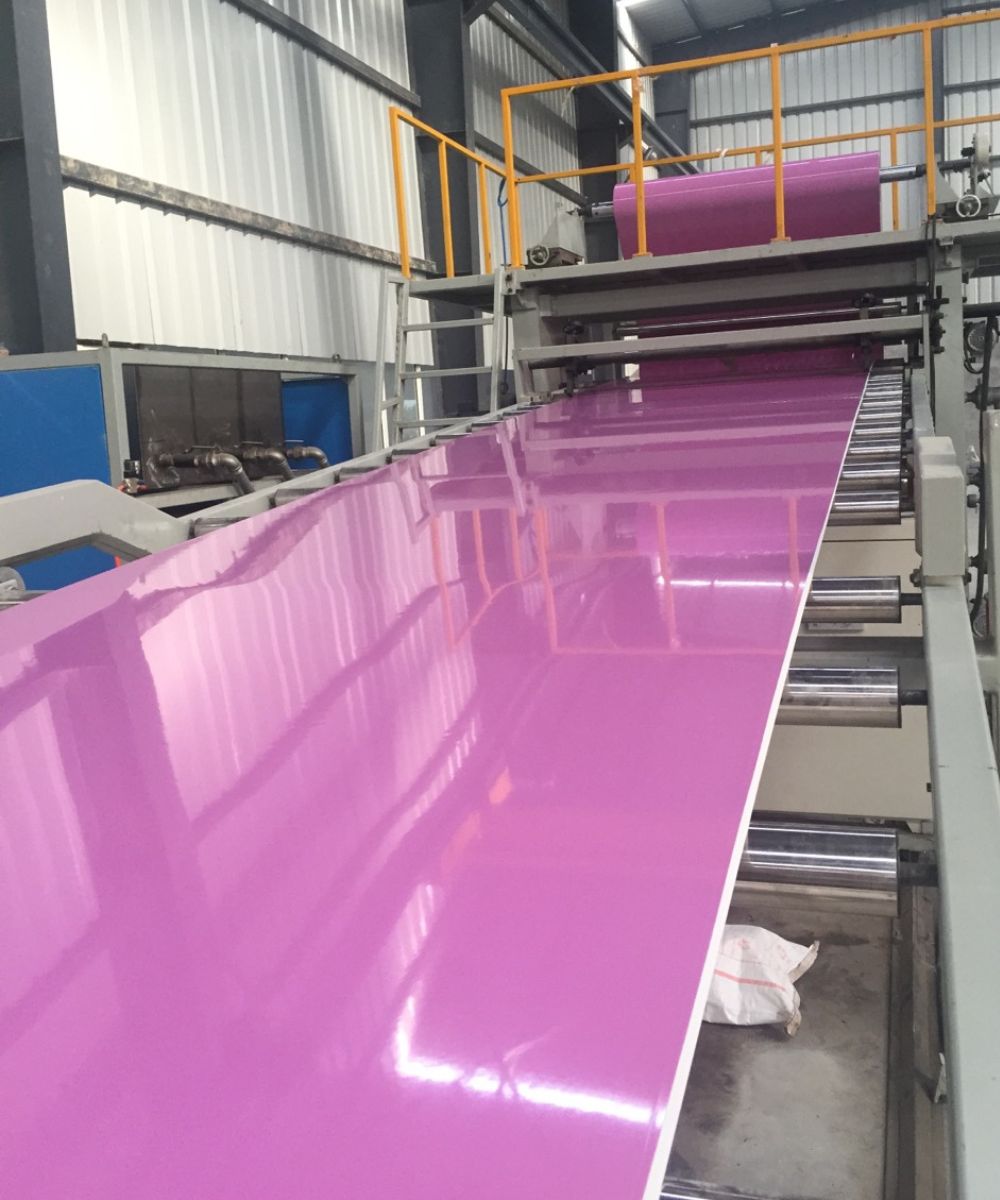
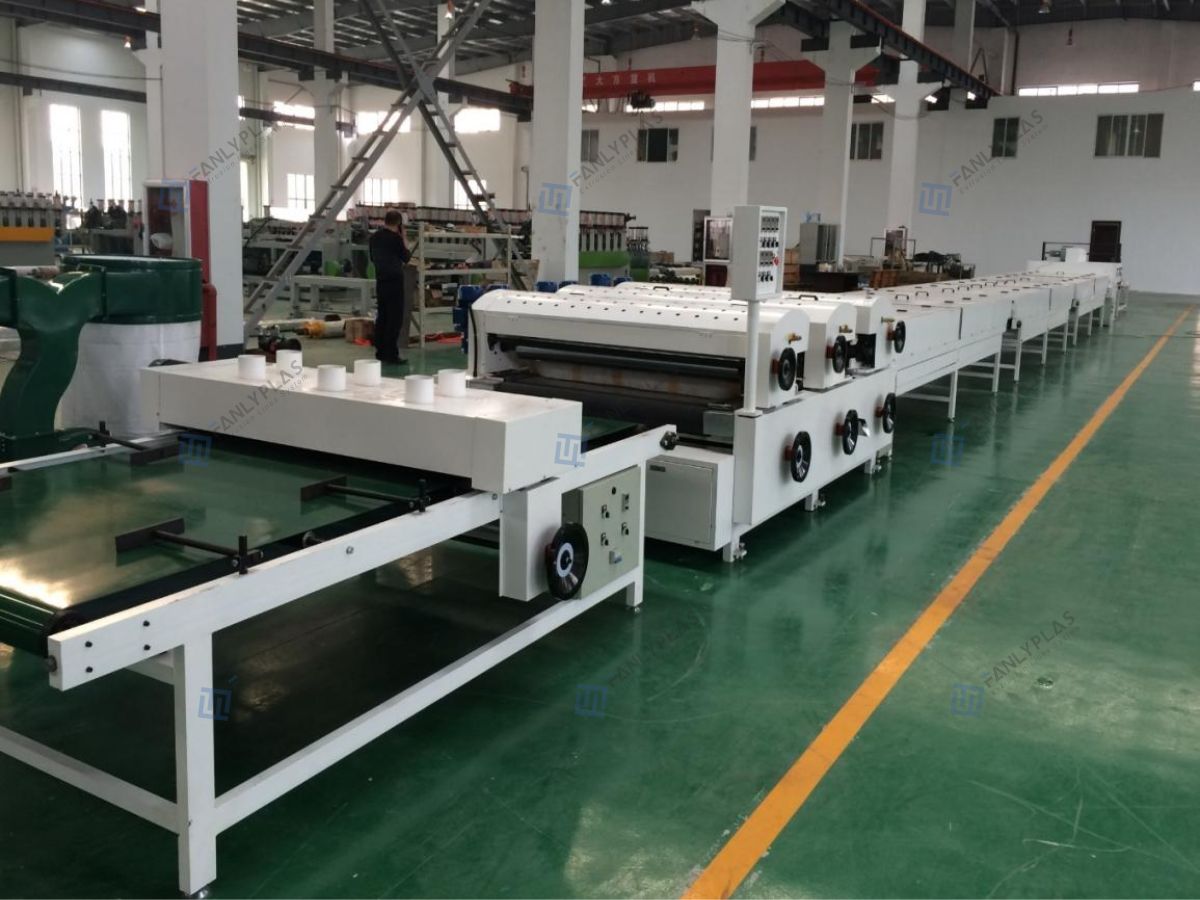
PVC Marble Sheet UV Coating Machine
1
Purpose : This machine is designed to apply a specialized UV-curable coating to the surface of PVC marble sheets. This coating enhances the sheet’s properties, improving its resistance to scratches, increasing its surface hardness, and providing a high-gloss finish that enhances its visual appeal.
2
Process : The process involves applying a liquid UV coating evenly across the PVC marble sheet surface. The coated sheet then passes under UV lamps. Exposure to this UV light triggers a rapid curing process, transforming the liquid coating into a hard, durable, and aesthetically pleasing layer. 、
3
Benefits : Integrating UV coating enhances the durability and aesthetic quality of PVC marble sheets. The resulting surface is not only more resistant to wear and tear but also achieves a high-end, polished look, making it a superior material for decorative applications.
PVC Marble Sheets: Key Attributes and Production
1
PVC Marble Sheet Characteristics & Uses : PVC marble sheets are engineered to replicate the aesthetic of natural marble while offering advantages like lighter weight, water resistance, and greater cost-effectiveness. These sheets find applications in interior decoration, including wall cladding, furniture surfacing, and decorative panels, providing a blend of visual appeal and practical performance.
2
Our Production Line Advantages : Our production lines are designed for efficient, high-volume manufacturing of PVC marble sheets. Key advantages include automated processes for consistent quality, precise control systems for dimensional accuracy, and high-speed production capabilities to meet diverse market demands.
3
Production Process & Refinements : The production process involves the preparation and mixing of raw materials, followed by extrusion and calendering to form the sheet. Lamination can be applied to enhance the surface design, and optional UV coating provides a durable, high-gloss finish. These processes ensure both aesthetic appeal and enhanced product durability
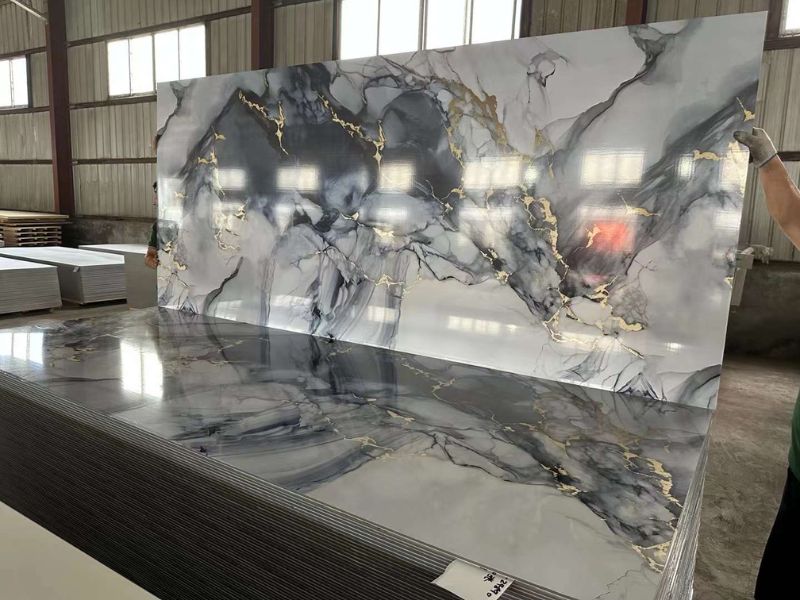
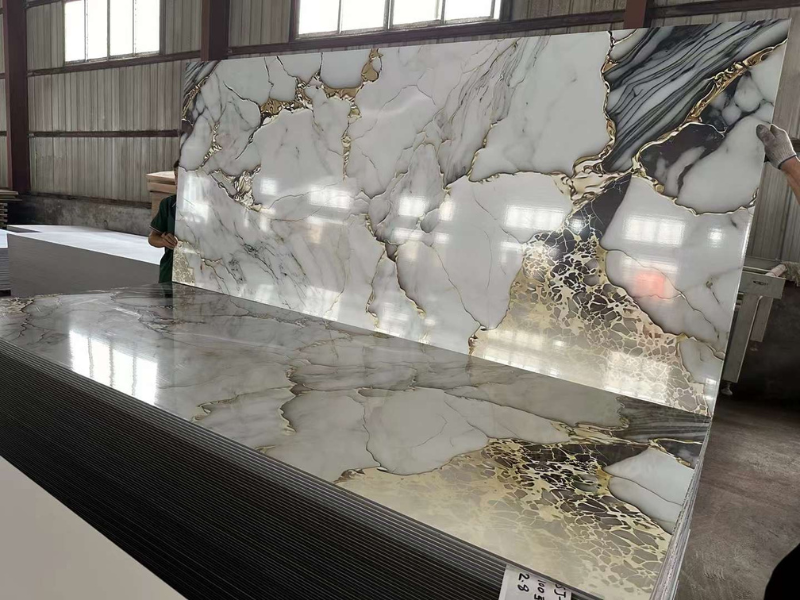
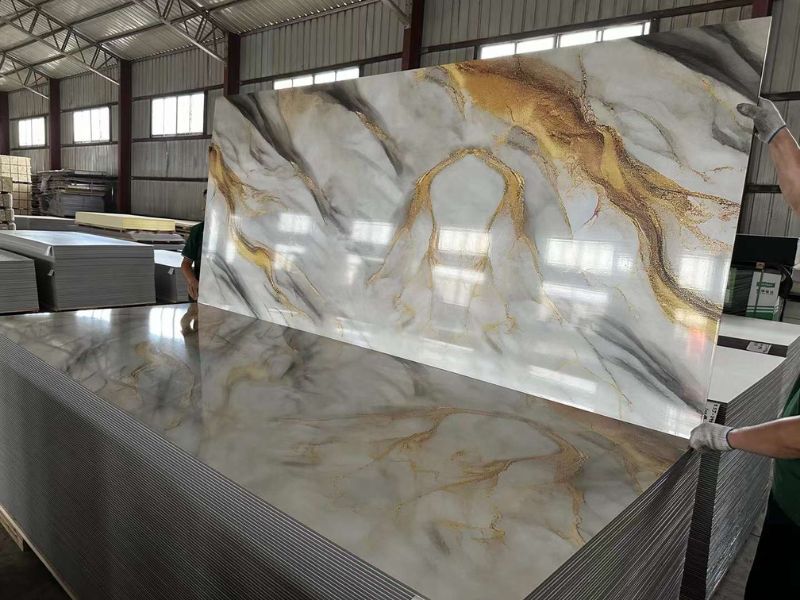
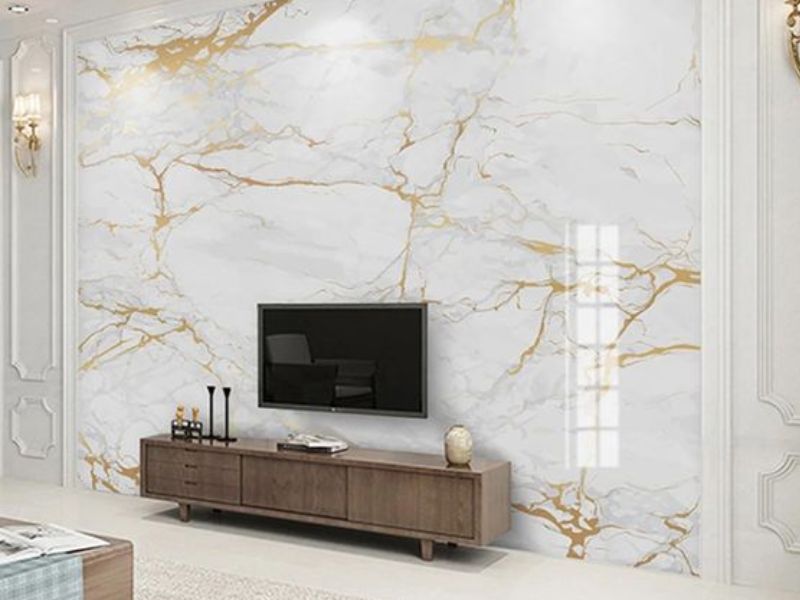
Q&A
What is the production capacity of the PVC marble sheet production line?
Can the production line produce sheets of different sizes and thicknesses?
What raw materials are required for the production line?
How long does it take to install and commission the production line?
Installation and commissioning typically take 10-15 days, depending on the complexity of the production line. Our engineers provide on-site support and training during this period.
What is the lead time for ordering your PVC marble sheet production line?
The normal lead time is approximately 30-60 working days after receiving the down payment. The specific time depends on the model and configuration of the production line. We will do our best to ensure timely delivery.
What after-sales services do we offer?
We provide comprehensive after-sales services, including equipment maintenance, spare parts supply, remote troubleshooting and on-site technical support. In addition, we also provide operator training, including equipment operation and raw material guidance.
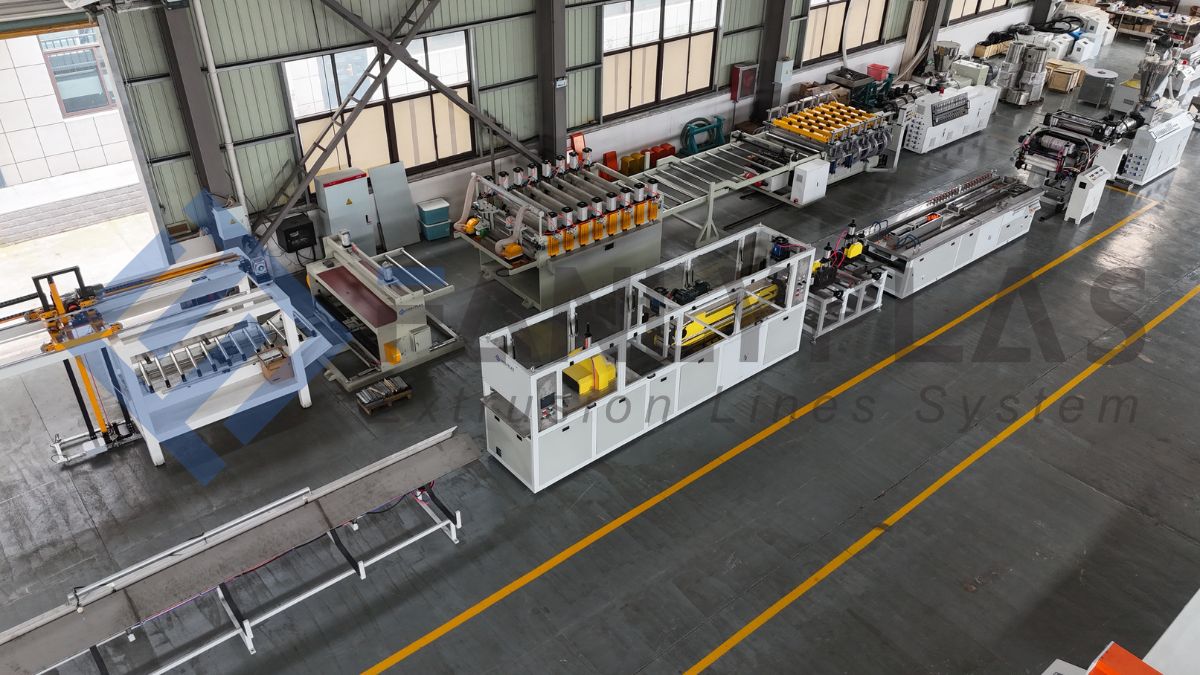
Why Choose Production Line from FANLYPLAS?
1
Superior Quality & Advanced Technology
ANLYPLAS is committed to providing high-quality PVC marble sheet production line, utilizing advanced extrusion technology and precise mold design to ensure stable and efficient operation, producing excellent PVC marble sheet to help you stand out in the market.
2
Customized Solutions & Professional Service
We have an experienced team that can provide tailor-made production line solutions based on your specific needs. Additionally, we offer comprehensive installation, training, and after-sales service to ensure the smooth operation of your production without any worries.
3
Continuous Innovation & Trustworthy Brand
FANLYPLAS, a well-known mechanical equipment production line brand from Shanghai, continuously invests in R&D to constantly optimize products and technologies. Choose us, and you will get reliable products and a long-term partnership.
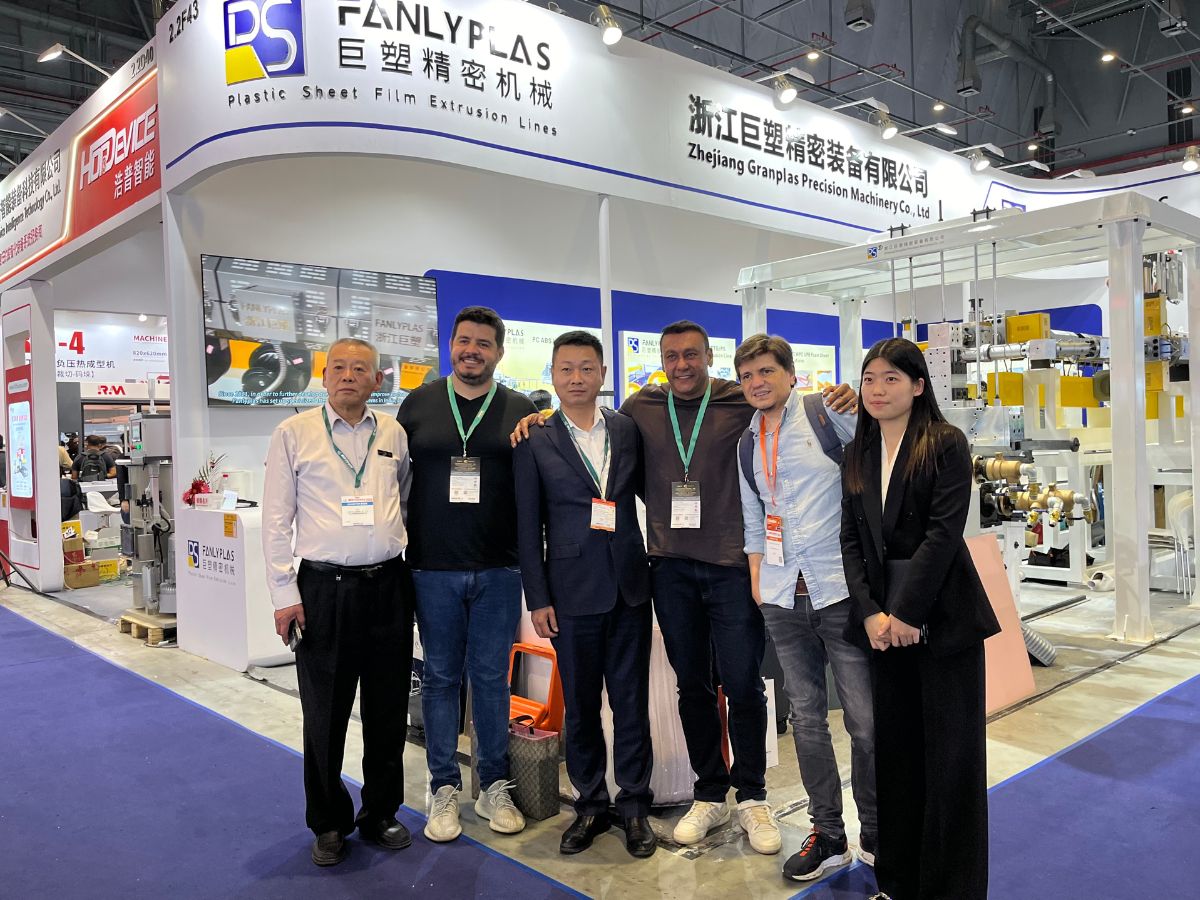
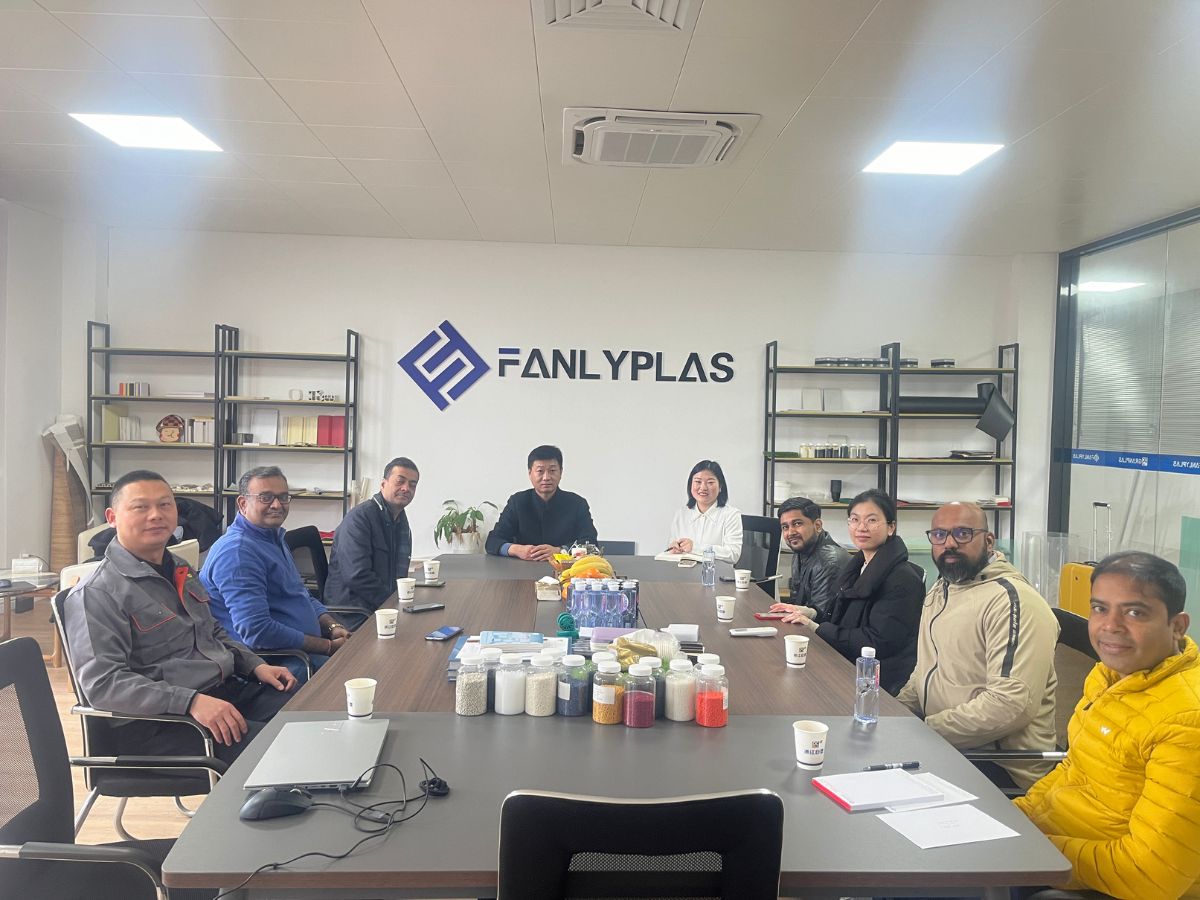
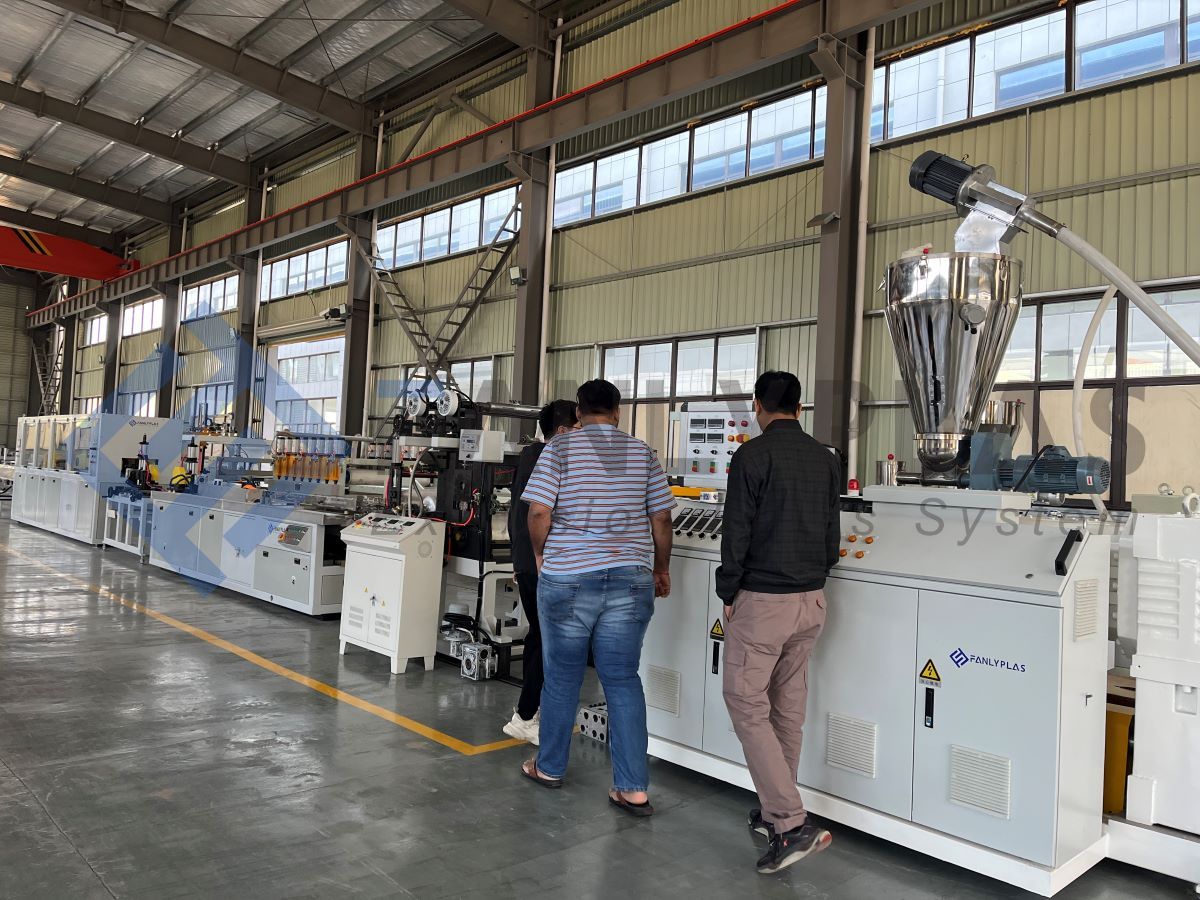
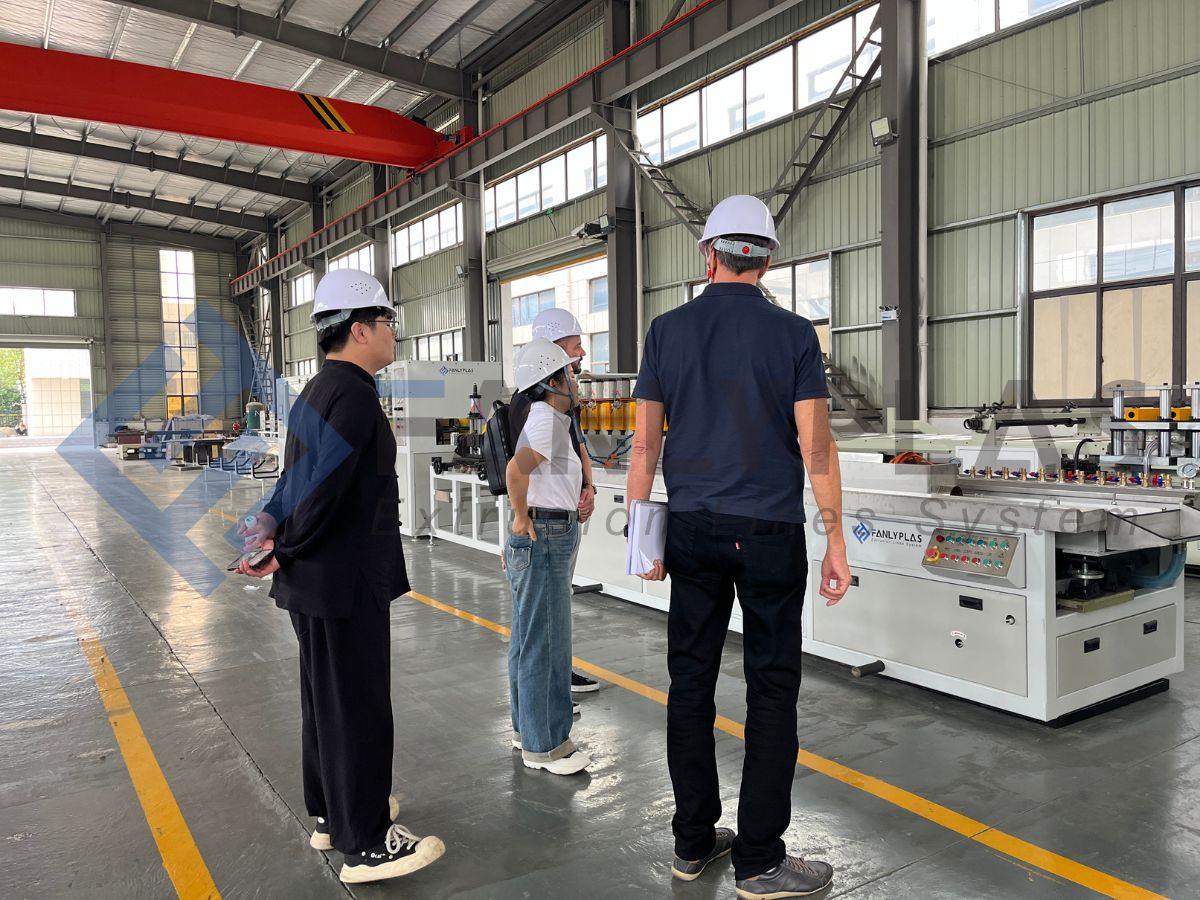
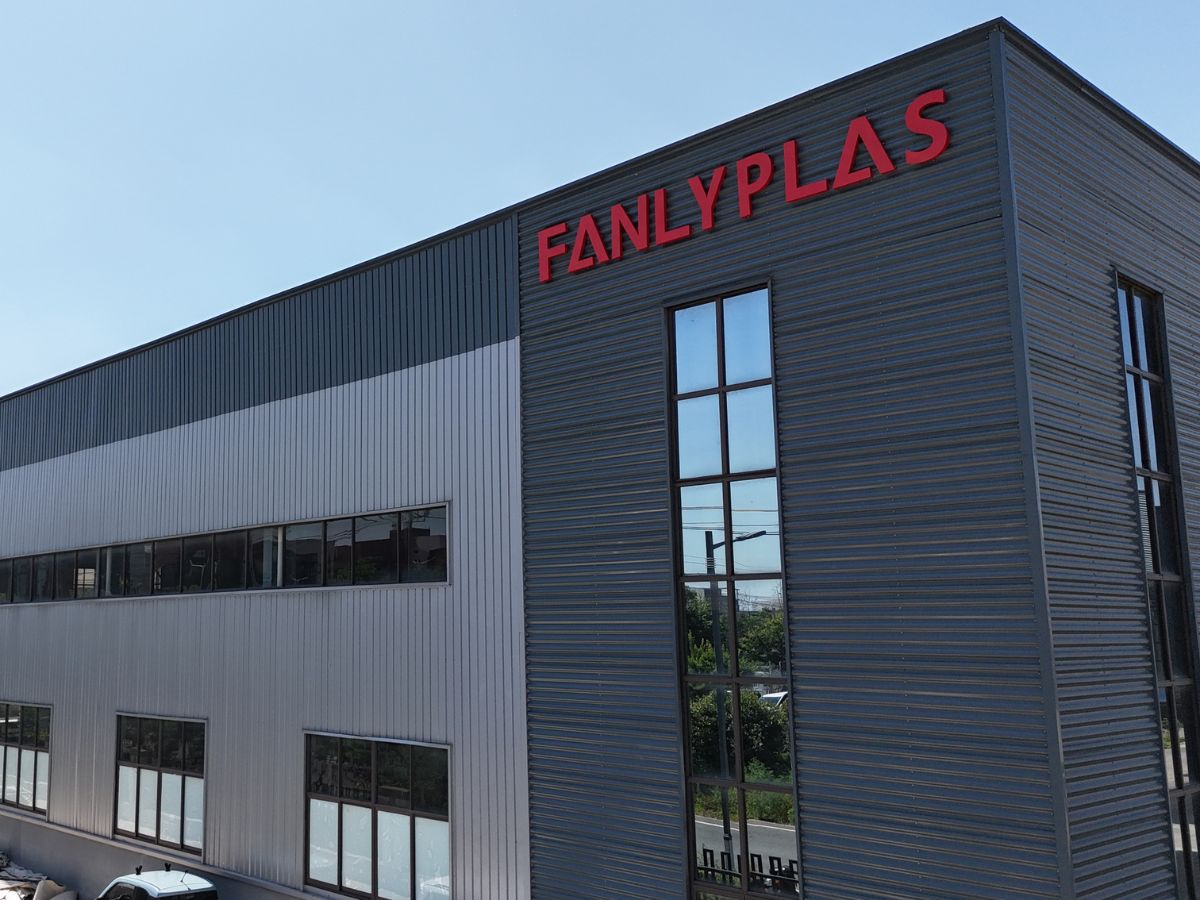
Contact Us for Your Solution!
Thank you for your interest in FANLYPLAS PVC marble sheet production lines! If you have any questions or requirements regarding our products, or if you would like to obtain a more detailed customized solution, please fill out the contact form below with your contact information and specific needs. Our professional team will contact you as soon as possible to provide you with the best quality service and support.