PMMA Acrylic Sheet Production Line
Be Green By Extrusion!
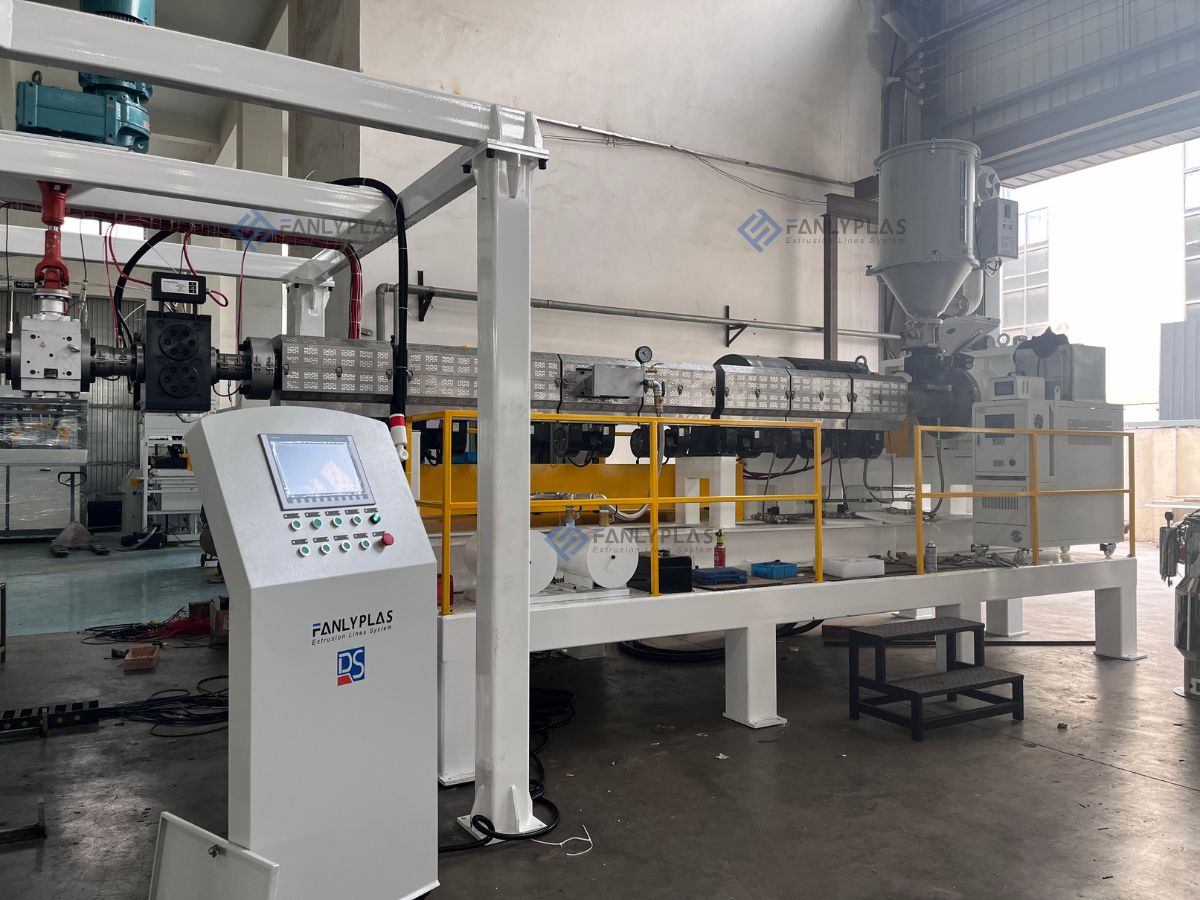
Applications and Features of FANLYPLAS PMMA Acrylic Sheet Production Line
FANLYPLAS Acrylic Sheet Production Line is a high-performance manufacturing system designed for the production of acrylic sheets with exceptional purity, gloosy and no crystal point.
Key Features of the Production Line:
1.Advanced Extrusion Technology: Our Acrylic Sheet Production Line employs state-of-the-art extrusion equipment to ensure uniform thickness, smooth surfaces, and no bubbles.
2.High Efficiency and Automation:The production line integrates automation systems, including precise temperature control and synchronized operations, enhancing productivity and reducing labor costs.
3.Customizable Design:Our production line supports various sheet specifications, including thickness, width, and surface textures, to meet diverse application needs.
4. Precise cutting system: We adopts knife cutting and braking system together to reach perfect edge trimming and cross cutting. Non-dust cutting system which makes workshop more clean and energy saving.
5.Easy Operation and Maintenance:The user-friendly interface and robust construction ensure ease of operation and maintenance, reducing downtime and operational costs.
Equipment Composition of FANLYPLAS PMMA Acrylic Sheet Production Line
FANLYPLAS offers customized PMMA Acrylic Sheet Production Line based on customer requirements, including product specifications, production volume, facility size, and desired level of automation. We provide flexible configurations to meet various needs. Below are some of the standard configurations available for FANLYPLAS PMMA Acrylic Sheet Production Line.
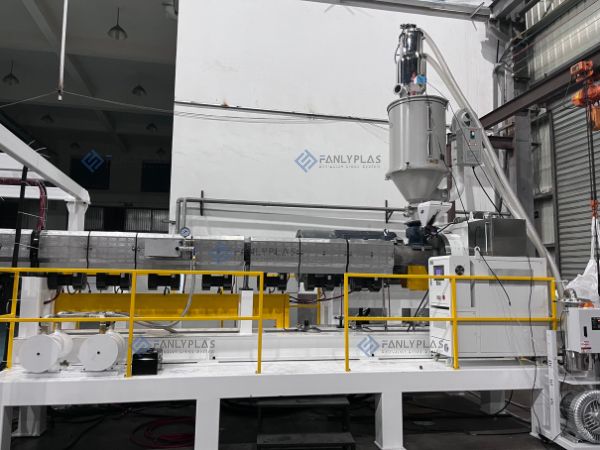
Extruder
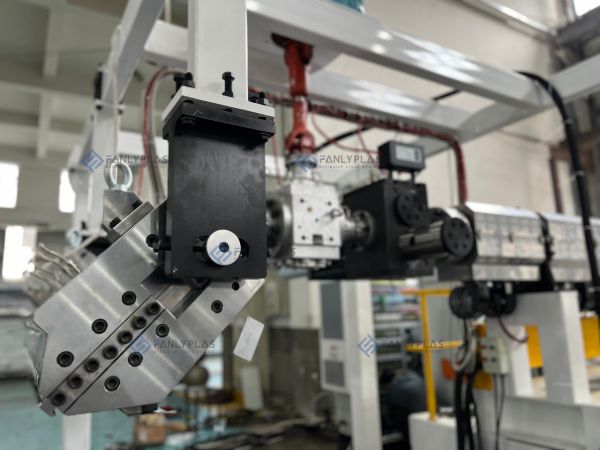
Die Head
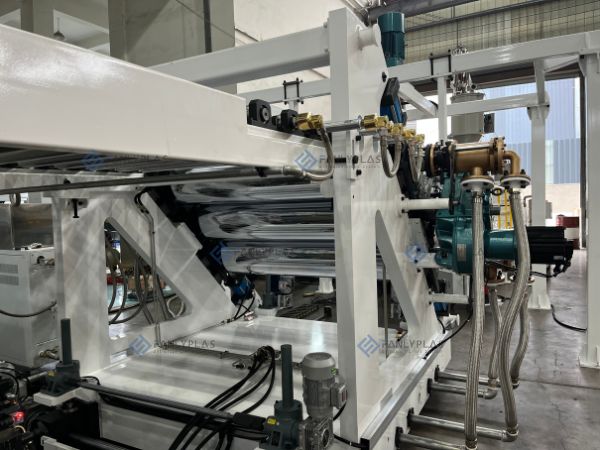
Three-roll Calender
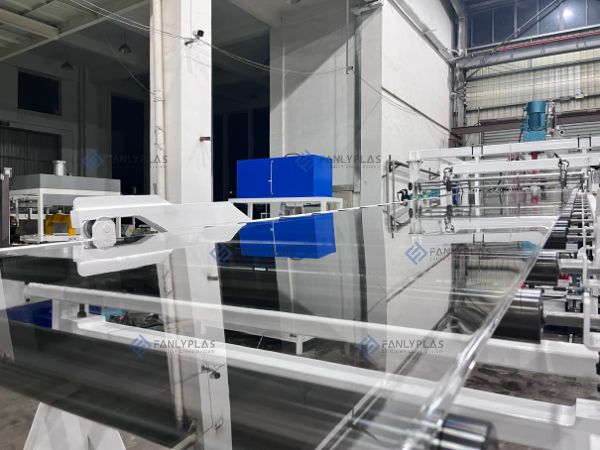
Cooling Roller Bracket
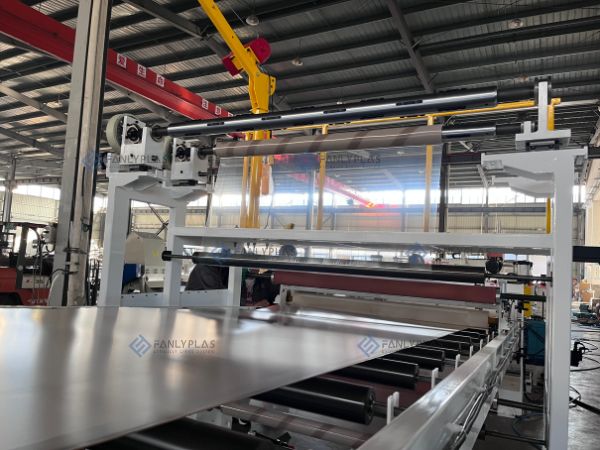
Haul-Off Unit
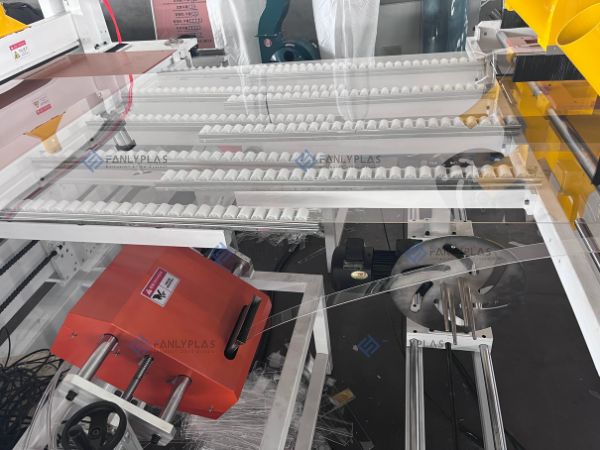
Edge Punching Collection Unit
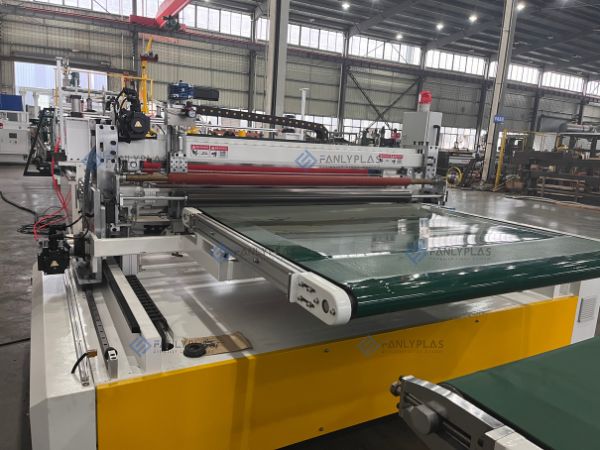
Knife Cutting Machine
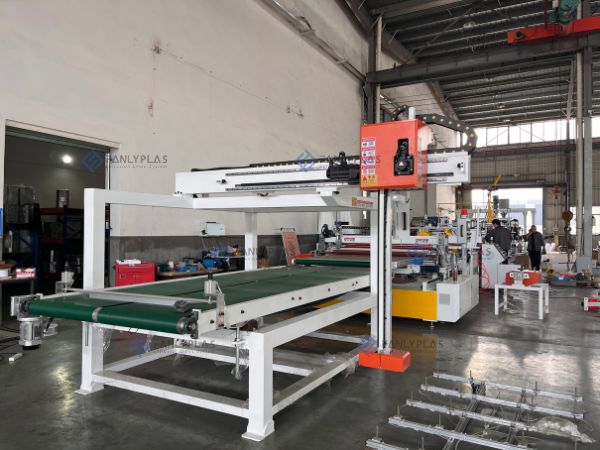
Auto Stacking System
FANLYPLAS PMMA Acrylic Sheet Production Line Workflow
1.Material Feeding
2.Extrusion and Melting
3.Shaping and Surface Finishing
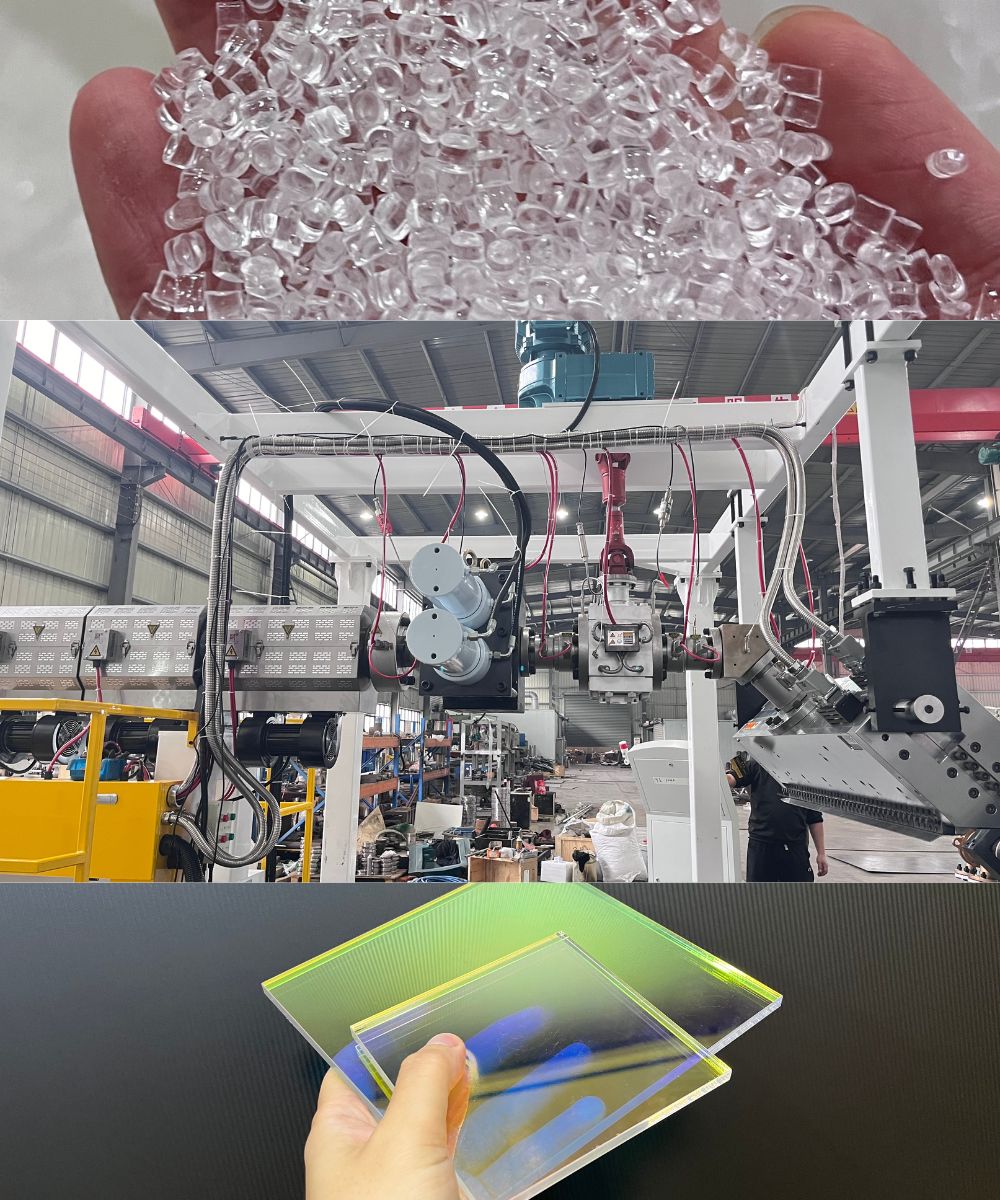
4.Cooling and Laminating (Film Coating)
5.Cutting and Edge Trimming
6.Automatic stacking
Characteristics and Applications of Acrylic Sheets
Acrylic sheets are known for their exceptional optical transparency, with a light transmittance of up to 92%, making them a superior alternative to glass. They are lightweight, impact-resistant, and weather-resistant, offering excellent durability in outdoor conditions. Acrylic is easy to machine, cut, and thermoform, making it versatile for various applications. Additionally, it is chemically stable and UV-resistant, ensuring long-lasting clarity and strength.
1.Construction and Architecture:Acrylic sheets are used as windows, skylights, partitions, and signage panels due to their high transparency, durability, and lightweight properties.
2.Advertising and Displays:They are ideal for illuminated signs, exhibition displays, and retail showcases, offering superior clarity and ease of customization.
3.Automotive Industry:Acrylic sheets are used for car light covers, dashboards, and interior design, providing lightweight and weather-resistant solutions.
4.Medical Equipment:Non-toxic and transparent, acrylic sheets are used in protective barriers, incubators, and medical device housings.
5. High-end furniture laminated surface: By doing anti-scratch coating, then laminate with PVC printed film to get high glossy acrylic laminate sheet which used for high-end furniture surface is getting very popular now.
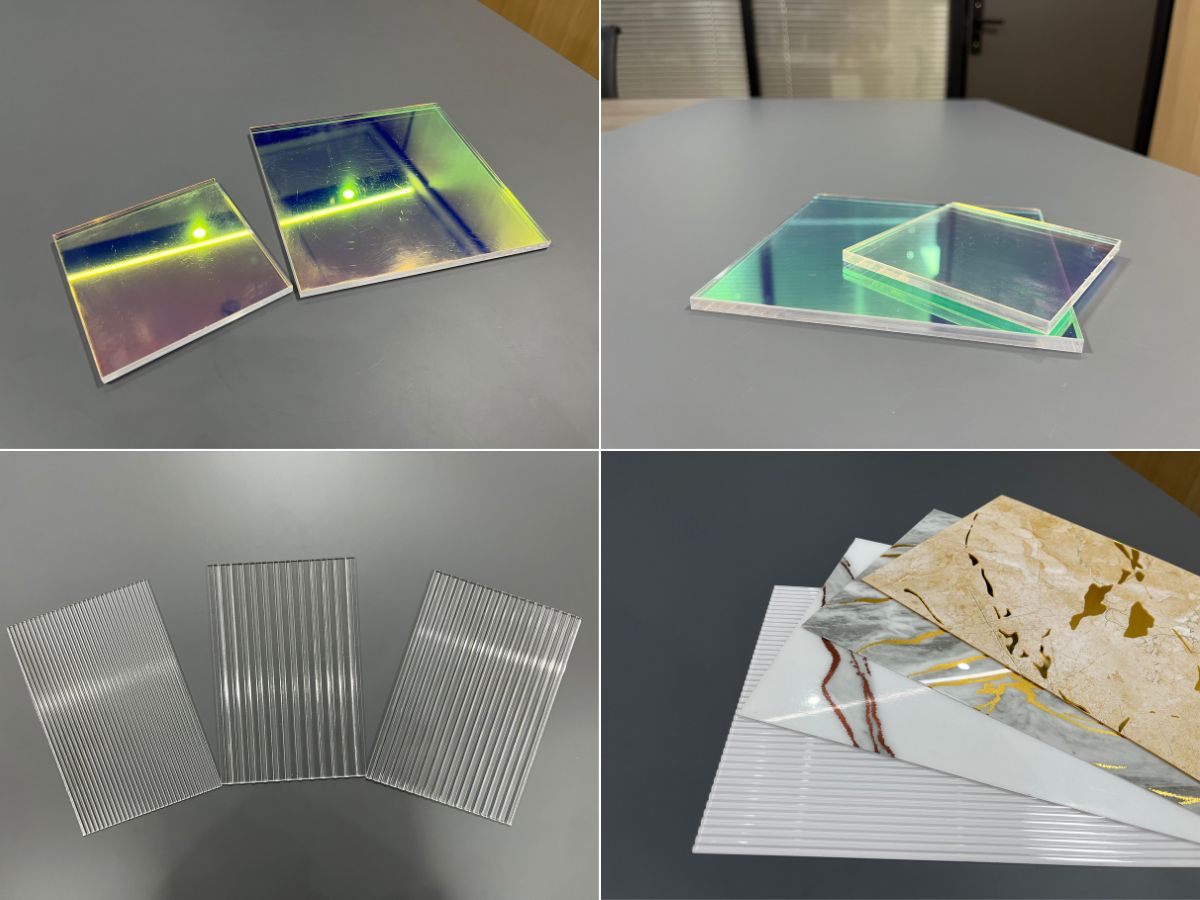
Q&A
What is the production capacity of the acrylic sheet production line?
The production capacity depends on the model and configuration of the production line. Typically, it ranges from 300 to 800 kg per hour. We can customize the capacity based on your specific requirements and variable as per different thickness and width.
Can the production line produce sheets of different sizes and thicknesses?
Yes, the production line is designed to produce sheets with various thicknesses (from 0.8-2mm) and width between 1220-2100mm. We provide different extruder model, adjustable die heads and suitable downstreams ,calender rollers to meet your specifications.
What raw materials are required for the production line?
The primary raw material is PMMA (acrylic pellets). Additives such as UV stabilizers, Masterbatch can also be used, depending on the desired sheet properties and colors.
How long does it take to install and commission the production line?
Installation and commissioning typically take 10-15 days, depending on the complexity of the production line. Our engineers provide on-site support and training during this period.
What after-sales services do you offer?
We offer comprehensive after-sales services, including equipment maintenance, spare parts supply, remote troubleshooting, and on-site technical support. Additionally, we provide operator training to ensure smooth production.
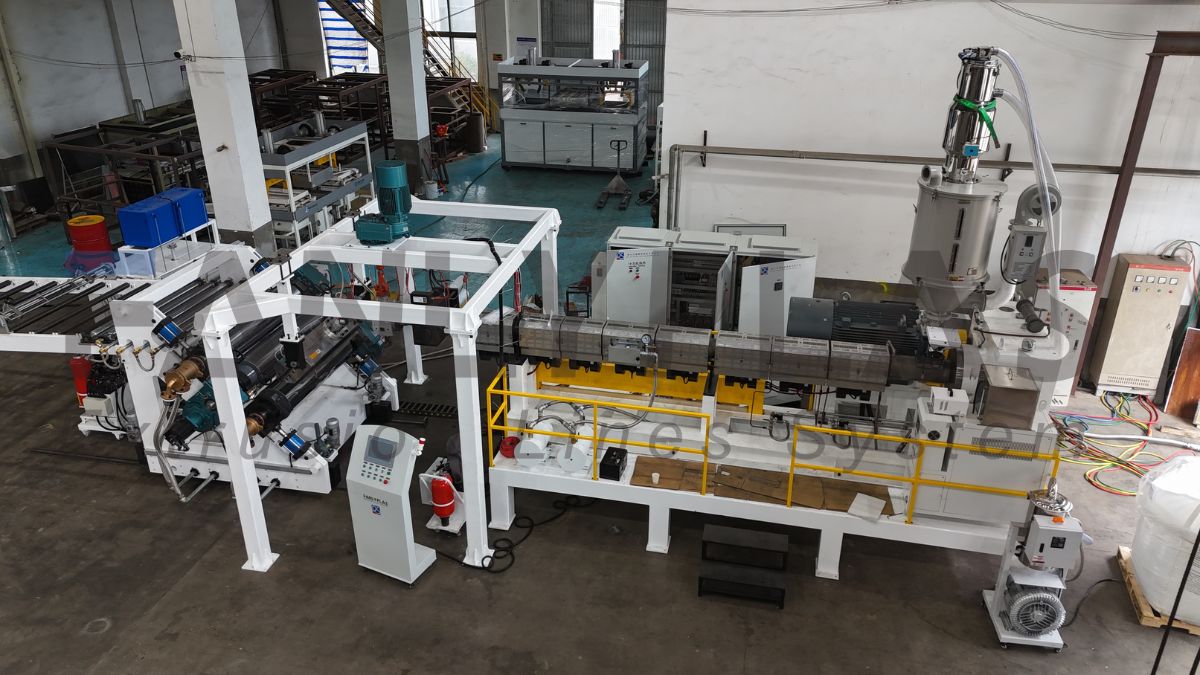
Why Choose Production Line from FANLYPLAS?
1
Superior Quality & Advanced Technology
ANLYPLAS is committed to providing high-quality PMMA acrylic sheet production lines, utilizing advanced extrusion technology and precise mold design to ensure stable and efficient operation, producing excellent acrylic sheet to help you stand out in the market.
2
Customized Solutions & Professional Service
We have an experienced team that can provide tailor-made production line solutions based on your specific needs. Additionally, we offer comprehensive installation, training, and after-sales service to ensure the smooth operation of your production without any worries.
3
Continuous Innovation & Trustworthy Brand
FANLYPLAS, a well-known mechanical equipment production line brand from Shanghai, continuously invests in R&D to constantly optimize products and technologies. Choose us, and you will get reliable products and a long-term partnership.
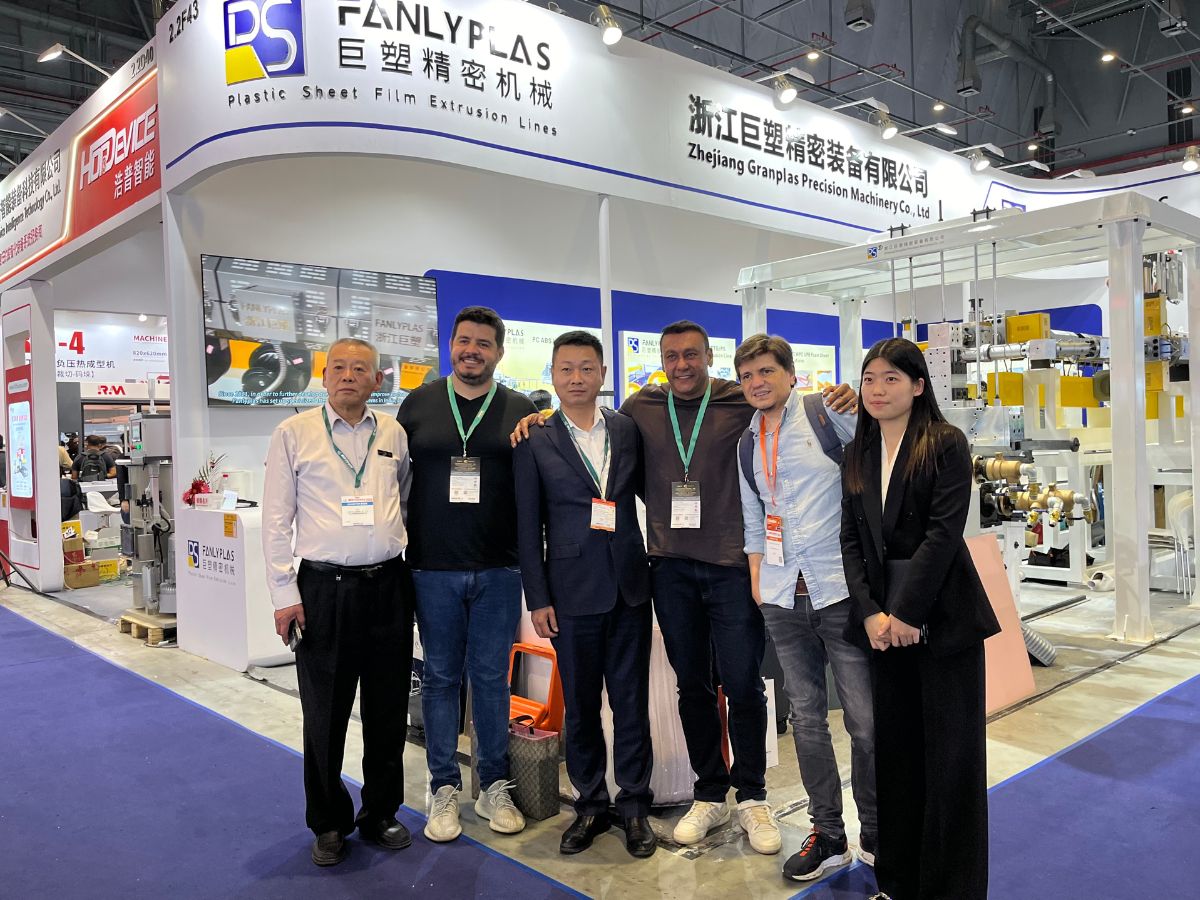
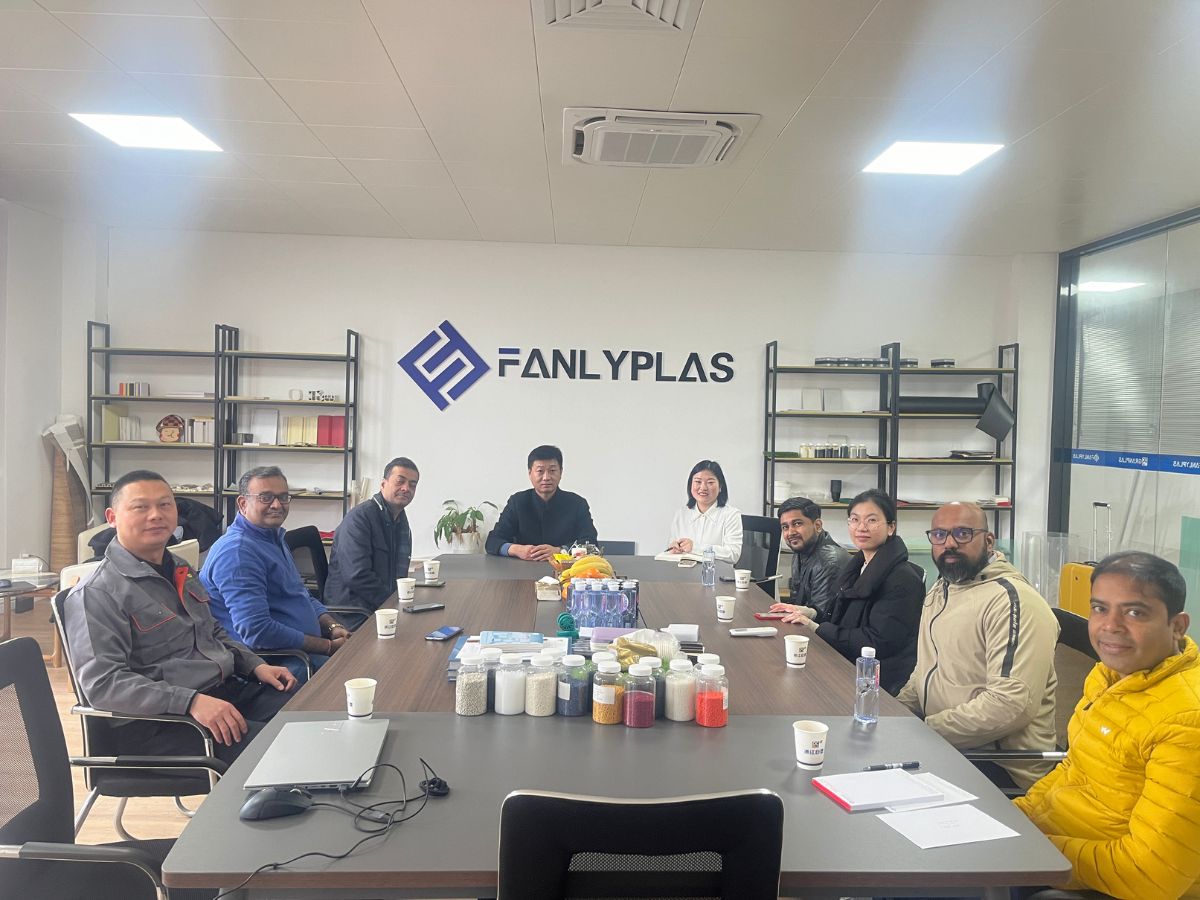
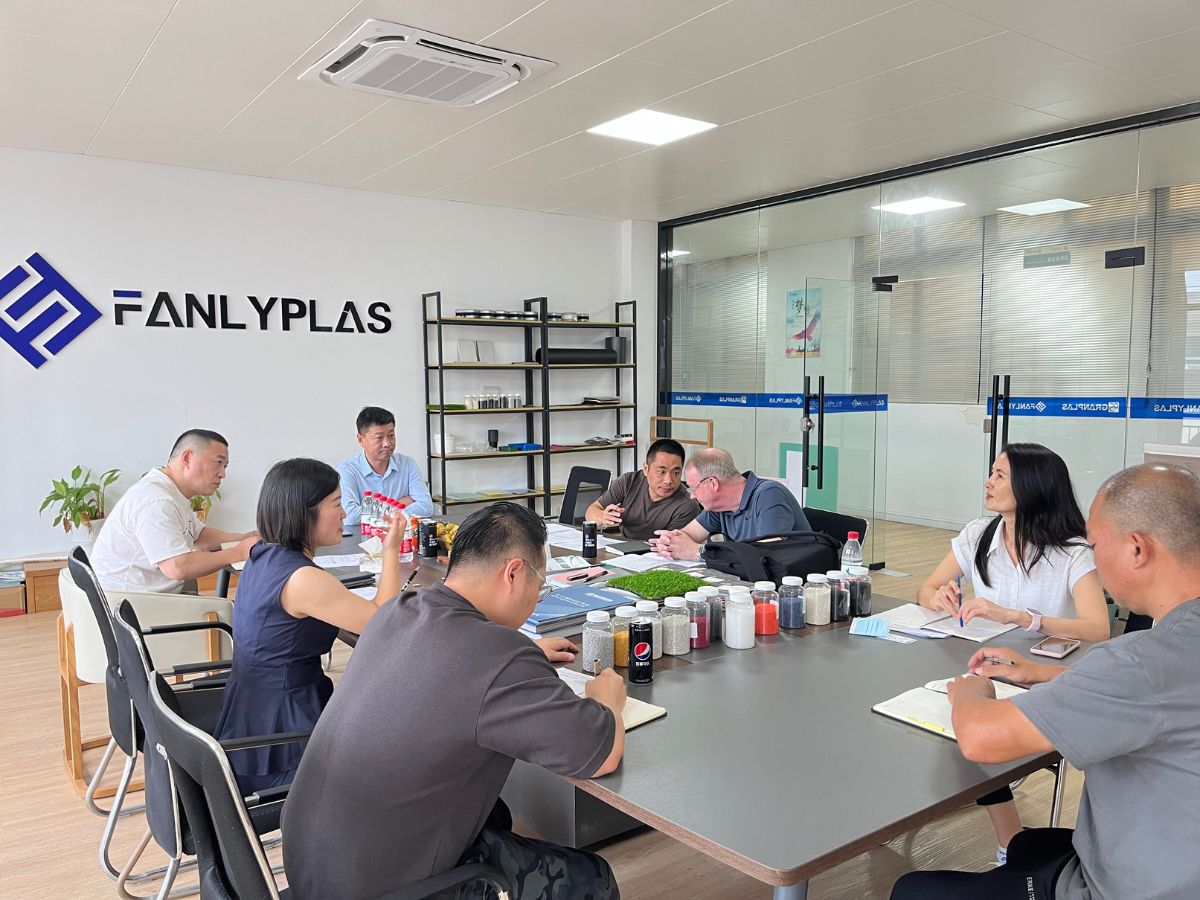
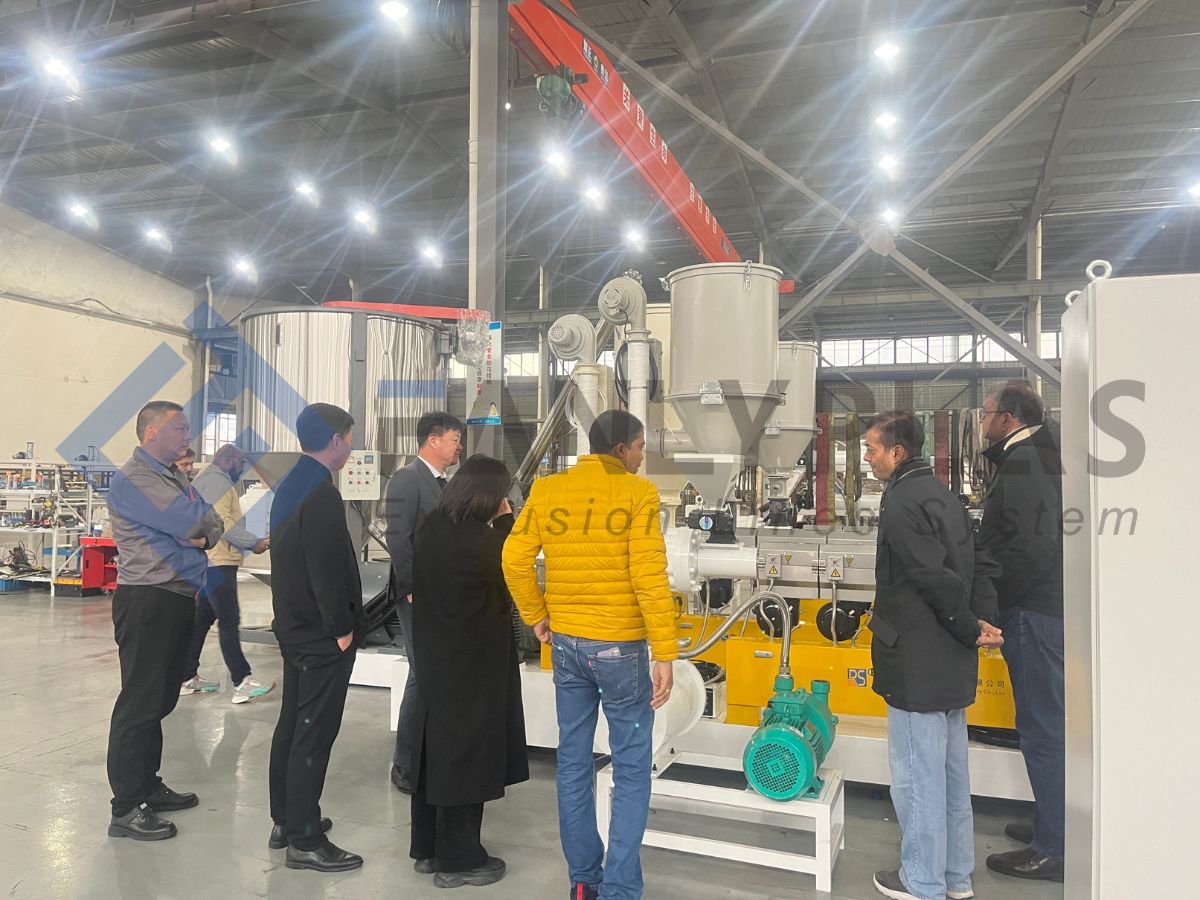
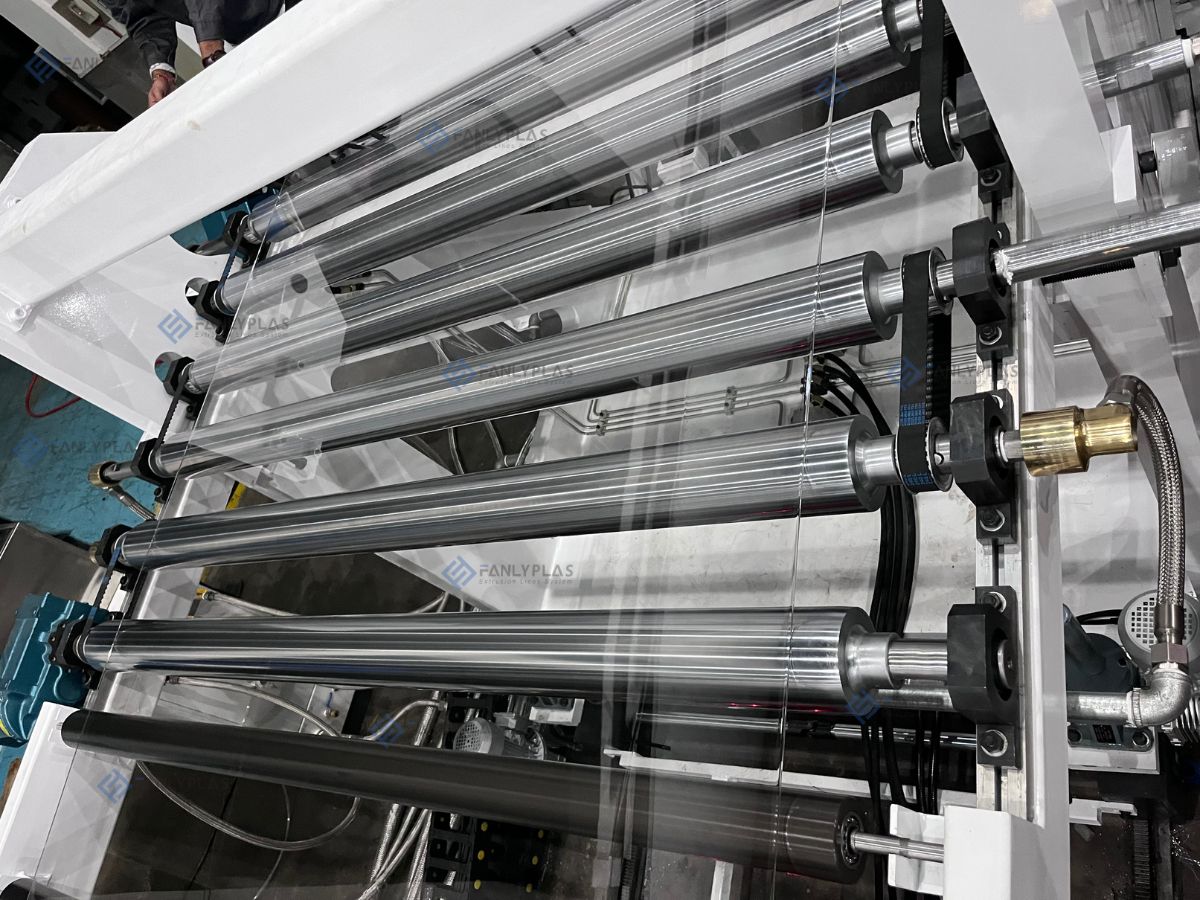
Contact Us for Your Solution!
Thank you for your interest in FANLYPLAS PMMA acrylic sheet production lines! If you have any questions or requirements regarding our products, or if you would like to obtain a more detailed customized solution, please fill out the contact form below with your contact information and specific needs. Our professional team will contact you as soon as possible to provide you with the best quality service and support.