HIPS Sheet Extrusion Line
Be Green By Extrusion!

Applications and Features of FANLYPLAS HIPS Sheet Extrusion Line
Based in our stragtic cooperation with core components supplier and our own designs, we established a very strong system whatever in technology, machine quality stability and supplying capacity. With many successful cases we have supplied whatever in China local market or foreign market. Our HIPS Sheet Extrusion Line is a state-of-the-art manufacturing solution designed for producing high-quality HIPS sheets.Our extrusion line integrates advanced technologies to ensure excellent performance of screw designs, high efficiency, and precise control over sheet thickness and surface quality. With its reliable design and innovative features.
1.High Precision Production: The line ensures uniform thickness and consistent surface quality with advanced calibration and cooling systems.
2.Customizable Design: Flexible configuration options allow for the production of sheets in various sizes, thicknesses, and surface finishes to meet diverse industry needs.
3.Energy Efficiency: Equipped with energy-saving components, the production line reduces power consumption while maintaining high output.
4.User-Friendly Operation: Automated controls and intuitive interfaces simplify operation, minimizing labor requirements and enhancing productivity.
Equipment Composition of FANLYPLAS HIPS Sheet Extrusion Line
FANLYPLAS offers customized HIPS Sheet Extrusion Line based on customer requirements, including product specifications, production volume, facility size, and desired level of automation. We provide flexible configurations to meet various needs. Below are some of the standard configurations available for FANLYPLAS HIPS Sheet Extrusion Line.
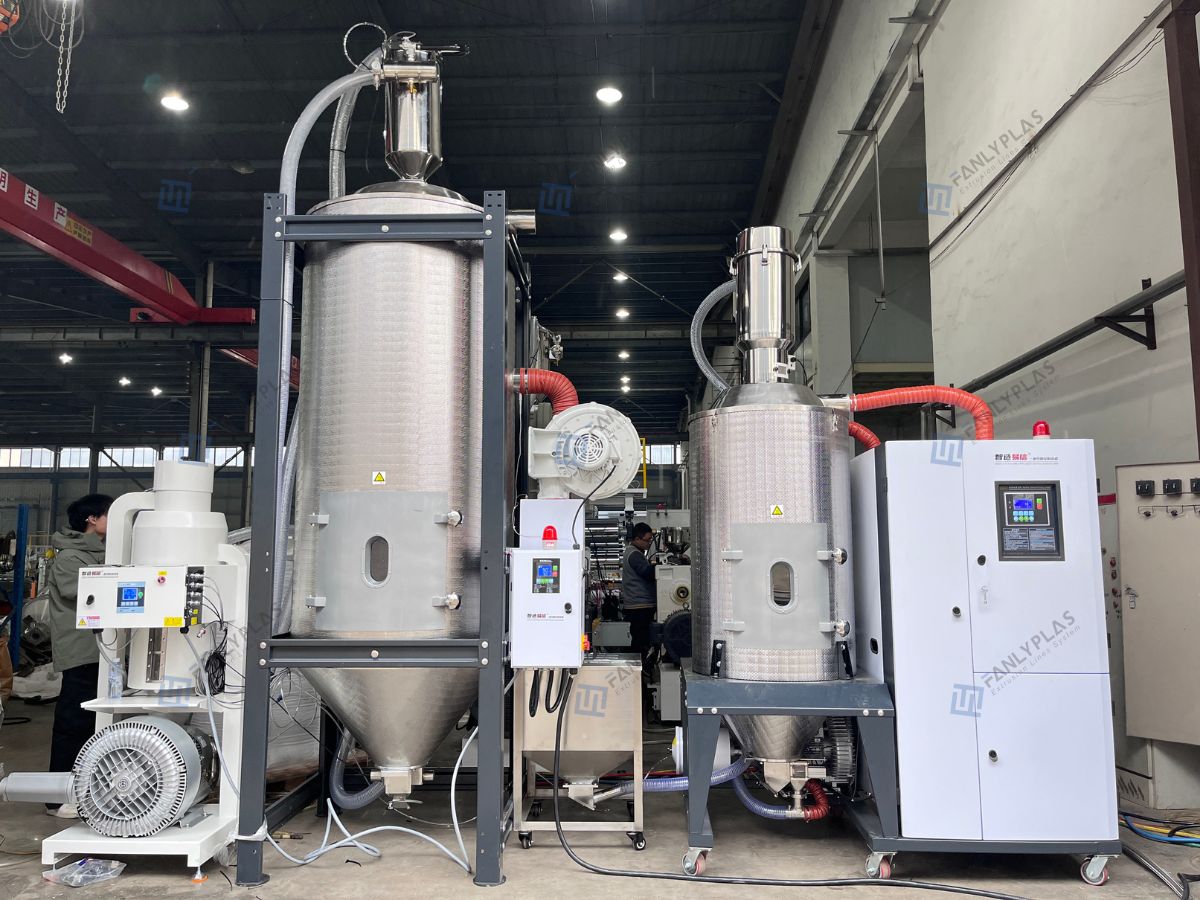
Dehumidifier and dryer system
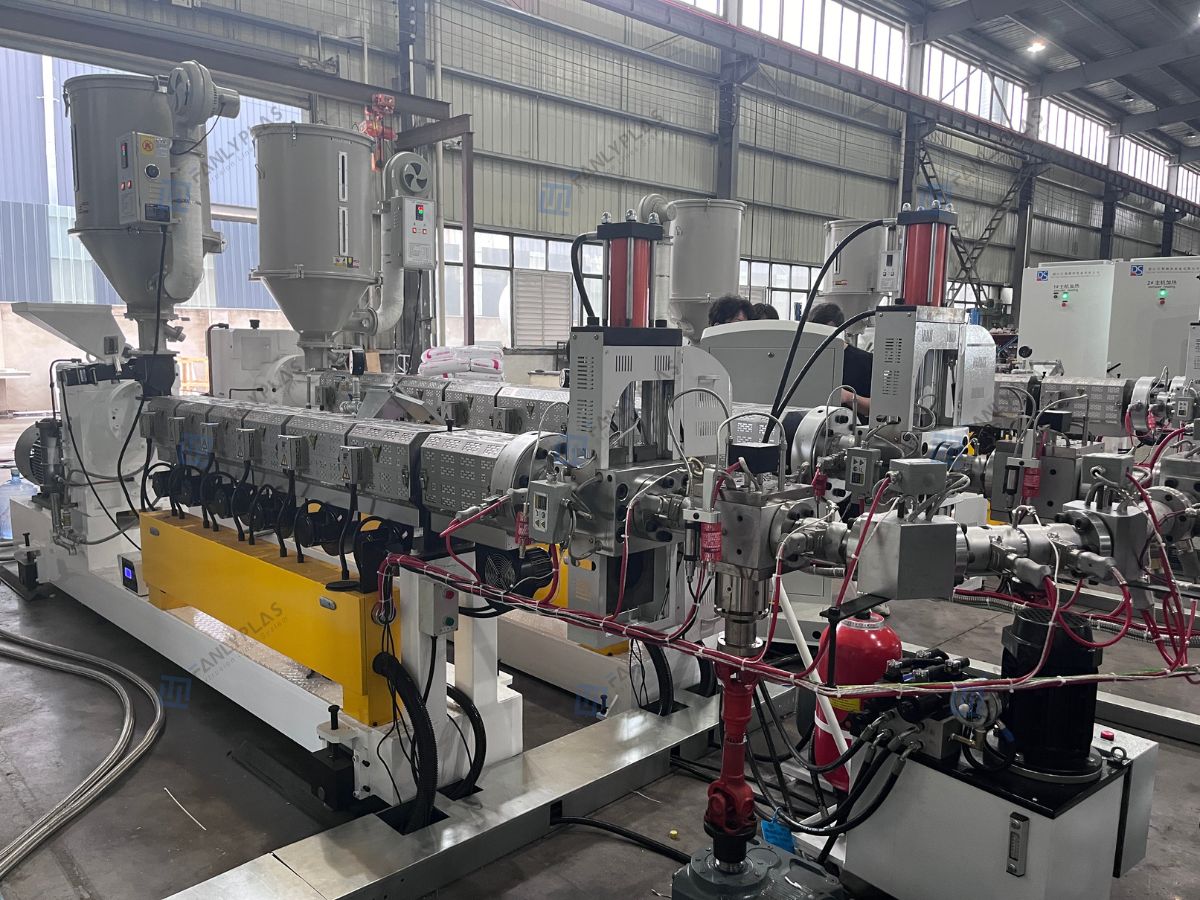
Extruder
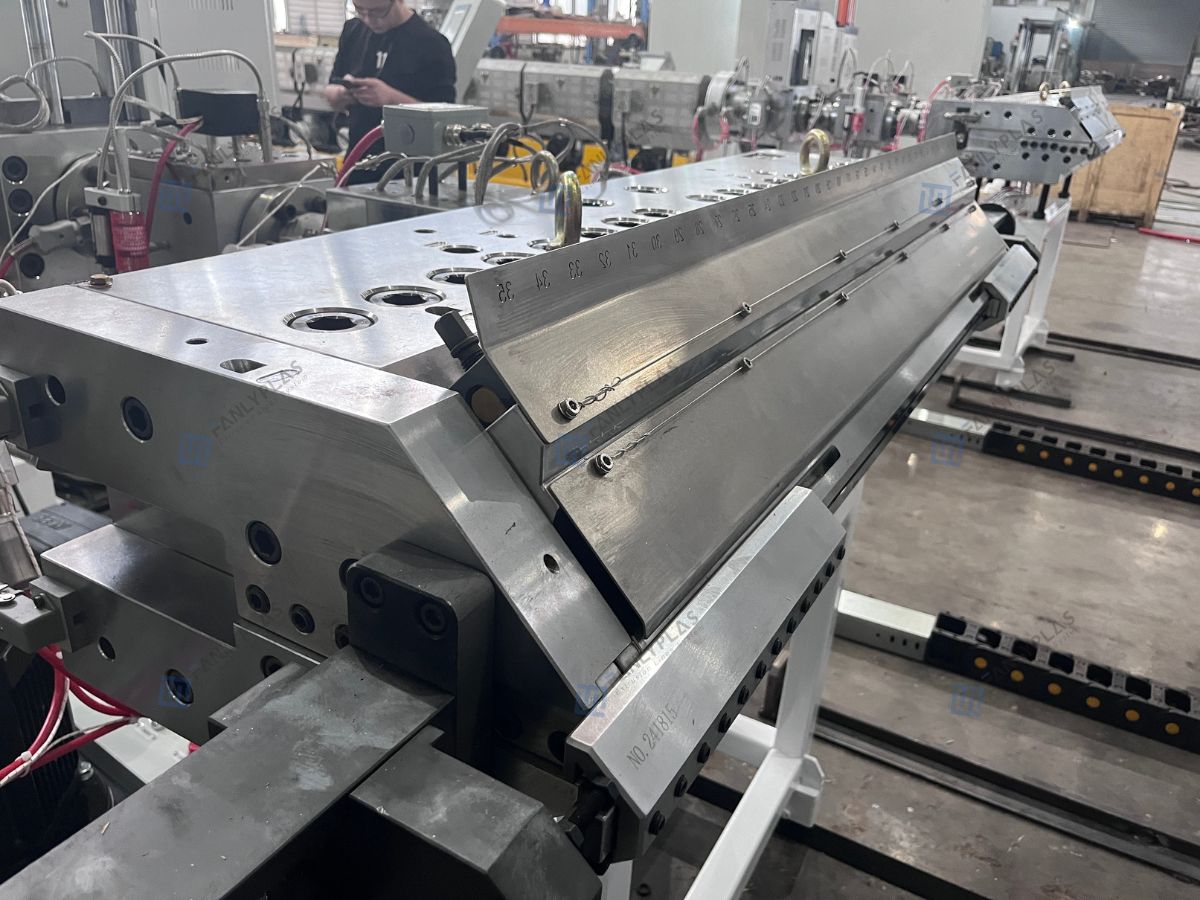
Die Head
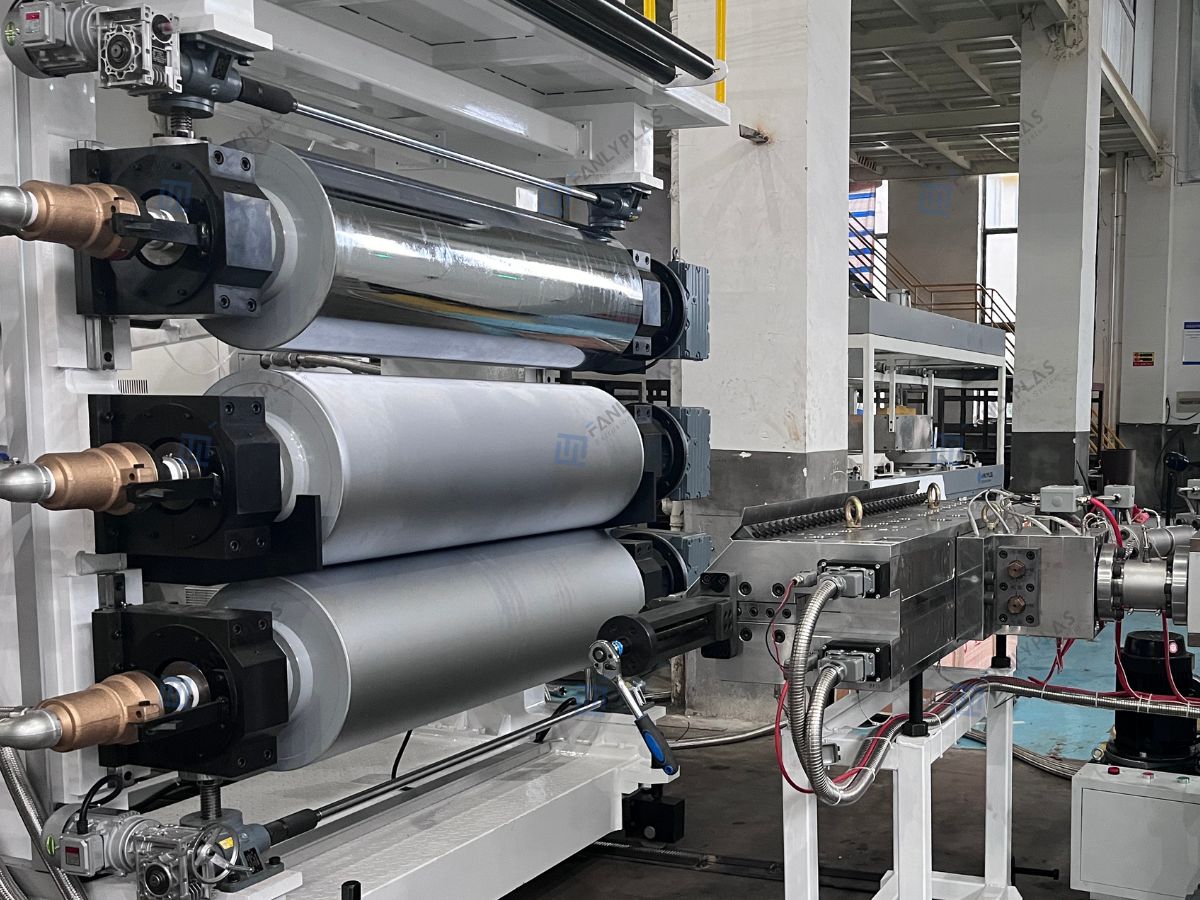
Three-Roller Calender
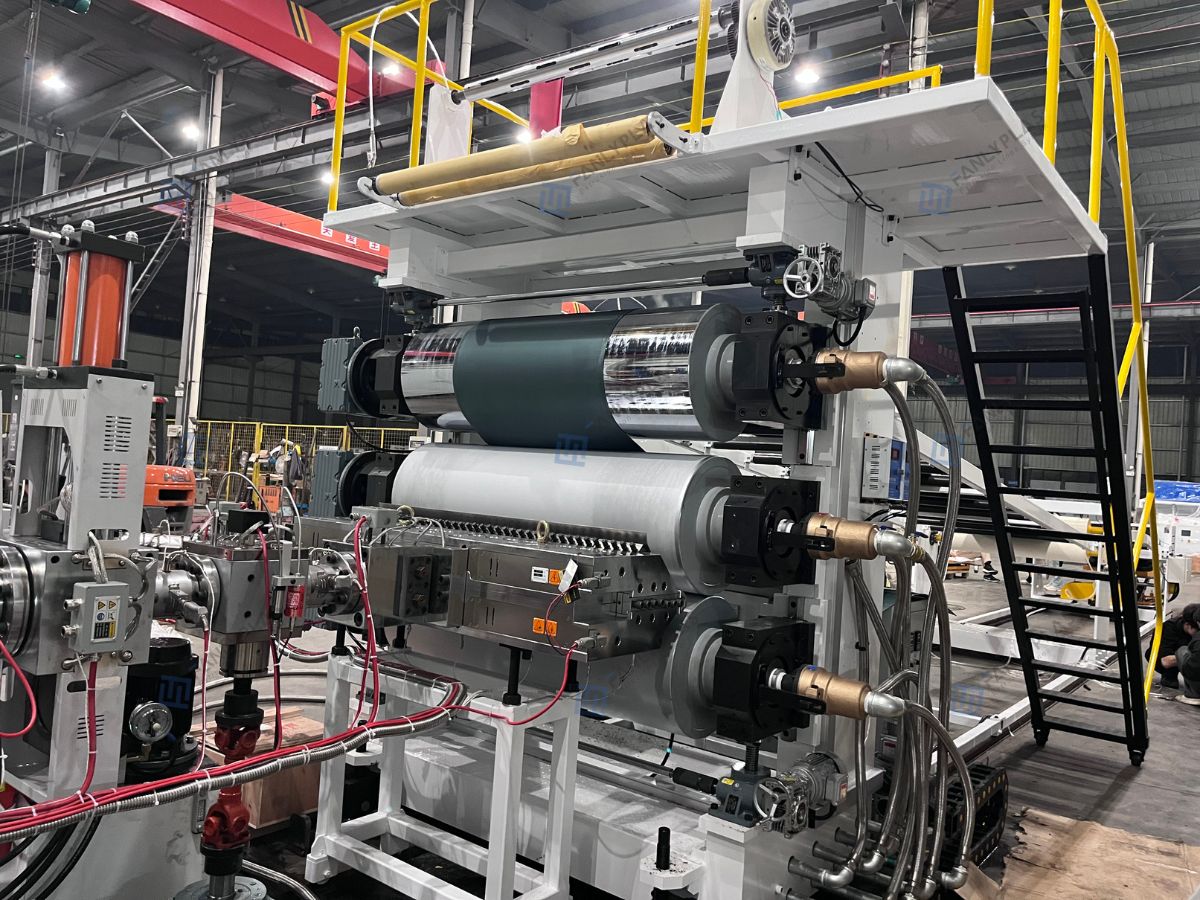
Lamination Unit Platform
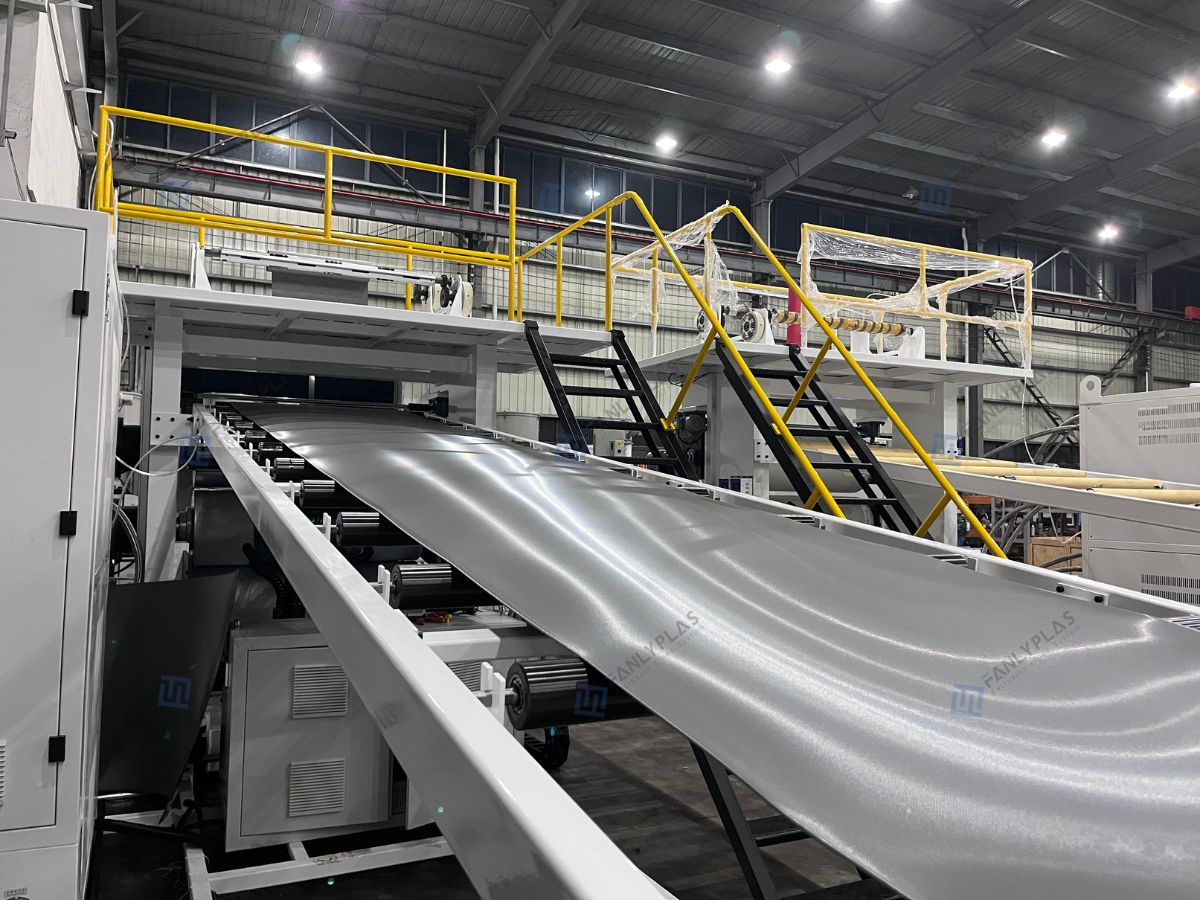
Cooling Bracket
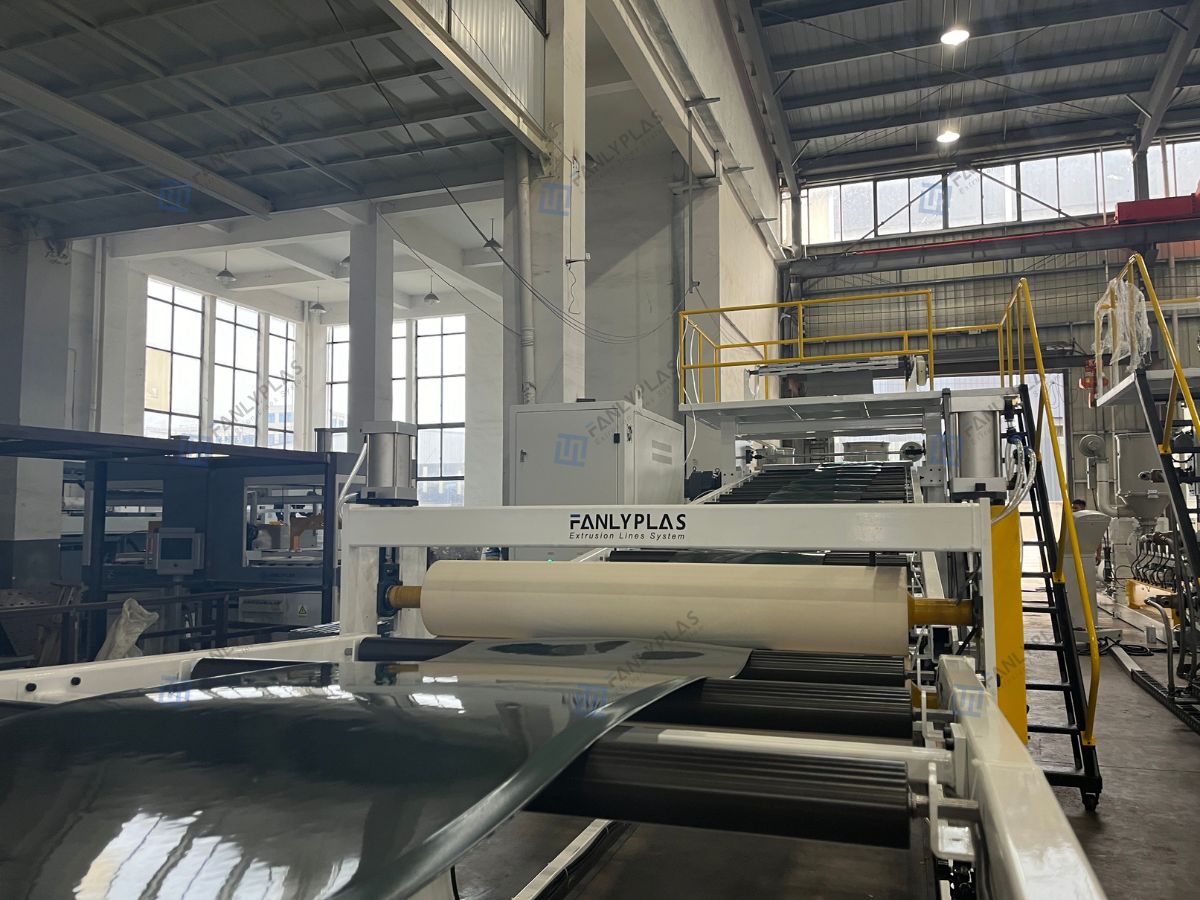
Tractor
The tractor pulls the sheet through the production line at a controlled speed. It ensures steady tension, preventing deformation and maintaining uniform sheet quality.
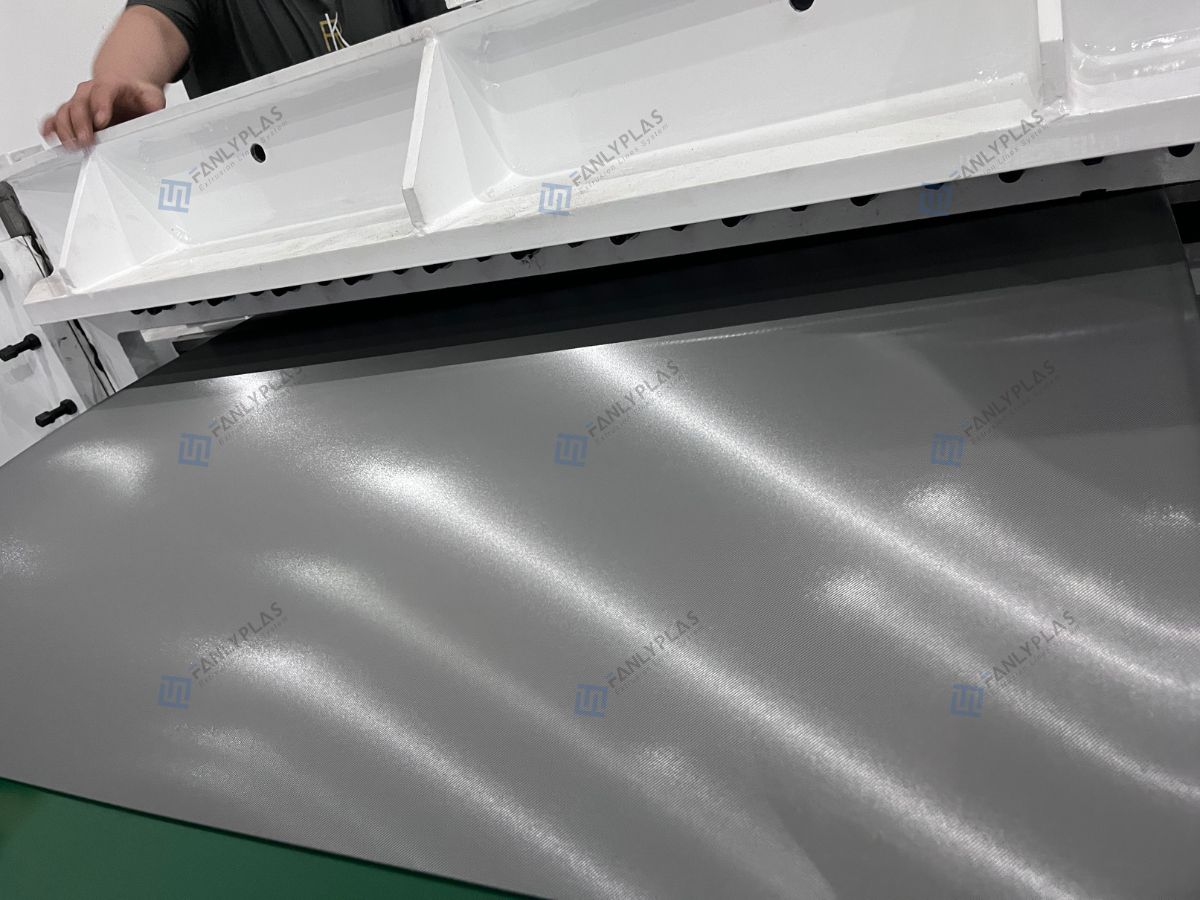
Cutting Machine
The cutting machine precisely cuts the sheet into desired lengths. It offers flexibility to produce sheets of various sizes and ensures clean, burr-free edges.
FANLYPLAS HIPS Sheet Extrusion Line Workflow
Raw Material Loading
Material Melting and Mixing
Sheet Forming
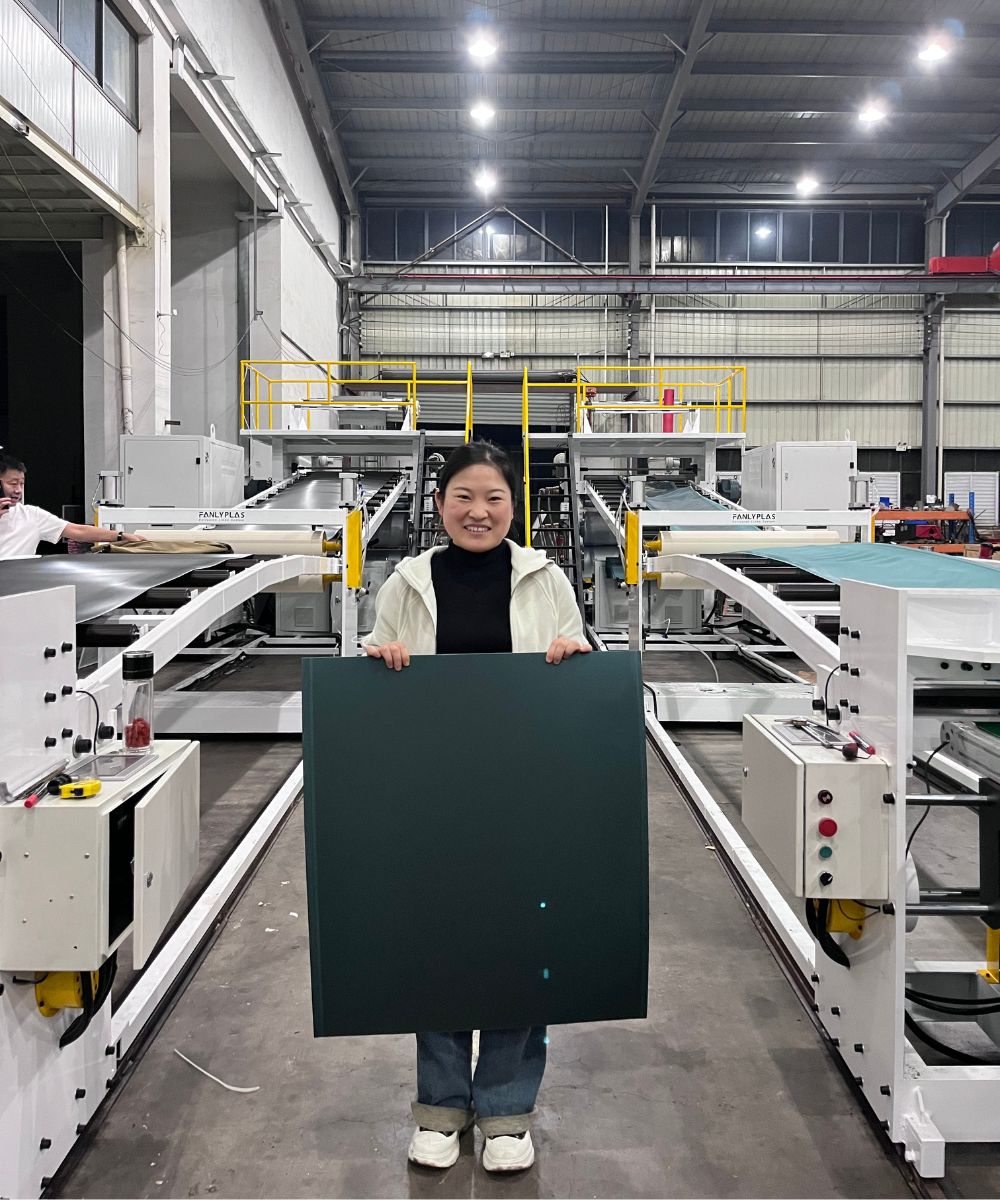
Surface Refinement
Cooling and Stabilization
Cutting and Finishing
Performance and Applications of HIPS Sheets
HIPS sheet is a popular and cost-effective plastic material due to its light weight, impact resistance, easy processing, good dimensional stability, moisture resistance and easy bonding with other materials.
1.Product Packaging: Due to its light weight, moisture resistance, and ability to be easily molded into different shapes and sizes.
2.Signage and Displays: HIPS is a popular choice for signs and displays due to its good dimensional stability, allowing it to maintain its shape even under varying temperatures and humidity.
3.Automotive Interiors: Due to its strong impact resistance and ease of manufacturing, HIPS is used to manufacture some automotive interiors, including dashboard components.
4.Toys: HIPS is used to manufacture toys and other children’s products because it is lightweight, impact-resistant, and can be easily molded into different shapes and colors.
5.Medical Devices: Due to its high impact resistance, light weight, and ease of processing, HIPS is used to manufacture a variety of medical devices, including orthopedic splints.
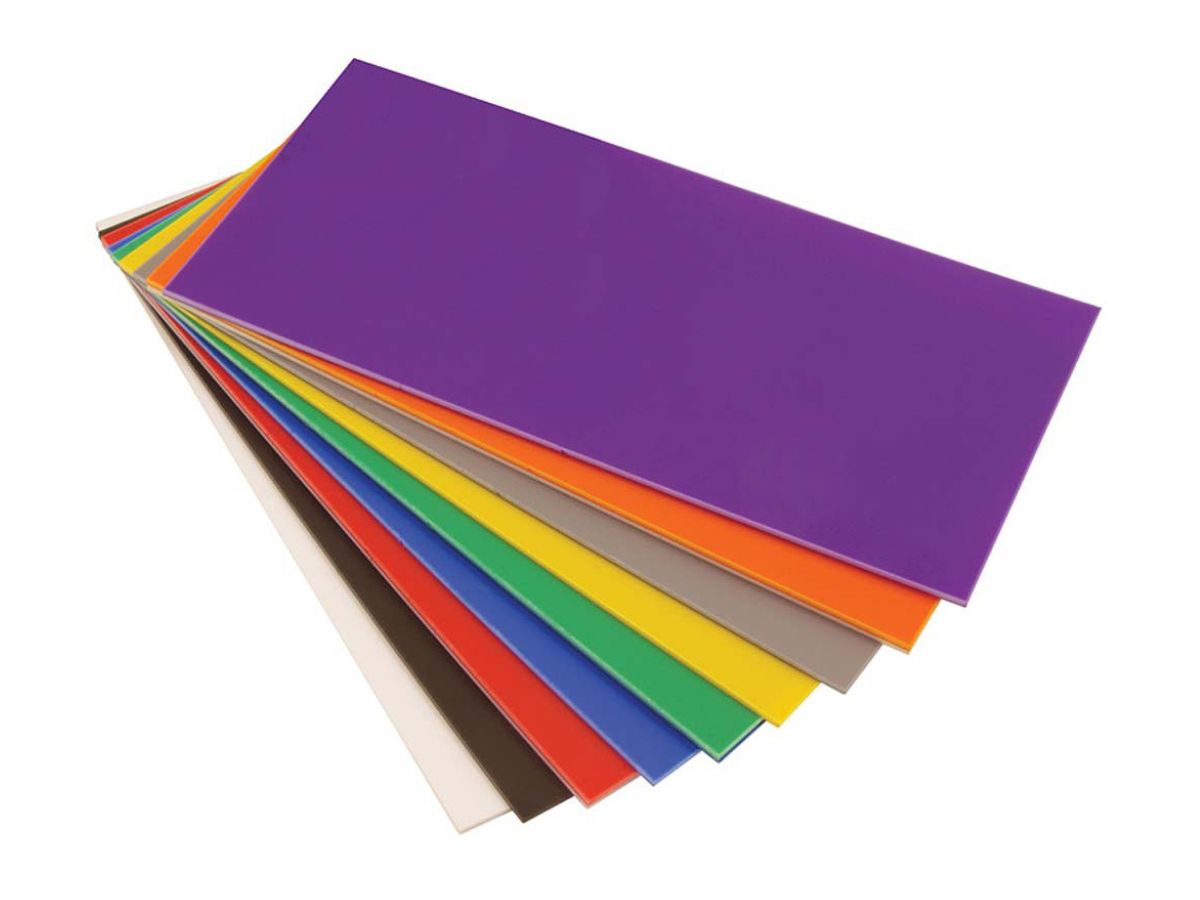
FAQS
What is the maximum sheet width and thickness your Extrusion line can produce?
Our HIPS Sheet Extrusion Line can produce sheets with a maximum width of 2100mm and a thickness range of 1mm to 12mm. Customizations are available to meet your specific requirements.
What types of raw materials are compatible with this extrusion line?
The Extrusion line is designed to handle high-quality HIPS raw materials, as well as their blends. It ensures efficient processing and consistent quality for various formulations.
How do you ensure the quality of the sheets produced by this line?
Our production line incorporates advanced technologies like precise screw design, high-quality die heads, and automated calibration systems. Additionally, rigorous testing and quality control protocols are implemented to ensure consistent thickness, surface finish, and mechanical properties.
How energy-efficient is your Extrusion line?
Our extrusion line is equipped with energy-saving components, such as high-efficiency motors, optimized heating systems, and smart control technologies. These features minimize energy consumption while maintaining high output.
What kind of after-sales service do you provide?
We offer comprehensive after-sales support, including on-site installation, training for operators, regular maintenance, and 24/7 technical assistance. Spare parts are also readily available for quick replacement.
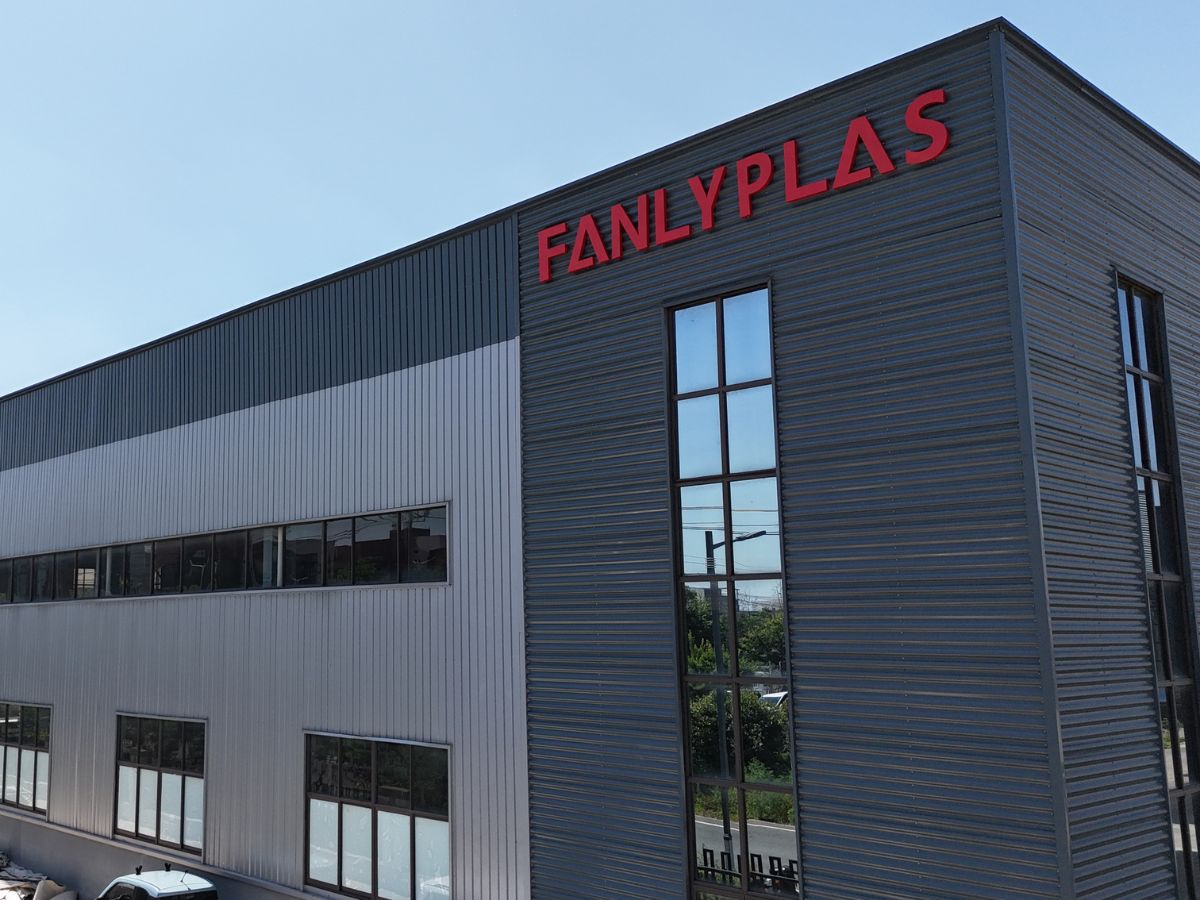
Get Extrusion Solutions Or Service Today?
Just leave your needs & questions here, we will back you in short time. (The more details you leave, the better quotation will reach you soon)