WPC Foam Board Production Line
Be Green By Extrusion!
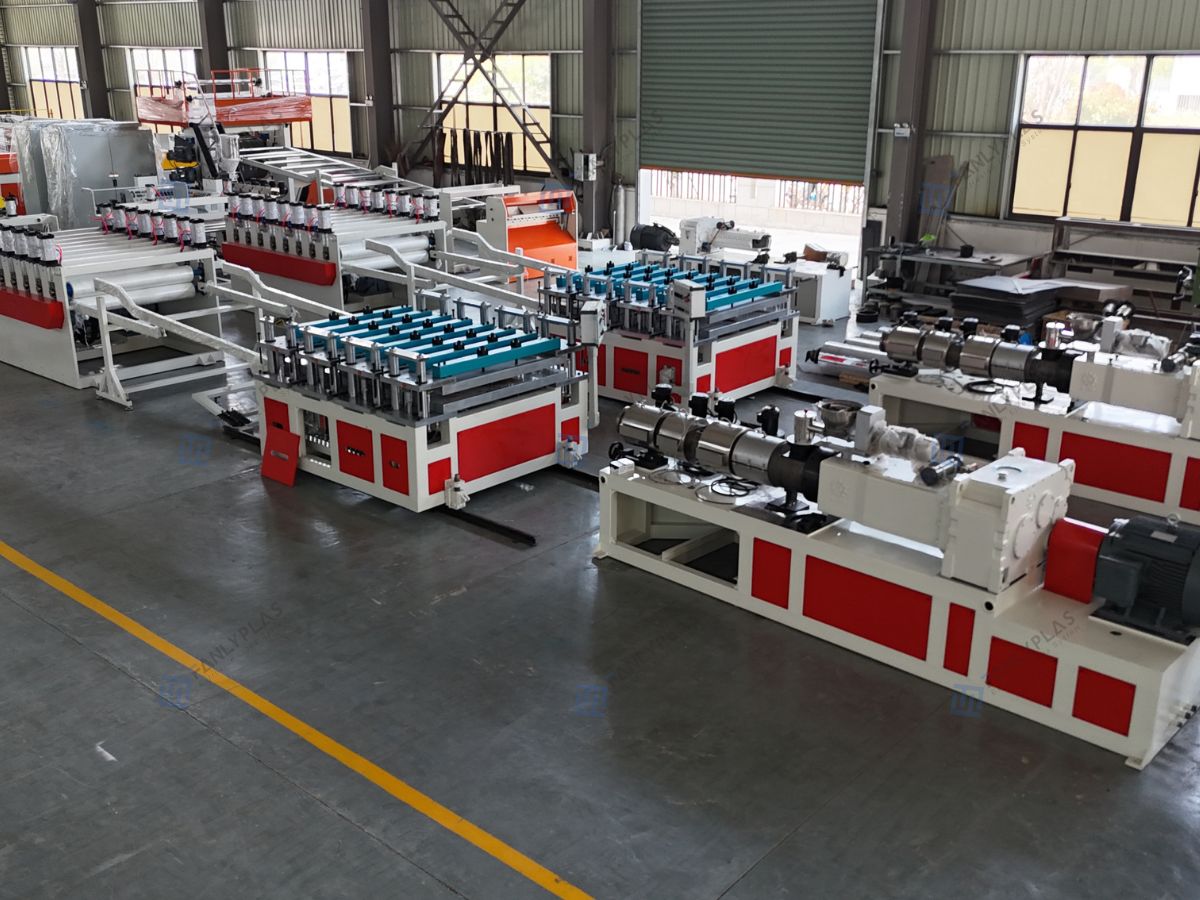
Introduction of Our WPC Foam Board Production Line
1
Applications : Our FANLYPLAS WPC foam board production line manufactures boards with thicknesses from 3 to 40mm, suitable for diverse applications. Thinner boards are ideal for wall panels and advertising, while thicker options are perfect for cabinet and door manufacturing. These versatile boards offer excellent performance in various construction and furniture applications.
2
Production Flow :The FANLYPLAS WPC board production line ensures continuous production, starting with a special twin-screw extruder and mould. The process includes a calibrating platform, cooling frame, haul-off machine, cutting machine, and stacker. For A+B+A three-layer co-extrusion boards, additional extruders and distributors can be added. Incorporating a water chiller further enhances production efficiency.
3
Line Features :The newly designed FANLYPLAS WPC foam board making machine offers higher output and lower power consumption. It features a compact twin-screw extruder with superior performance. Our screws, barrels, and dies are designed in-house and made by world-renowned manufacturers. We also provide the best material formulation and comprehensive technical support.
Equipment Composition of FANLYPLAS WPC Foam Board Extrusion Line
FANLYPLAS offers customized WPC foam board extrusion line based on customer requirements, including product specifications, production volume, facility size, and desired level of automation. We provide flexible configurations to meet various needs. Below are some of the standard configurations available for WPC foam board extrusion line.
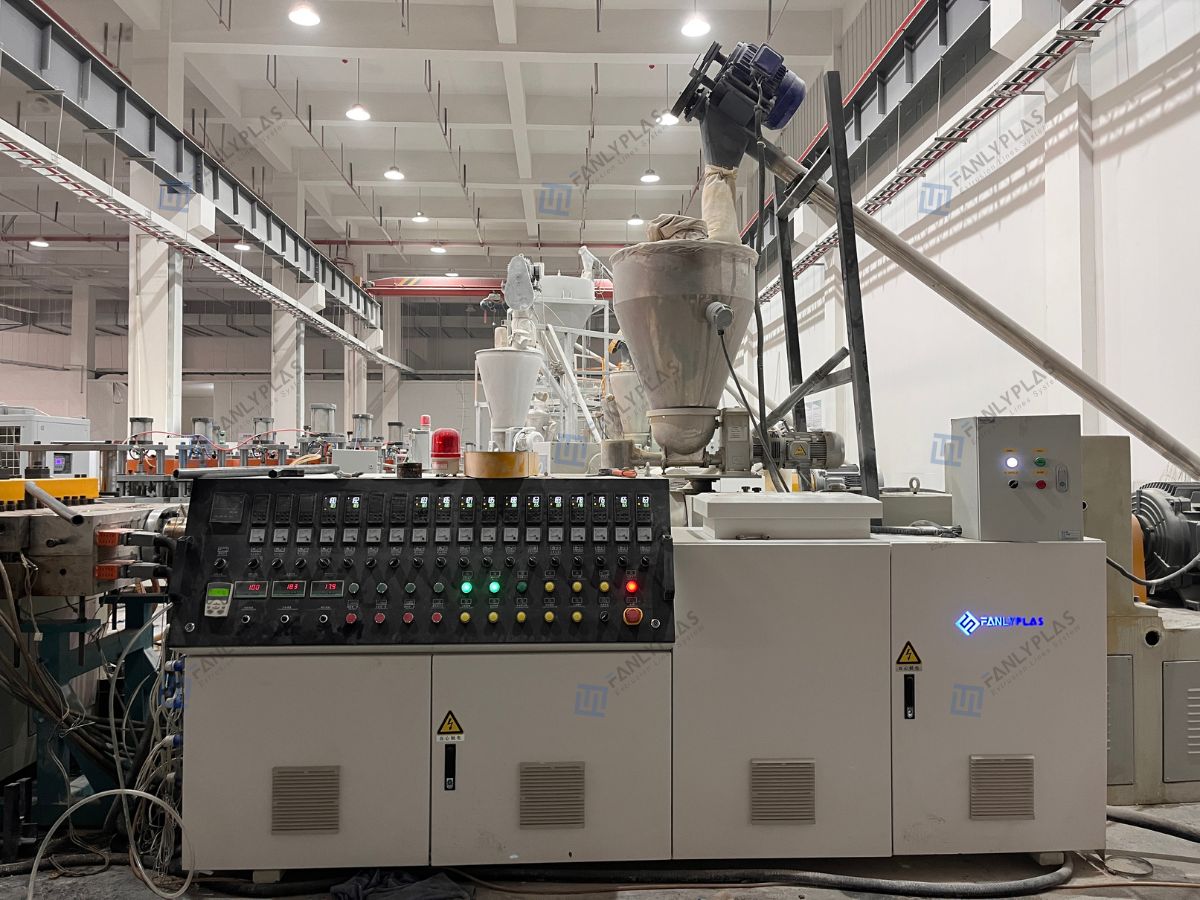
Extruder
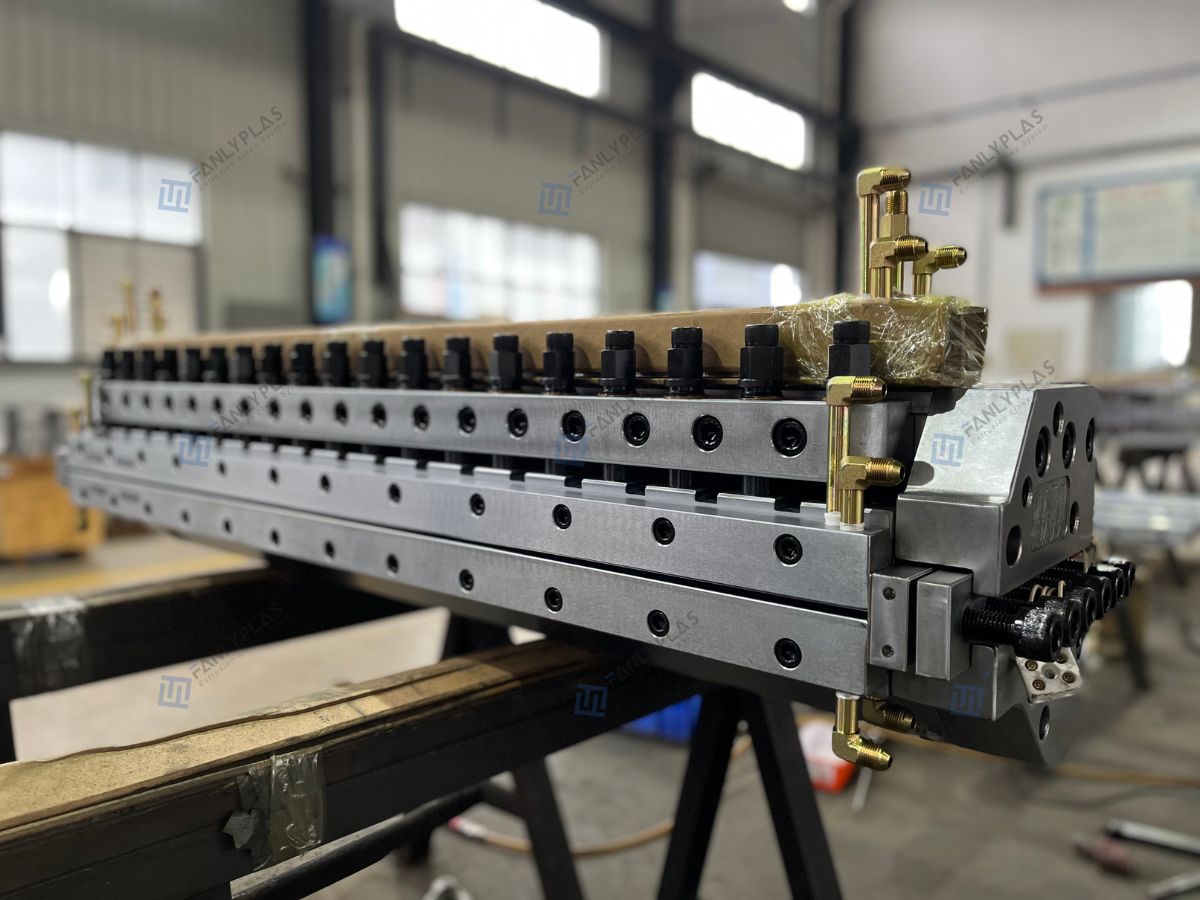
T-Die
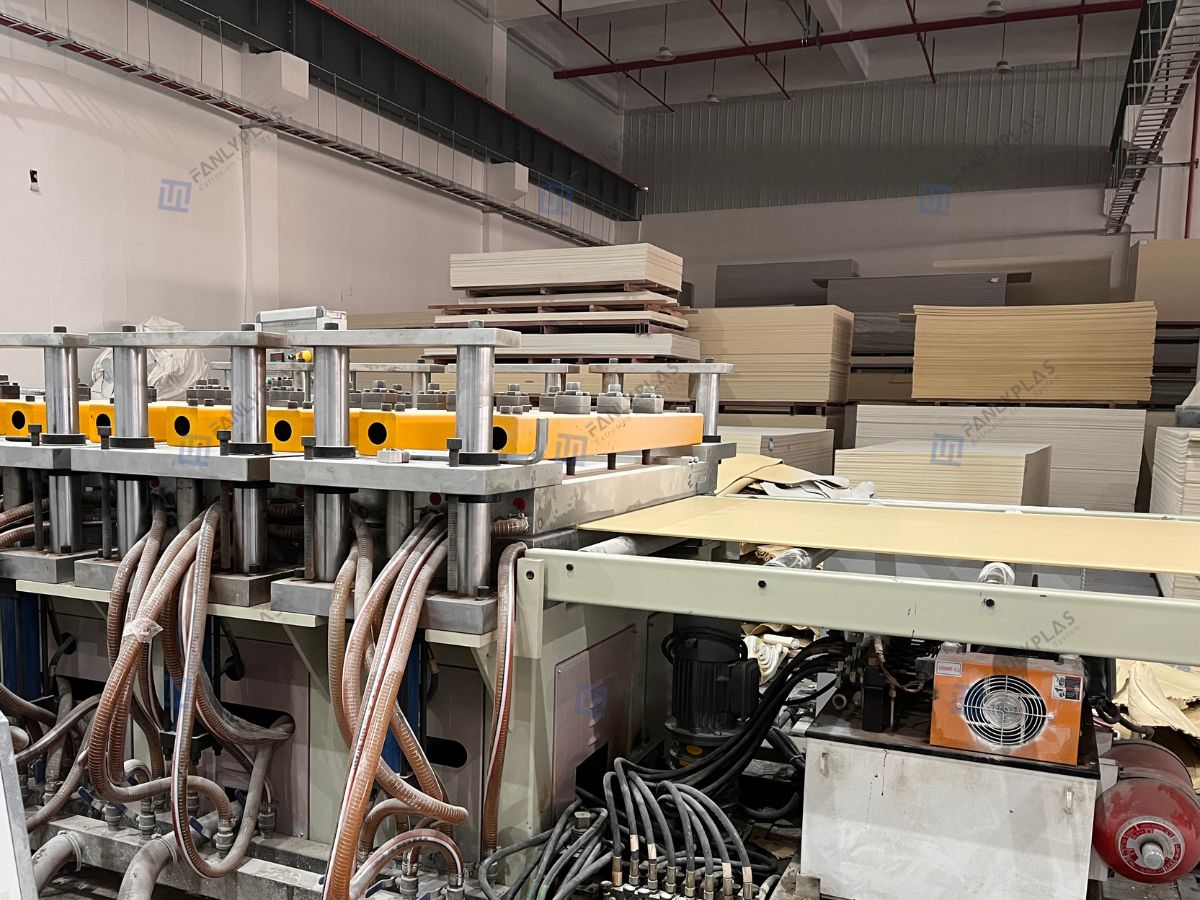
Calibration table and Cooling Bracket
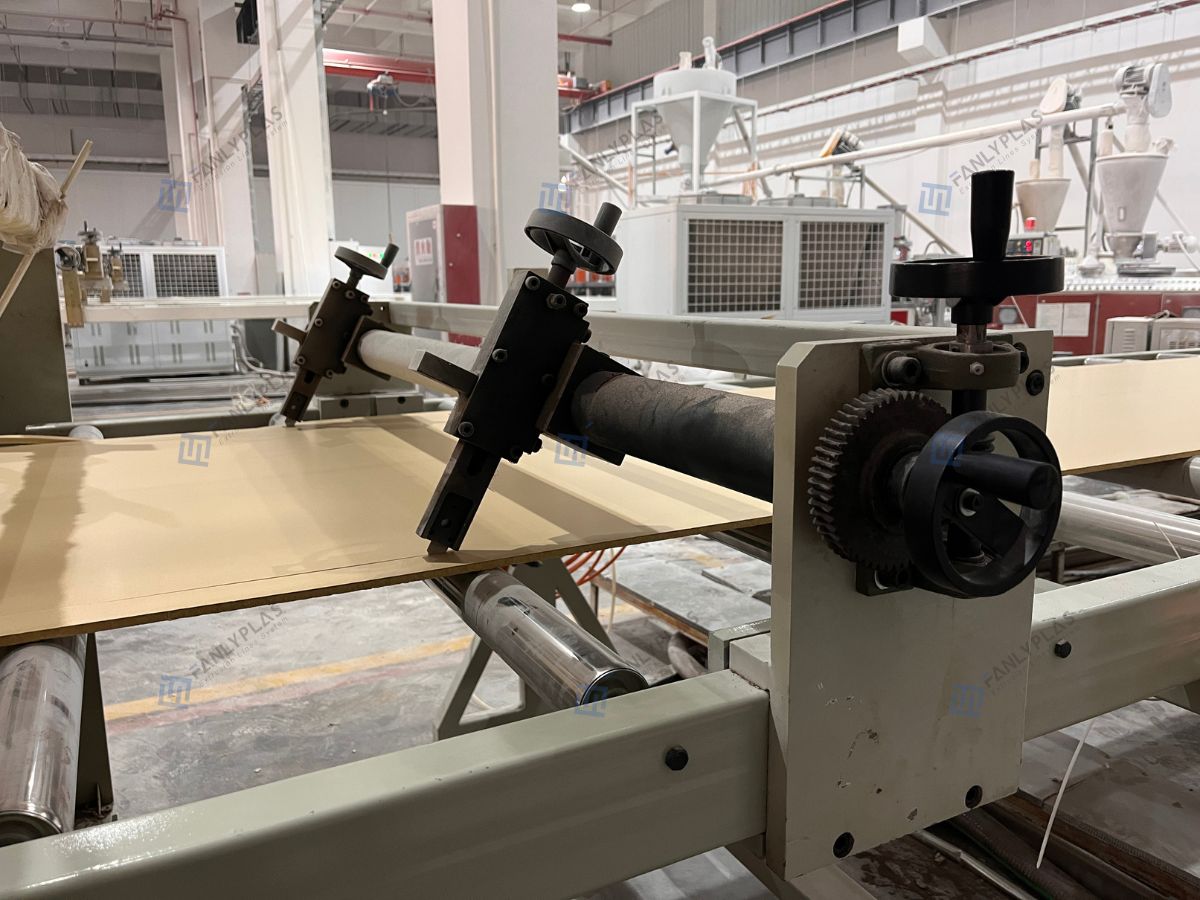
Edge cutting device

Haul-off unit with Top film lamination device
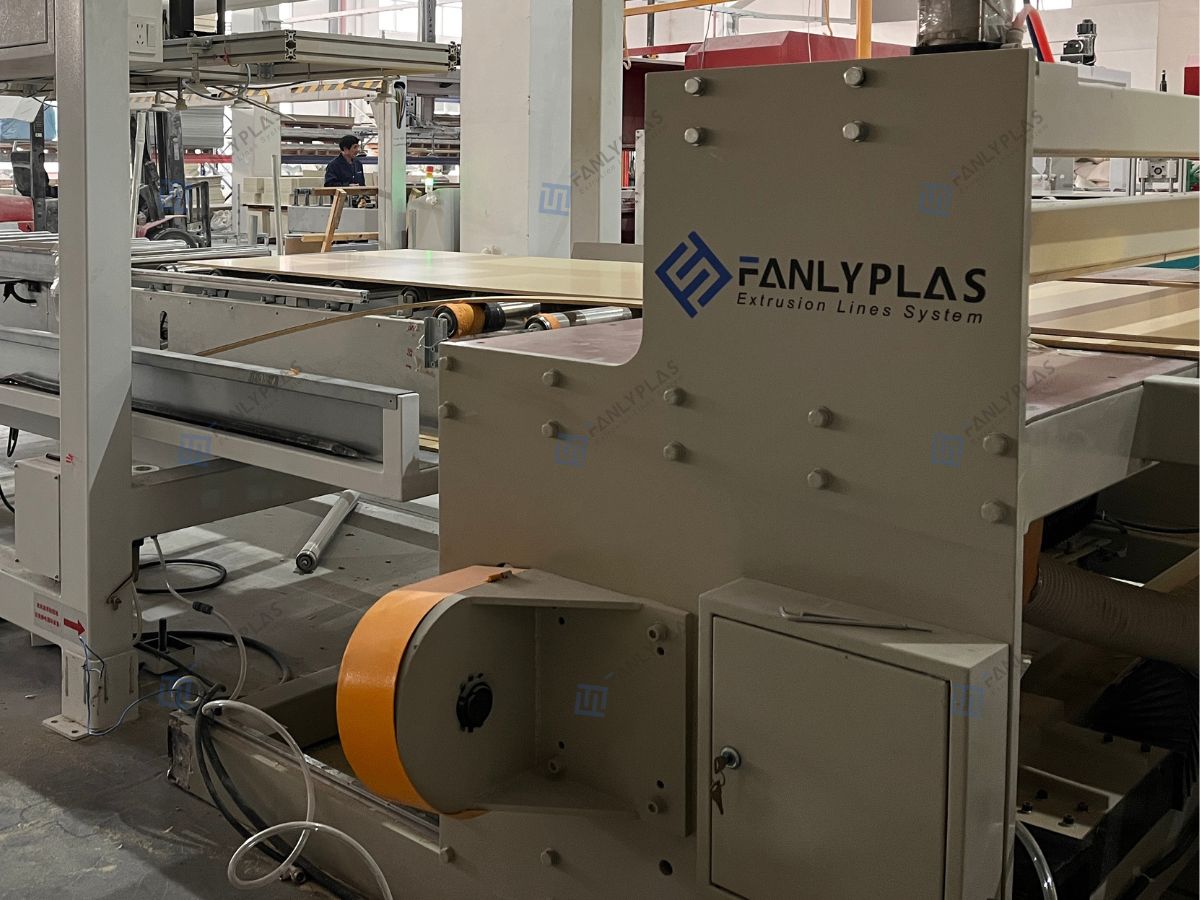
Cutting unit with Dust collector
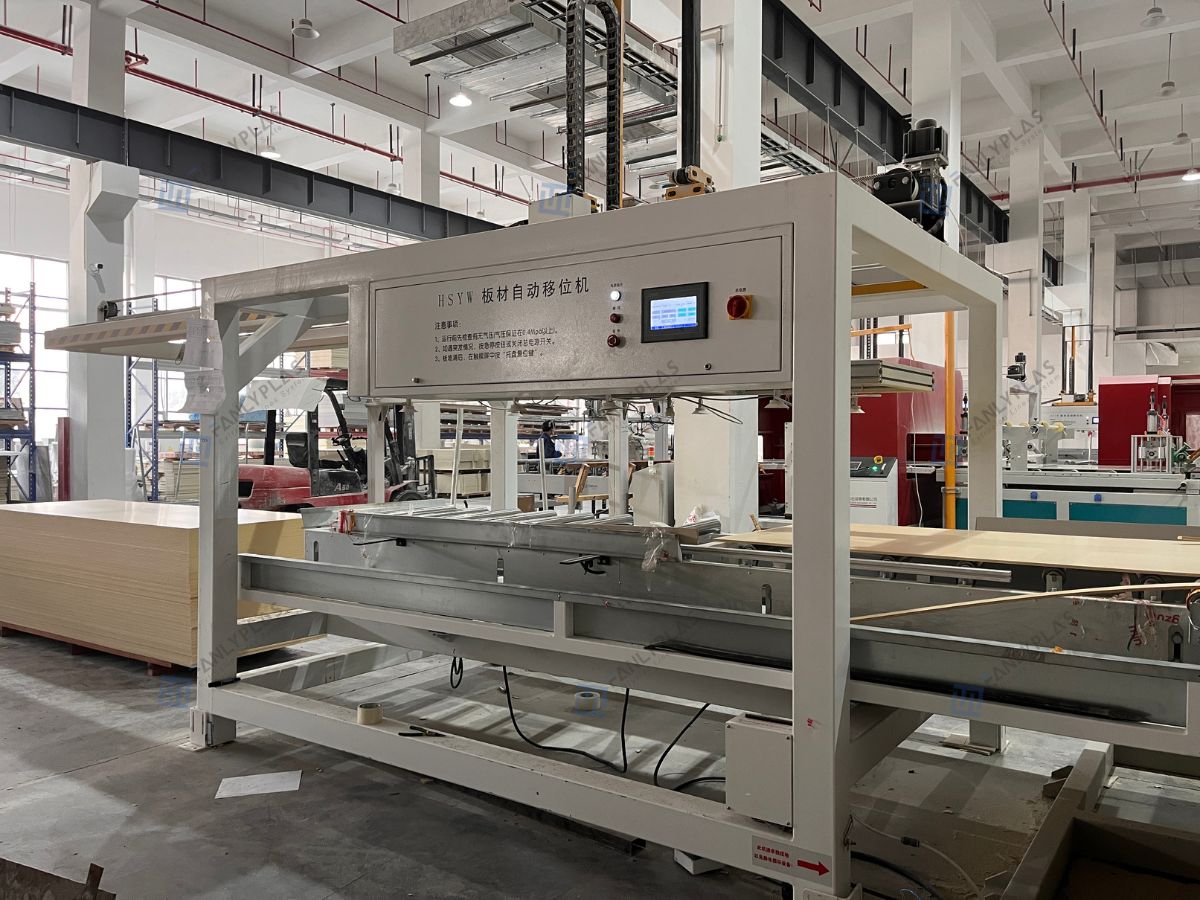
Auto Stacker
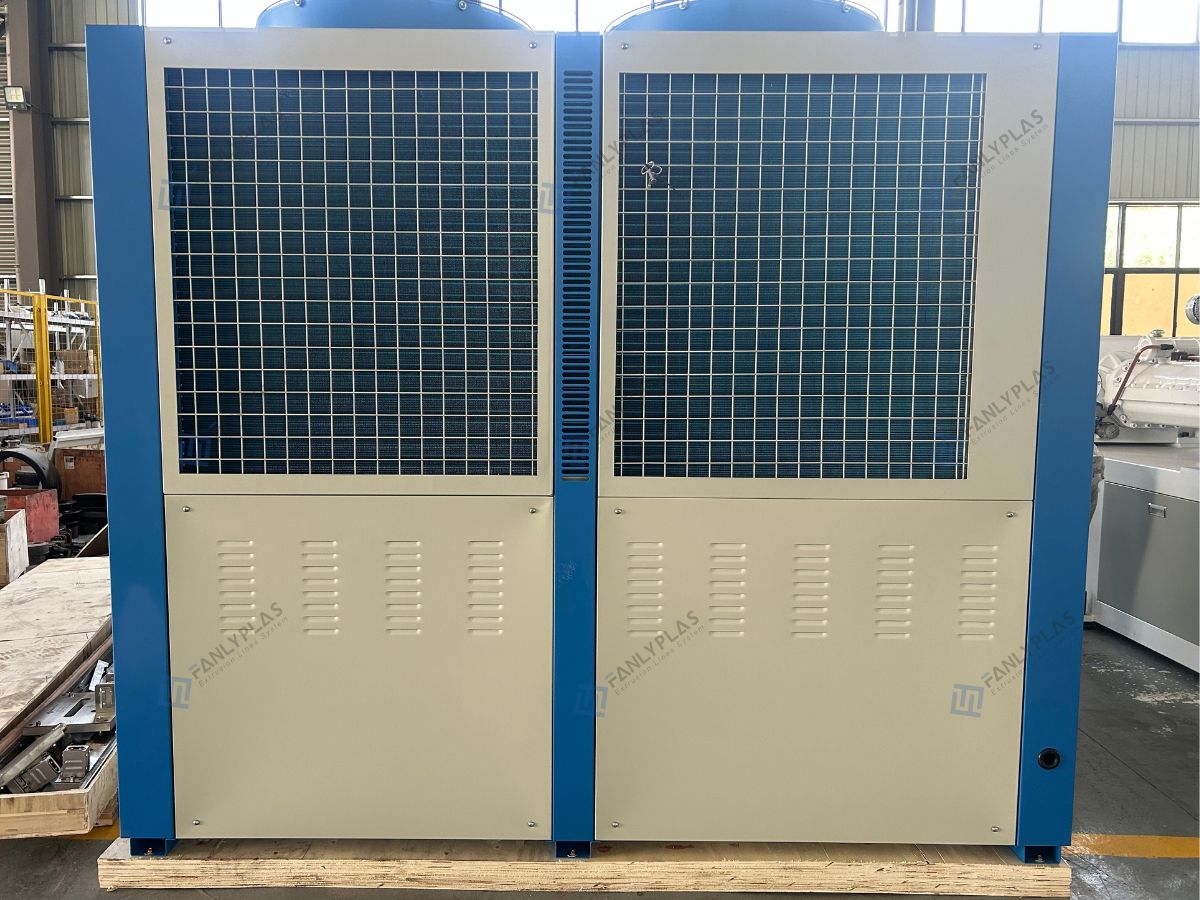
Water Chiller
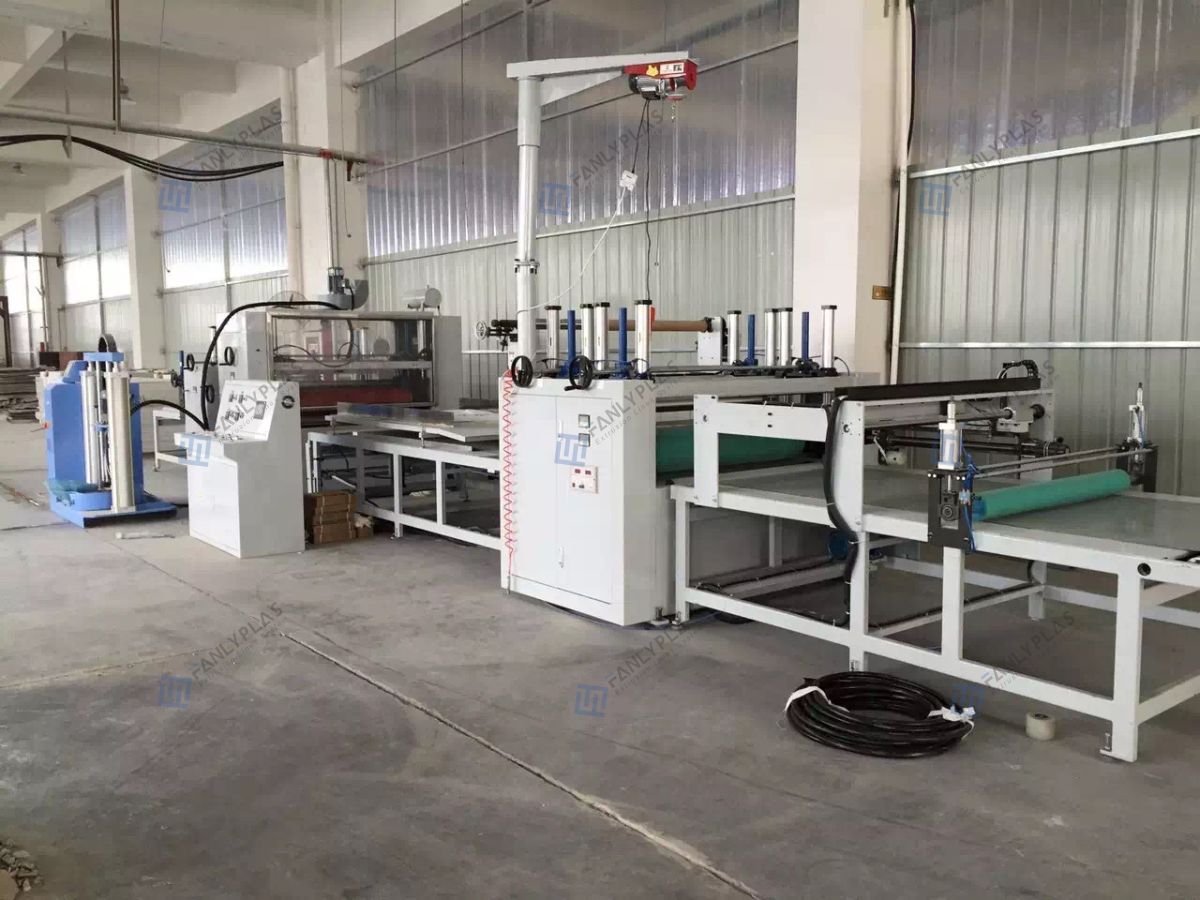
PVC Film Laminating Machine for WPC Foam Boards
Our FANLYPLAS PVC film laminating machine enhances WPC foam boards with vibrant colors and durable protection, offering resistance to scratches, wear, moisture, and UV. It can be configured for online or offline lamination based on production needs. Ideal for interior wall panels, furniture, and more, the machine ensures precise lamination through heated rollers or vacuum systems, providing a strong bond. Features include tension control, uniform heating, and user-friendly operation.
WPC Foam Board Production Line Auxiliary machinery
Beyond the core production line, FANLYPLAS offers a range of essential auxiliary machinery to optimize your WPC foam board manufacturing process.
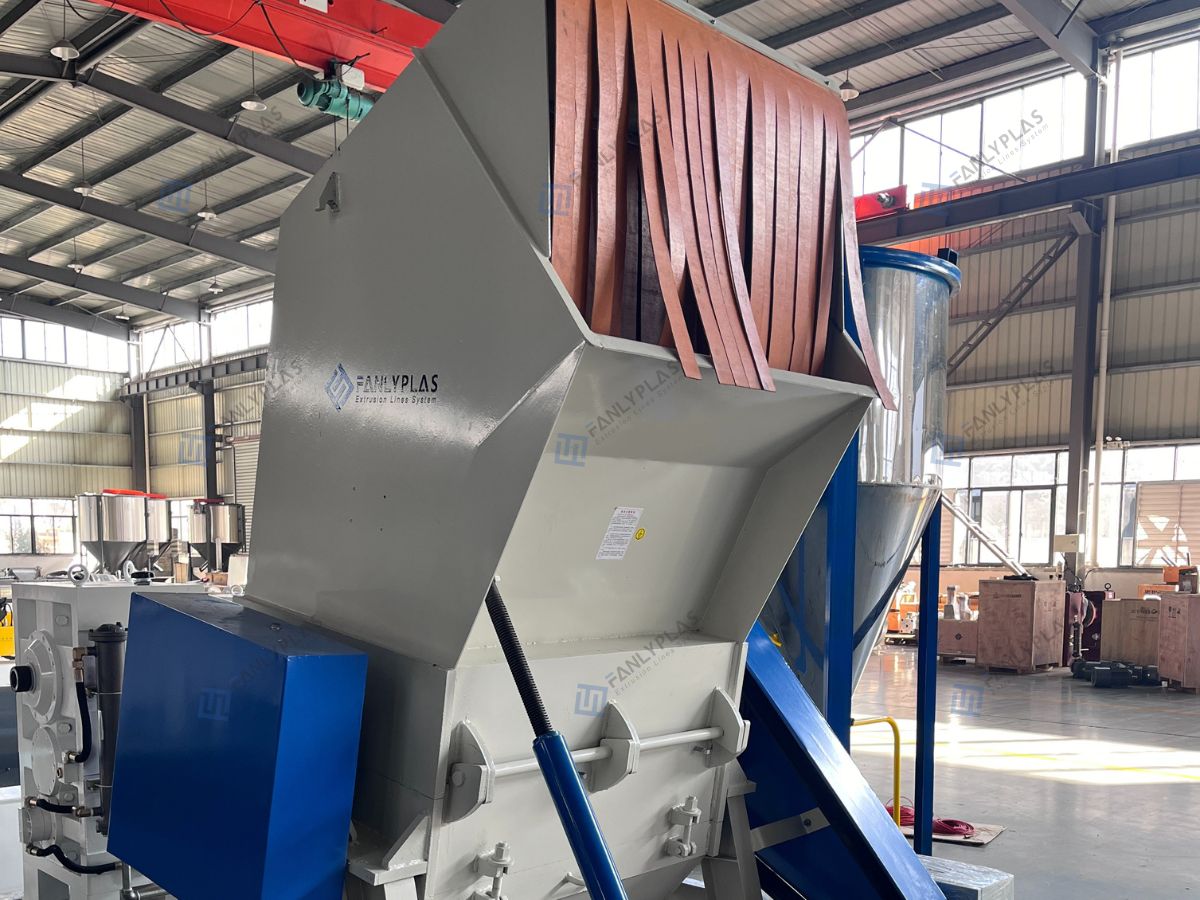
Crusher
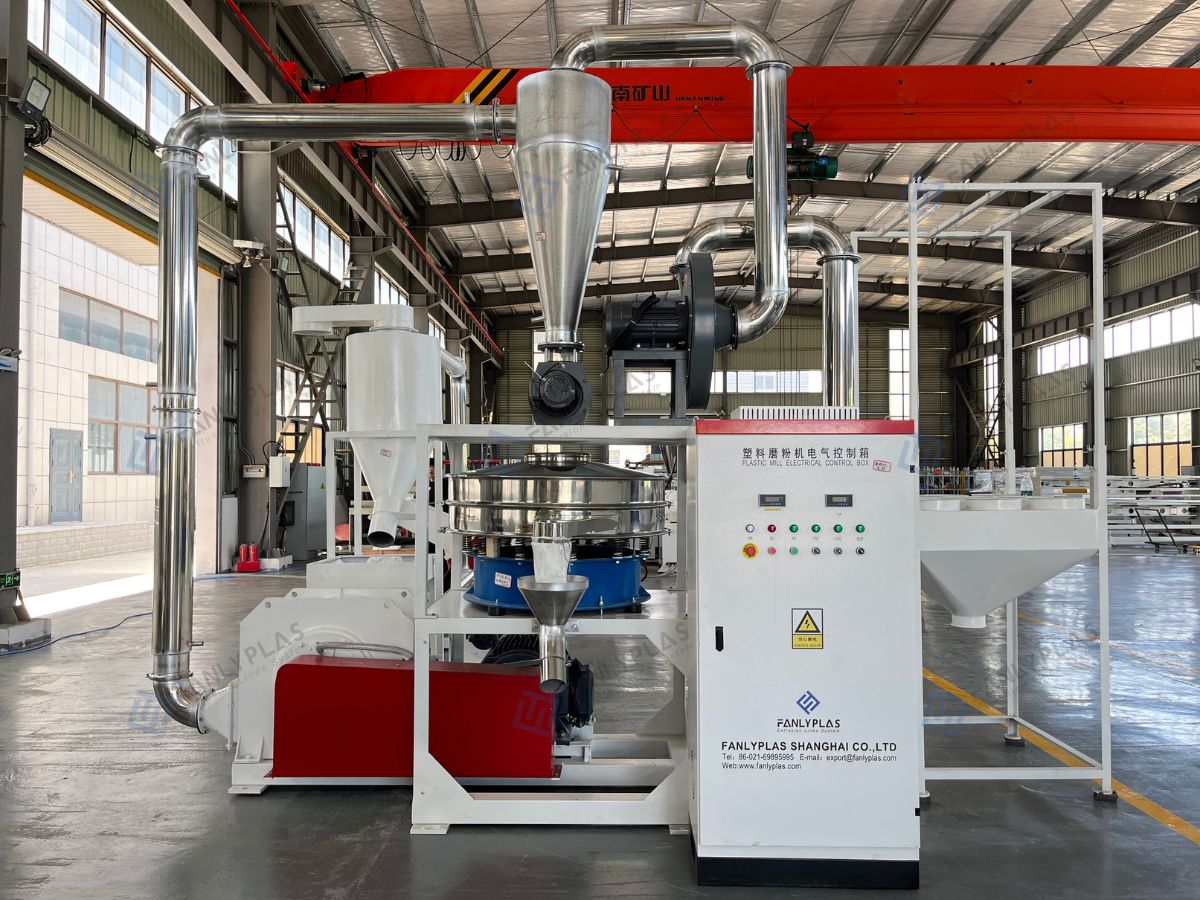
Miller
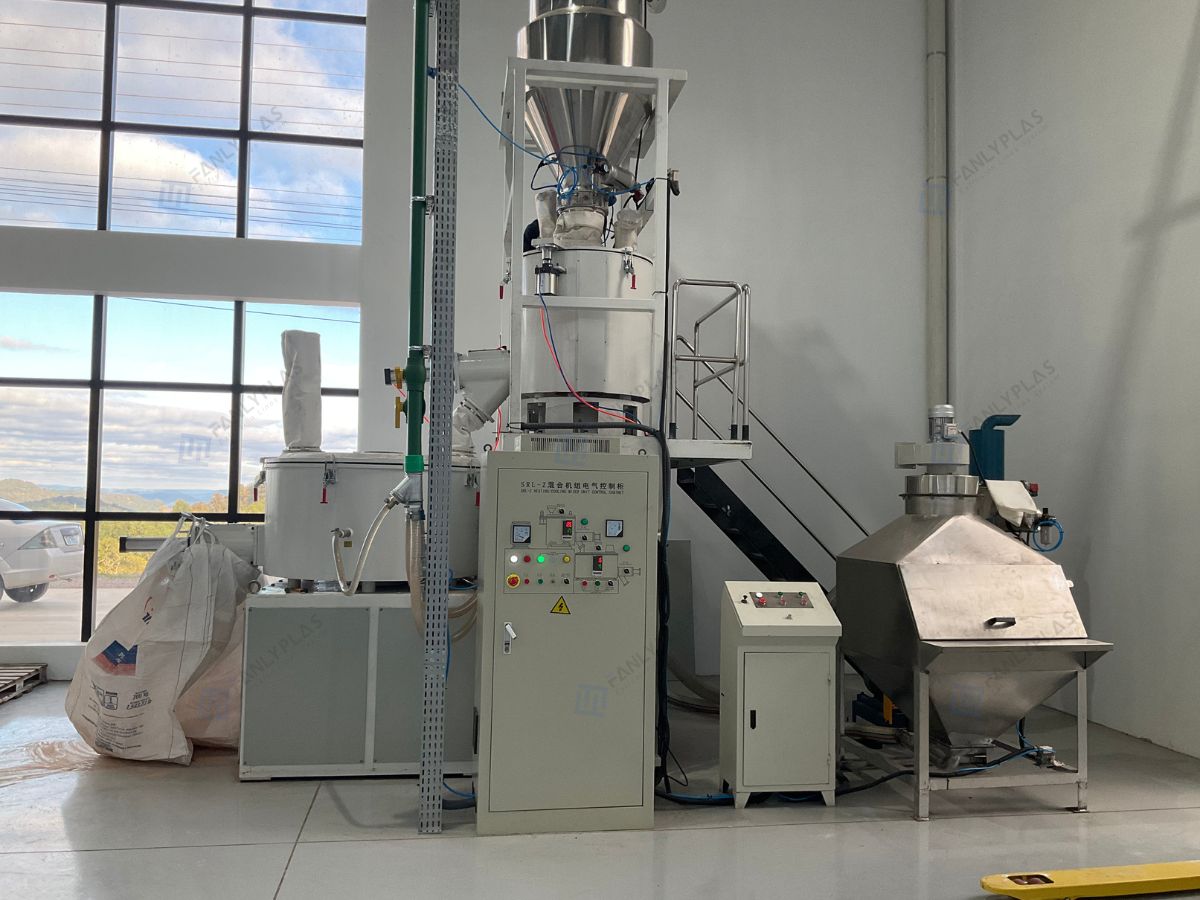
Mixing Unit
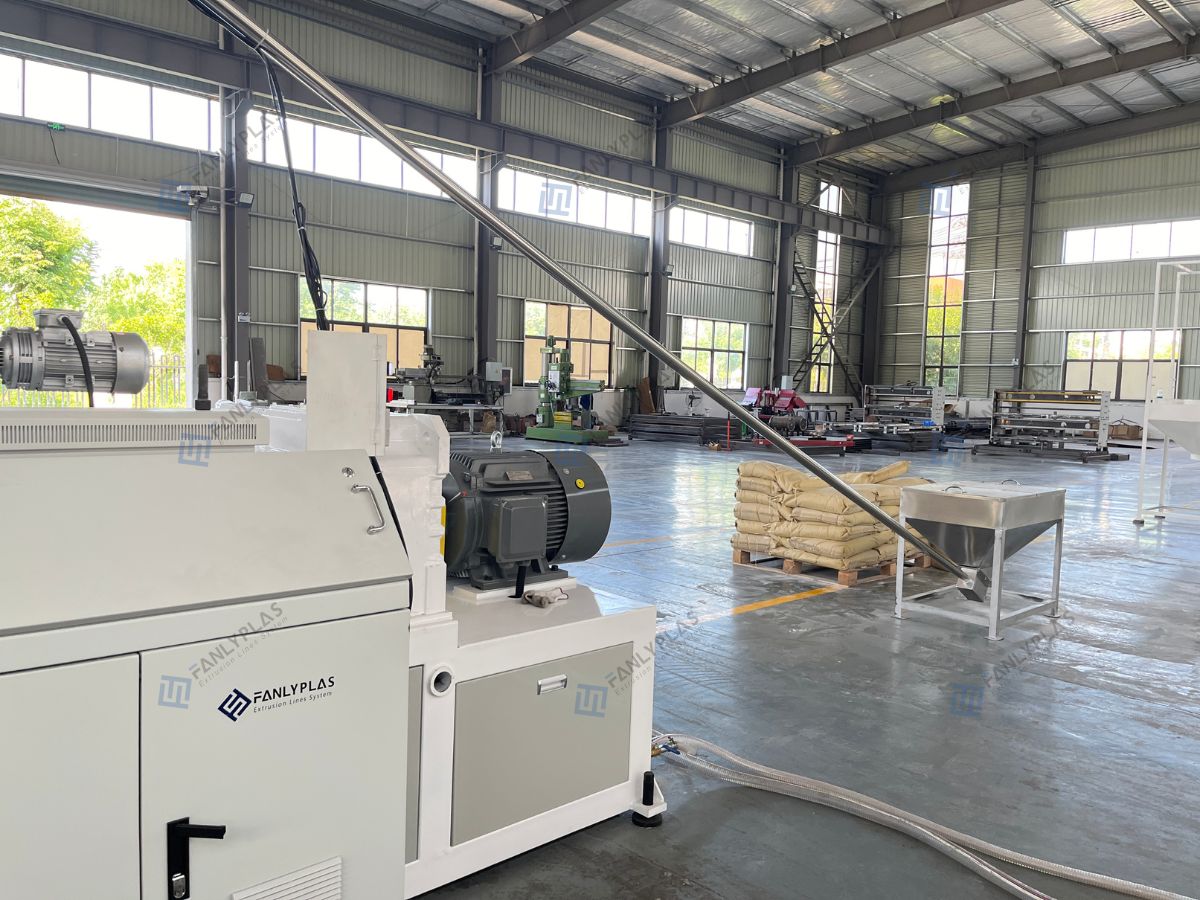
Feeding System
WPC Foam Board Production Line Workflow
1
Material Mixing
All raw materials will be prepared as per formula and loaded it into hot mixer to get evenly mixing by self-friction & electric heating, then release them to cold mixer and cooled down by water cooling.
2
Extrusion and Melting
Extrusion is the most critical part in manufacturing WPC foam board. The plastic materials in powder form will be conveyed forward by two rotation screws in opposite directions, and heated and plasticized into molten material form.
3
Shaping
The molten material from extruder will go through adapter into T-die. Molten material will be forming again inside T-die, and T-die will give it a general shape and required thickness. Then, preformed board comes out from T-die mouth.
4
Calibrating and Cooling
The preformed board is cooled by cycling cooling water calilbration table to get the required thickness and perfect surface. And a series of rollers of cooling bracket will help foam board exposed to the surrounding air for further cooling.
5
Top film Laminating and Hauling off
After cooling, a protective film is laminated onto the surface to prevent scratches during handling, and haul off unit gives enough power for foam board processing.
6
Cutting and Edge Trimming
The cooled sheet is cut to the desired length using a cutting machine. Simultaneously, excess edges are trimmed to ensure uniformity and precise dimensions.
7
Automatic stacking
The cut plates are neatly stacked on pallets using automated robots.
8
Grinding and pulverizing
Foam board scrap can be put into the grinder and cut big pieces into small pieces, then pulverized them into powder. Those powder can be reused in foam board formula as recycled material.
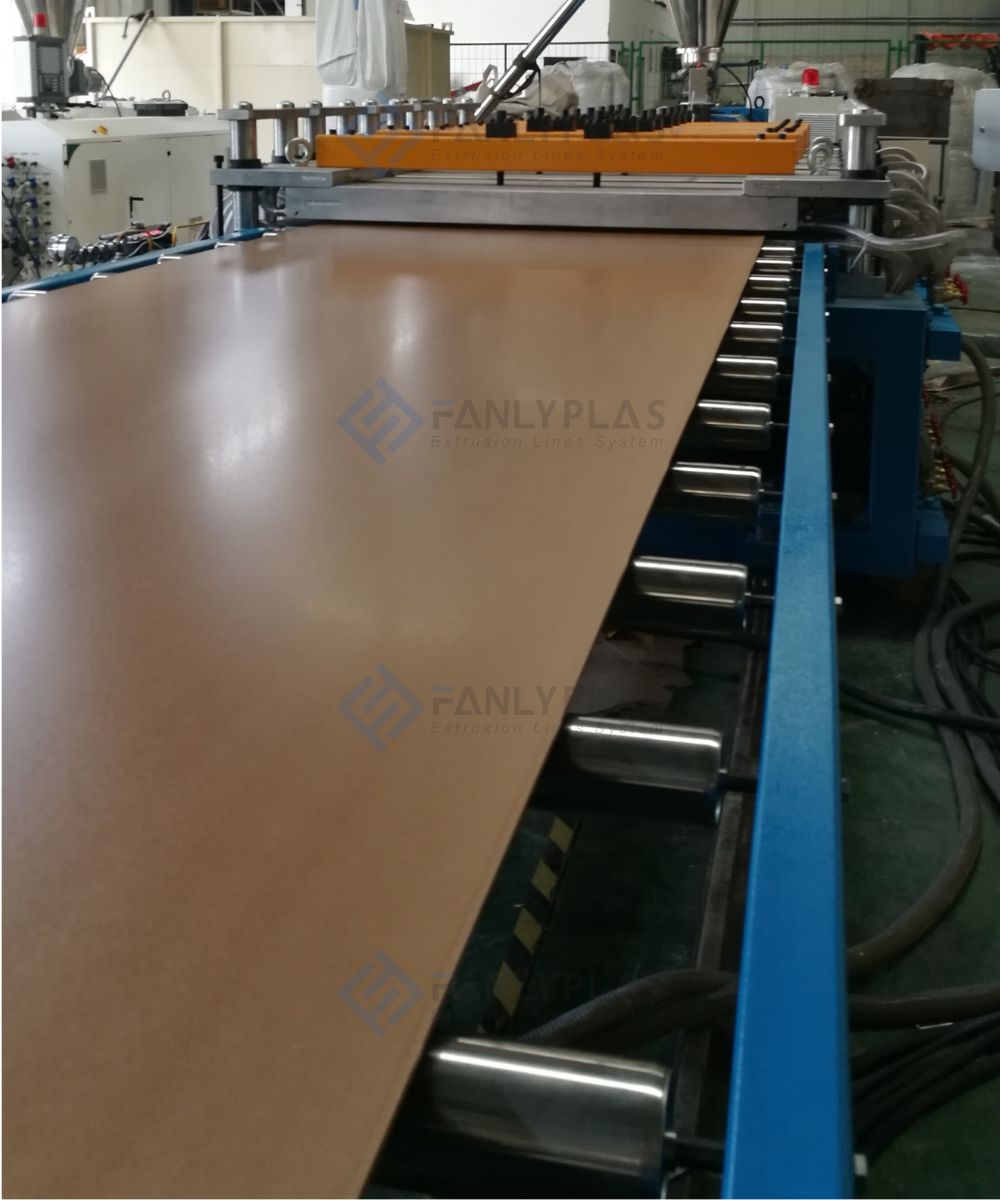
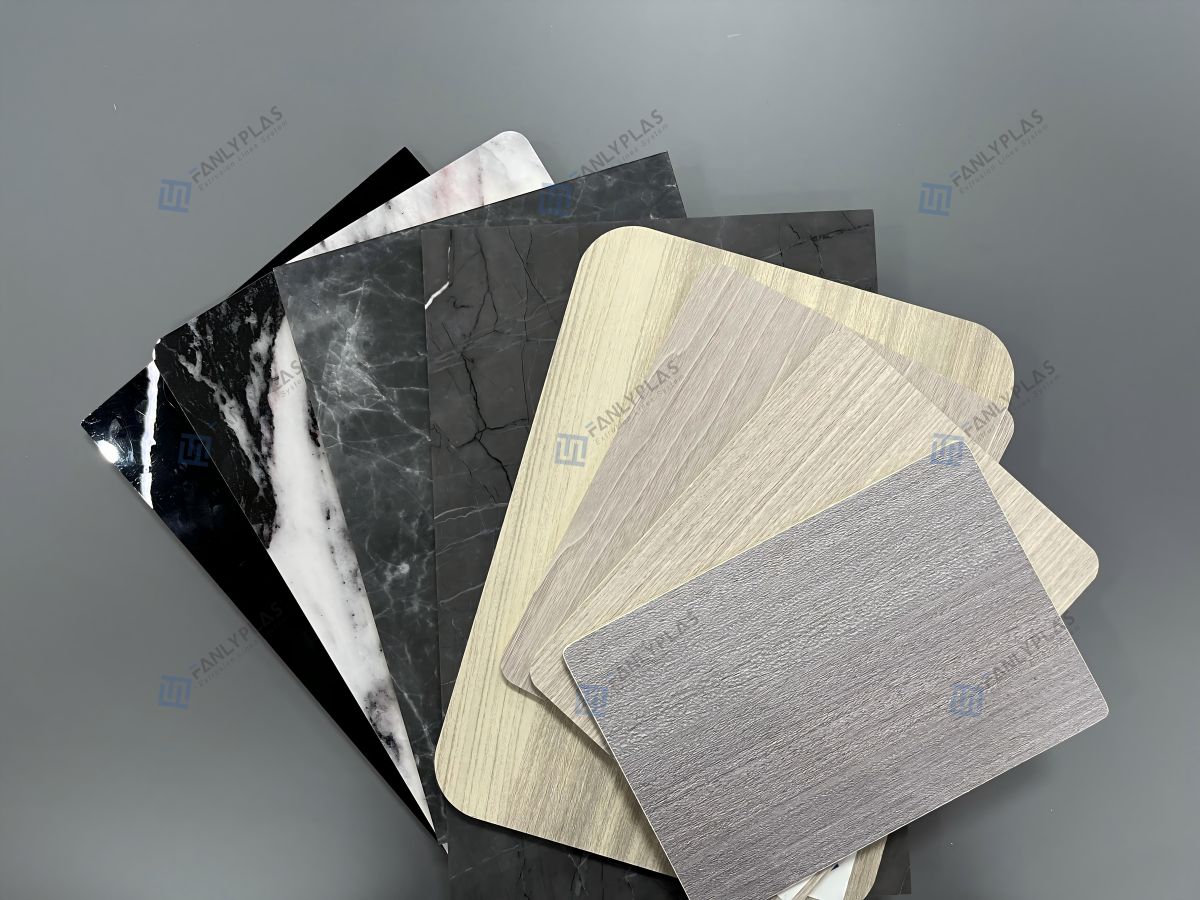
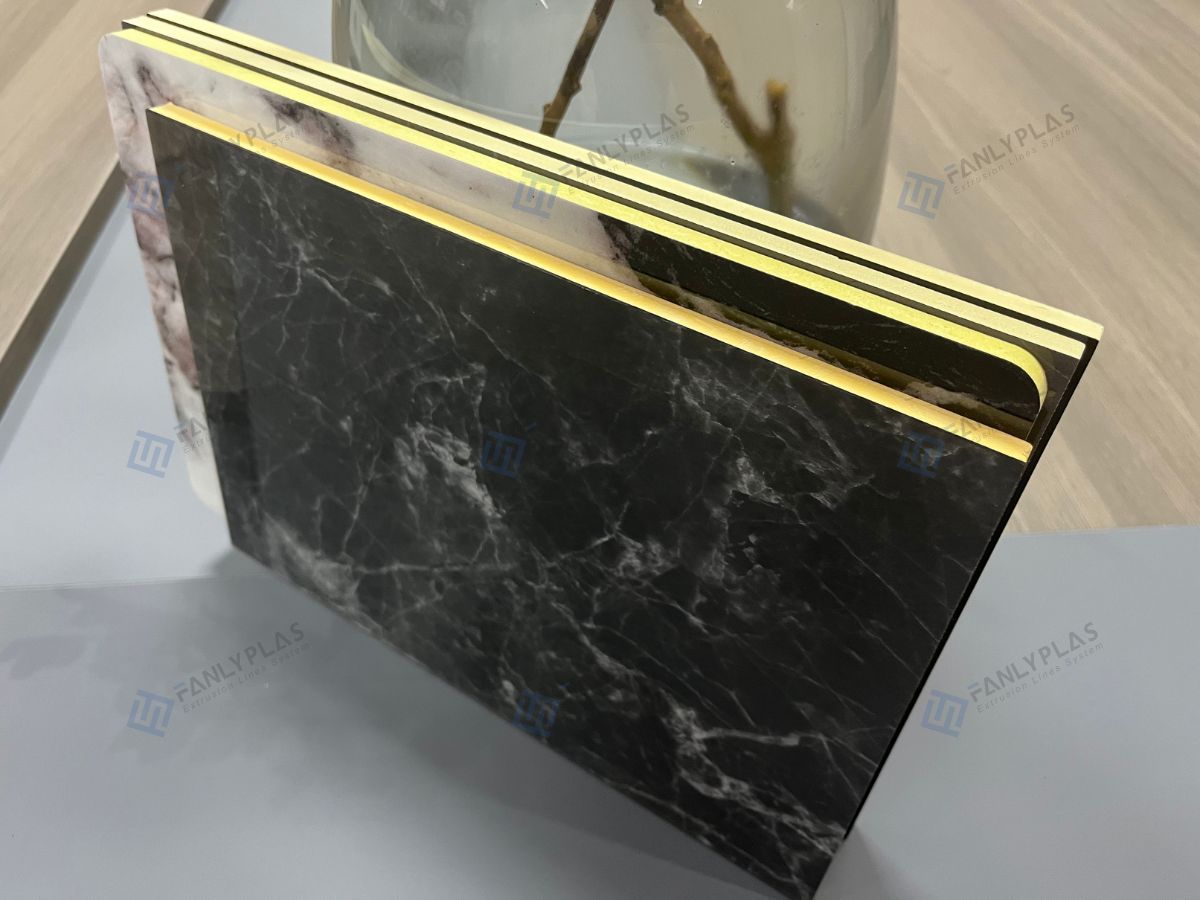
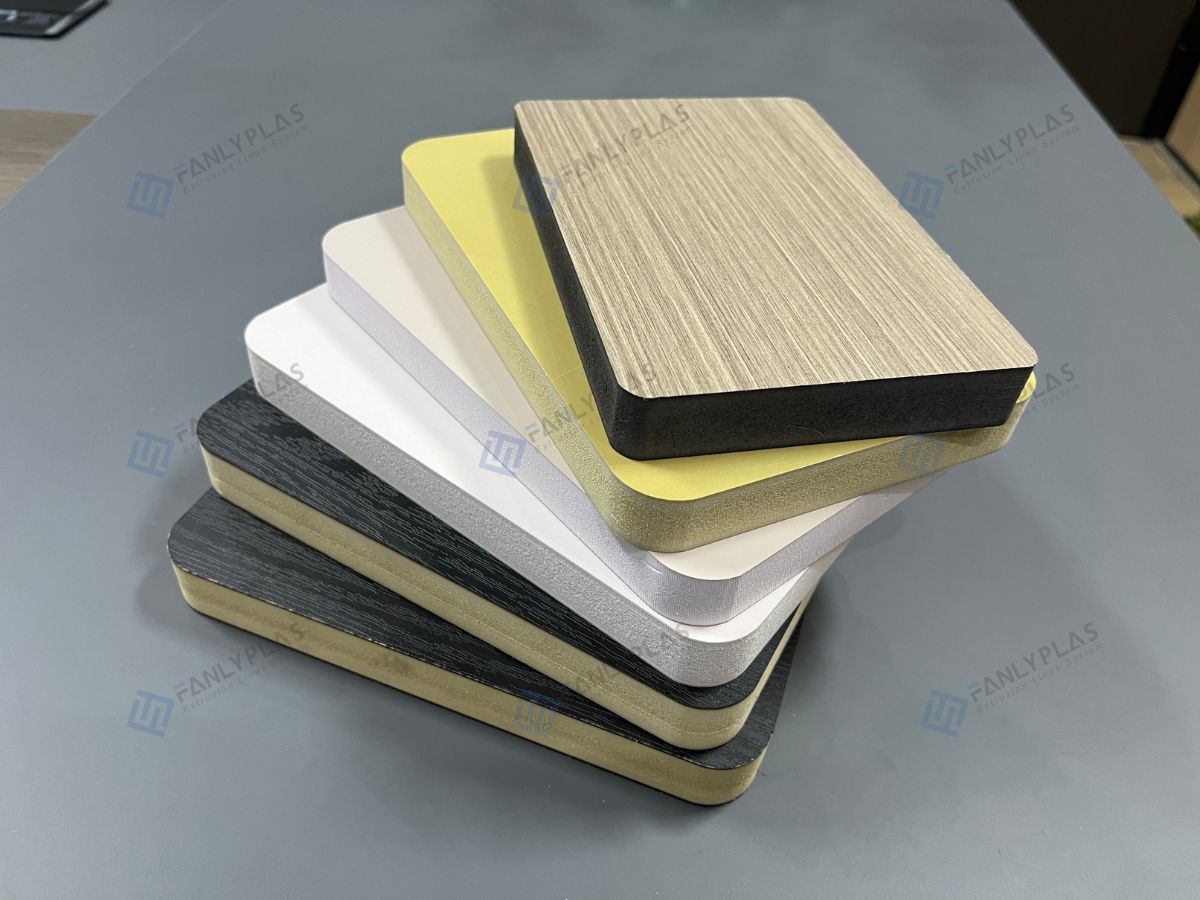
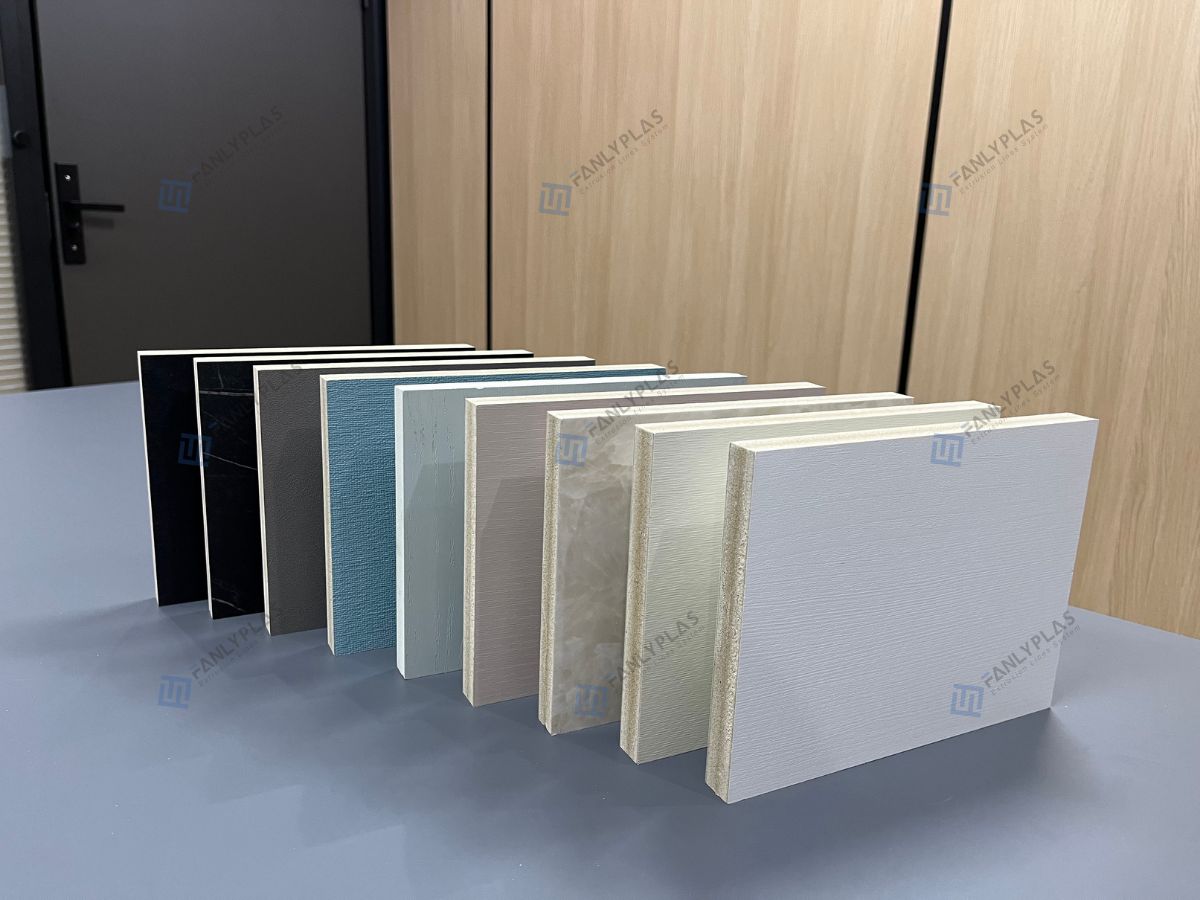
Characteristics and Applications of WPC Foam Board
Features of WPC Foam Boards :
WPC foam boards are lightweight yet durable and moisture-resistant, ideal for various applications. They are termite-proof, require low maintenance, and offer good thermal and sound insulation. Easy to work with, they provide a smooth surface for printing and lamination.
Applications of WPC Foam Boards :
WPC foam boards are widely used for interior wall panels, ceilings, furniture, and advertising signage. Their moisture resistance makes them suitable for kitchens and bathrooms. They are also used in door frames, decorative moldings, and packaging.
Q&A
What is the production capacity of WPC Foam board production line?
Can the production line produce sheets of different sizes and thicknesses?
What is the lead time for ordering your WPC Foam board production line?
How long does it take to install and commission the production line?
Installation and commissioning typically take 10-15 days, depending on the complexity of the production line. Our engineers provide on-site support and training during this period.
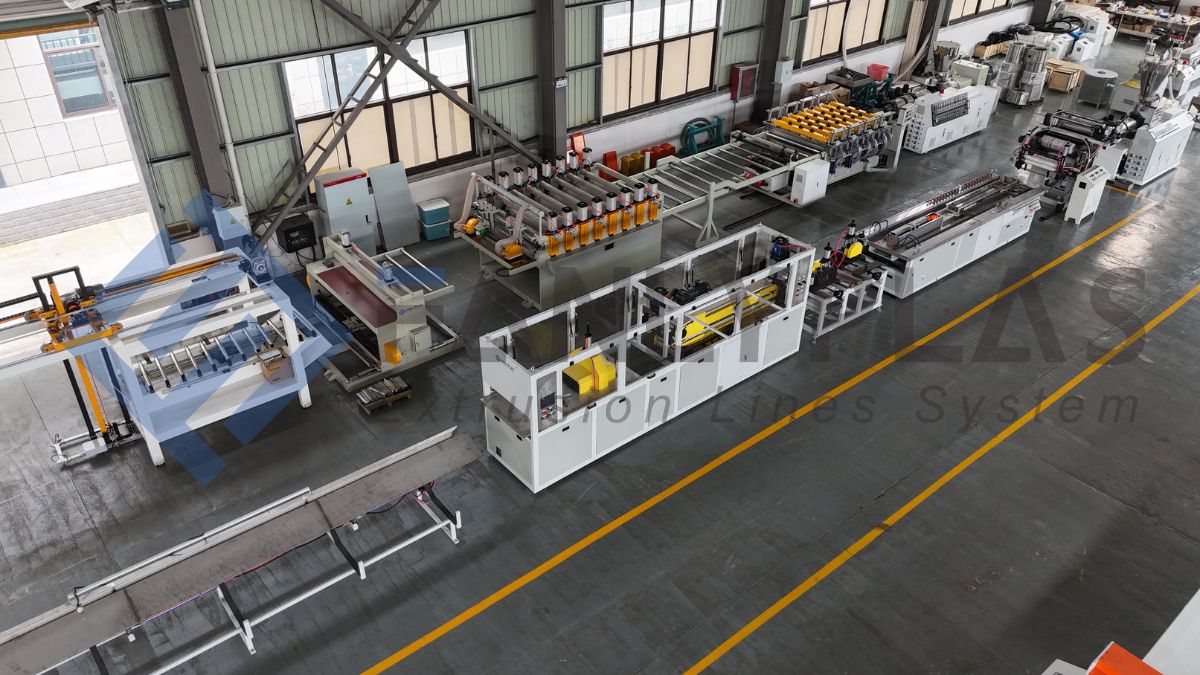
Why Choose Production Line from FANLYPLAS?
1
Superior Quality & Advanced Technology
ANLYPLAS is committed to providing high-quality WPC foam board production line, utilizing advanced extrusion technology and precise mold design to ensure stable and efficient operation, producing excellent WPC foam board to help you stand out in the market.
2
Customized Solutions & Professional Service
We have an experienced team that can provide tailor-made production line solutions based on your specific needs. Additionally, we offer comprehensive installation, training, and after-sales service to ensure the smooth operation of your production without any worries.
3
Continuous Innovation & Trustworthy Brand
FANLYPLAS, a well-known mechanical equipment production line brand from Shanghai, continuously invests in R&D to constantly optimize products and technologies. Choose us, and you will get reliable products and a long-term partnership.
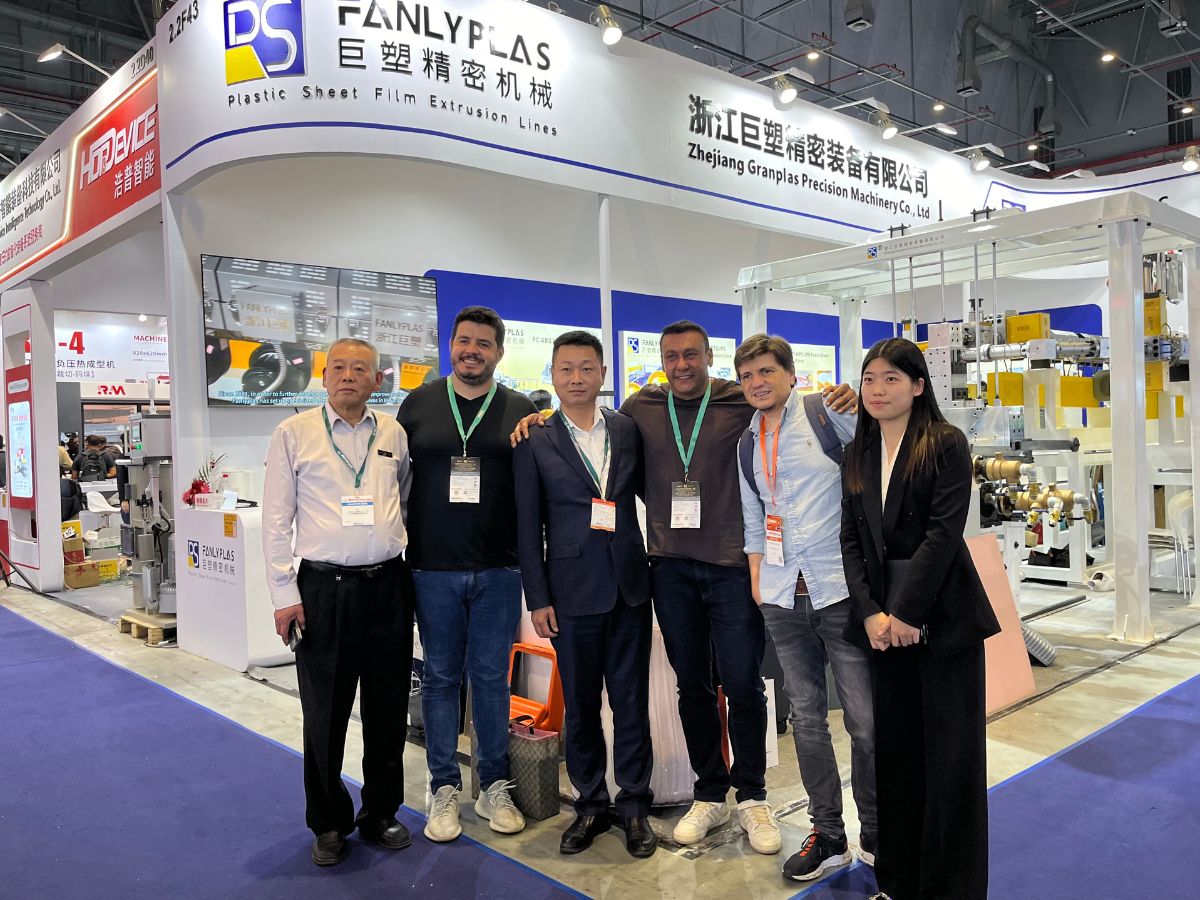
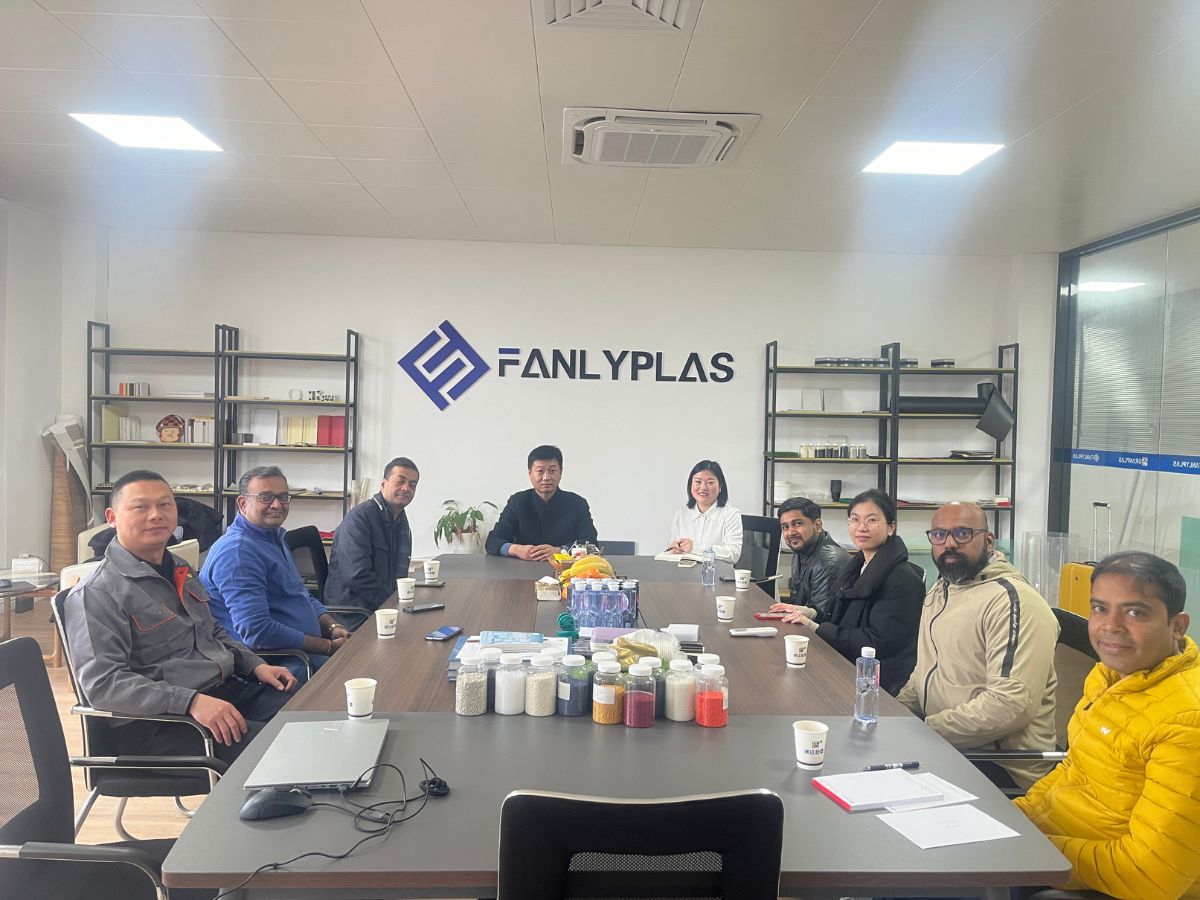
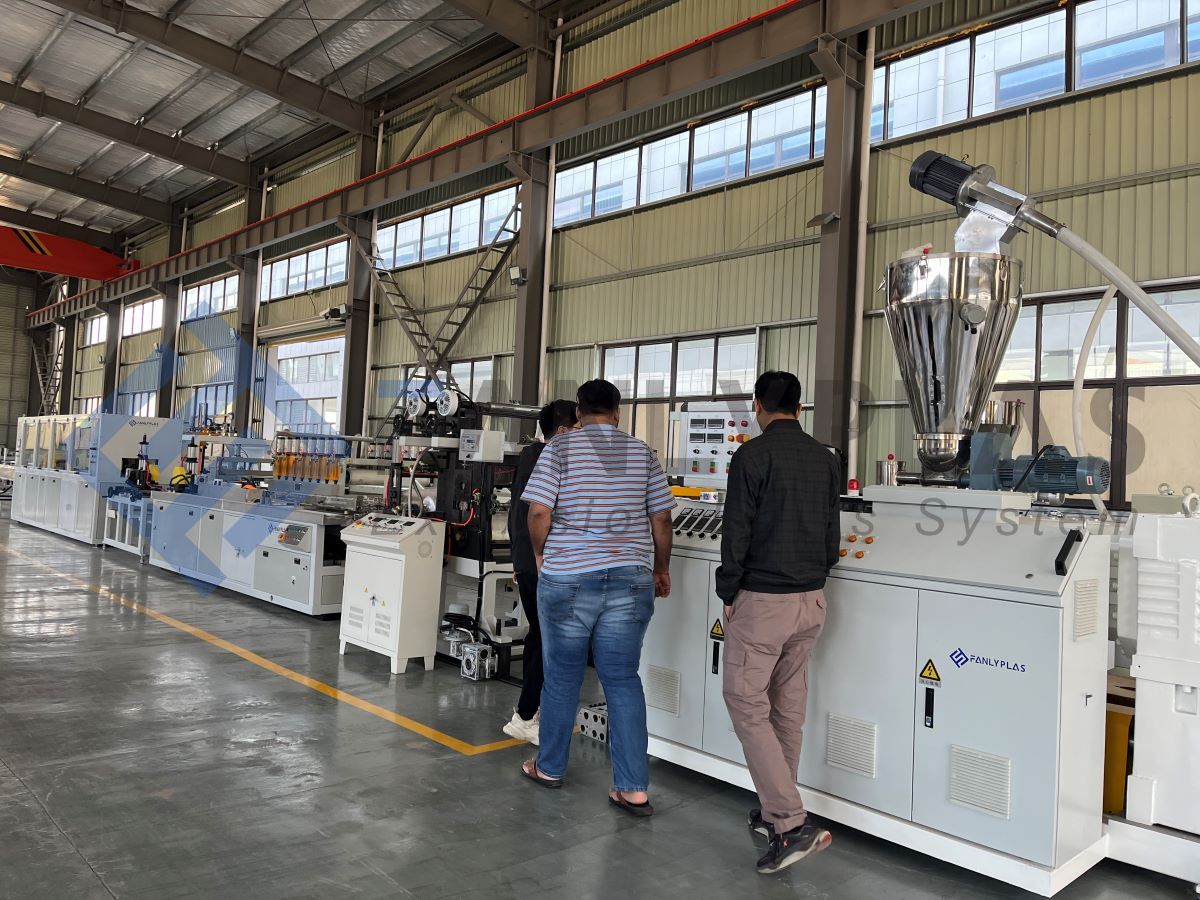


Contact Us for Your Solution!
Thank you for your interest in FANLYPLAS WPC foam board production lines! If you have any questions or requirements regarding our products, or if you would like to obtain a more detailed customized solution, please fill out the contact form below with your contact information and specific needs. Our professional team will contact you as soon as possible to provide you with the best quality service and support.