SPC Flooring Production Line
Be Green By Extrusion!
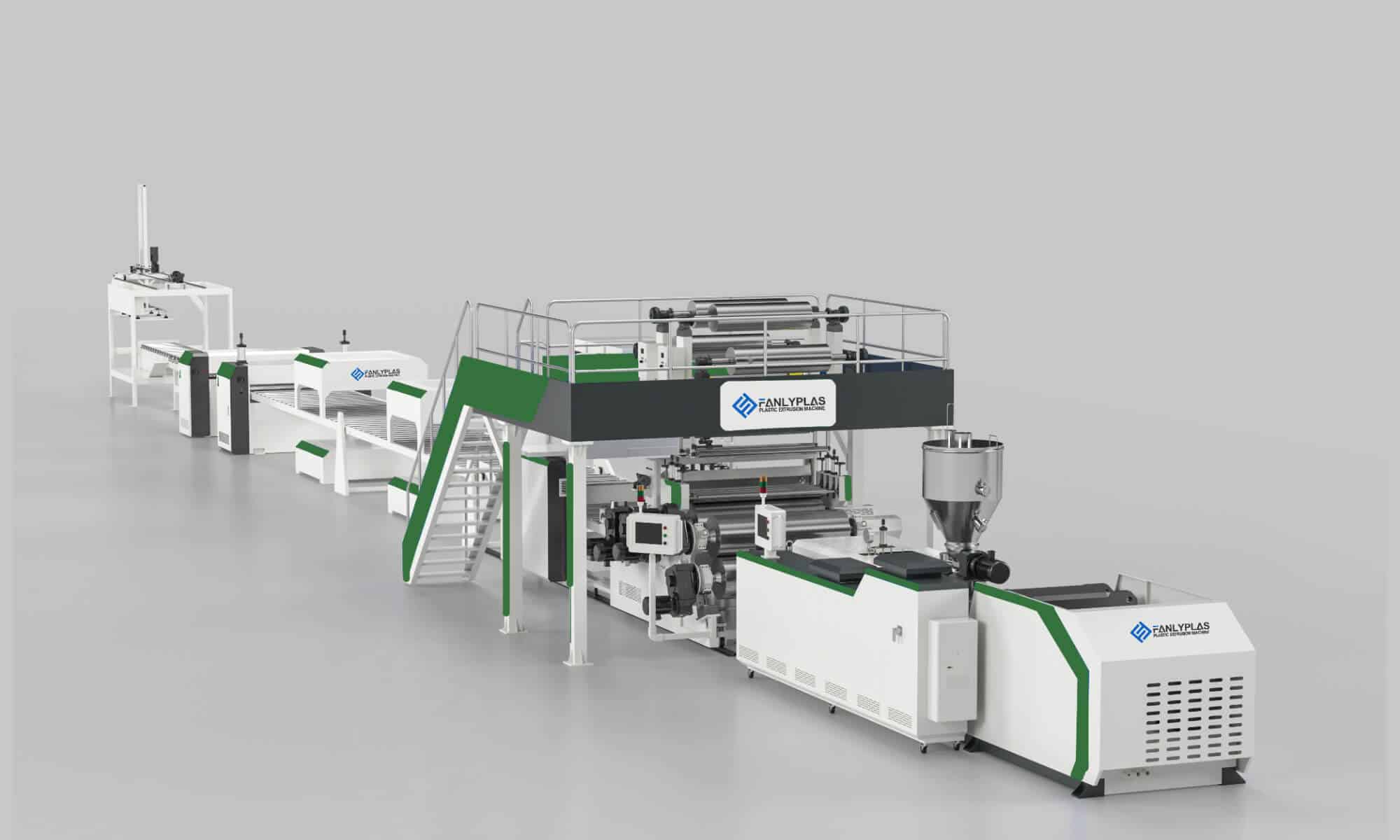
Introduction of FANLYPLAS SPC Flooring Production Line
The SPC flooring production line developed by our company is suitable for extruding SPC flooring of various sizes. We also provide customers with formulas and related technologies to help customers complete their projects.
At the same time, we also provide EIR hardware and software services
Complete set of solutions can be provided according to customer needs.
Including:
- Automatic conveying weighing and mixing system
- SPC flooring extrusion line
- UV Coating line
- Slitting and grooving line
- IXPE/EVA lamination line
- Automatic packing line
Equipment Composition of FANLYPLAS SPC Flooring Production Line
FANLYPLAS offers customized SPC Flooring Production Line based on customer requirements, including product specifications, production volume, facility size, and desired level of automation. We provide flexible configurations to meet various needs. Below are some of the standard configurations available for FANLYPLAS SPC Flooring Production Line.
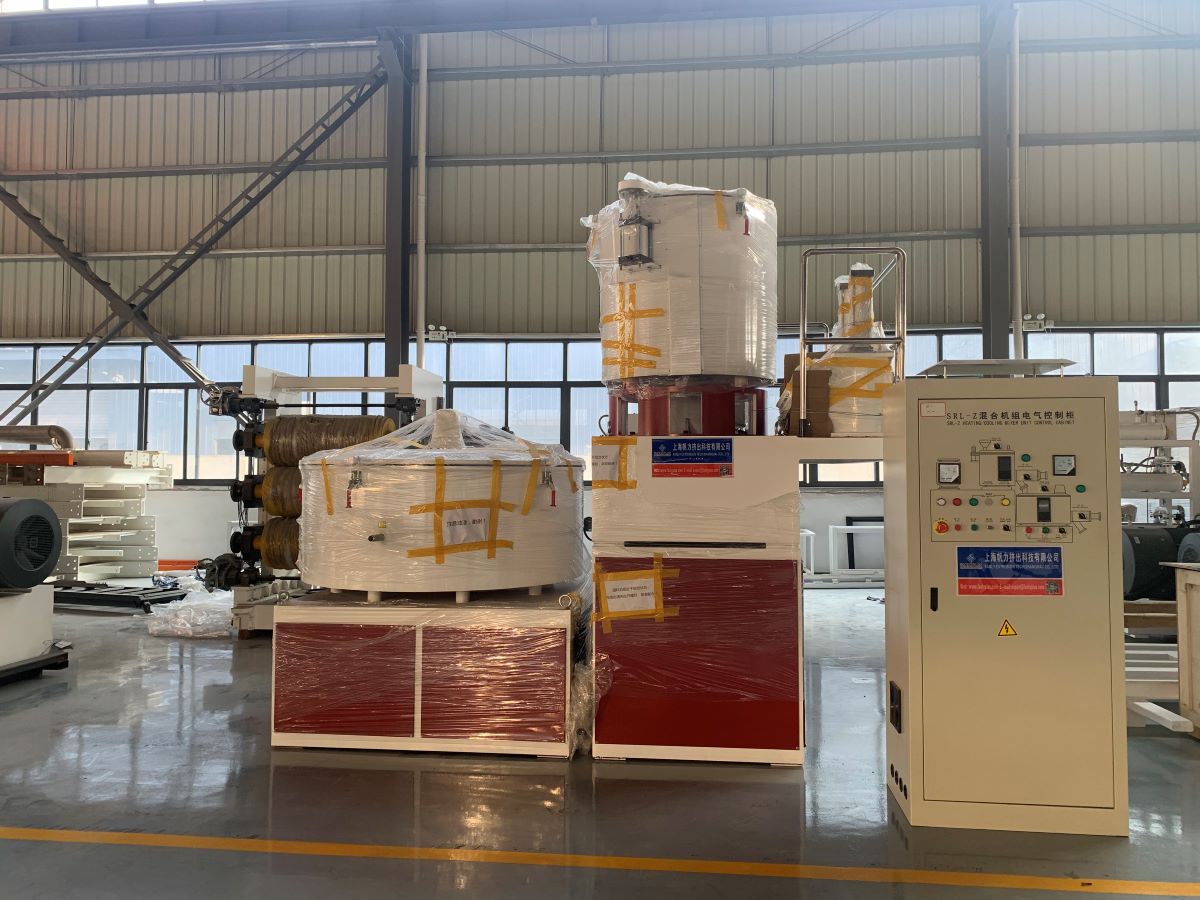
Mixer
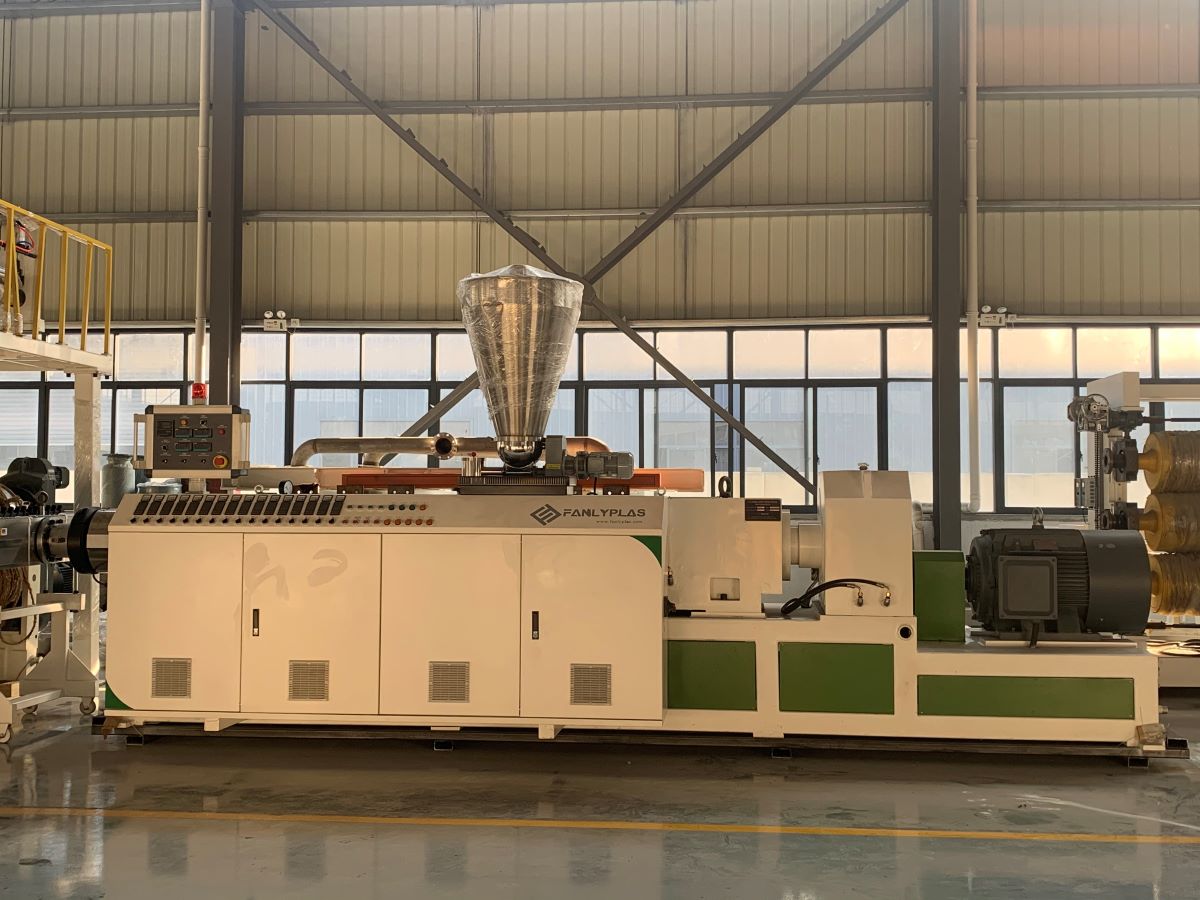
Extruder
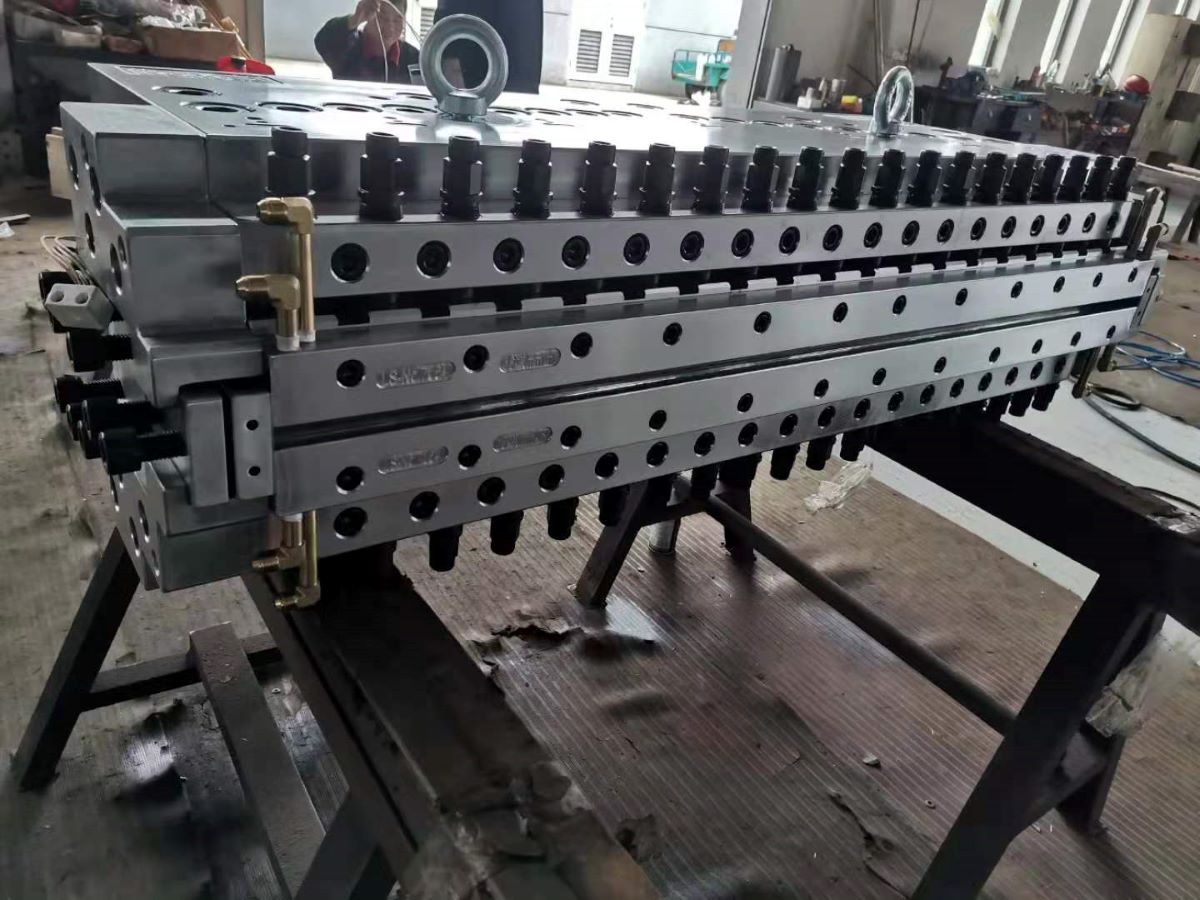
T-Die
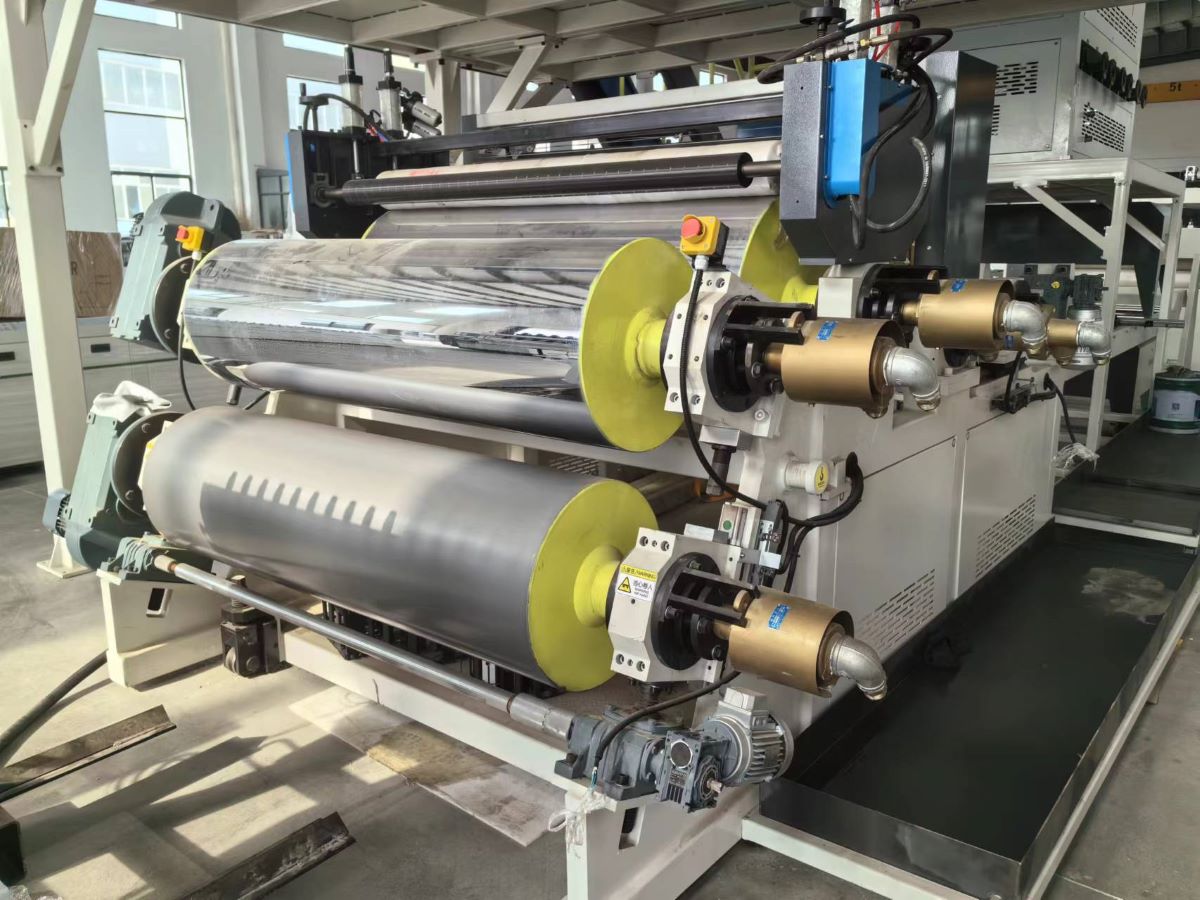
Five-roll Calender
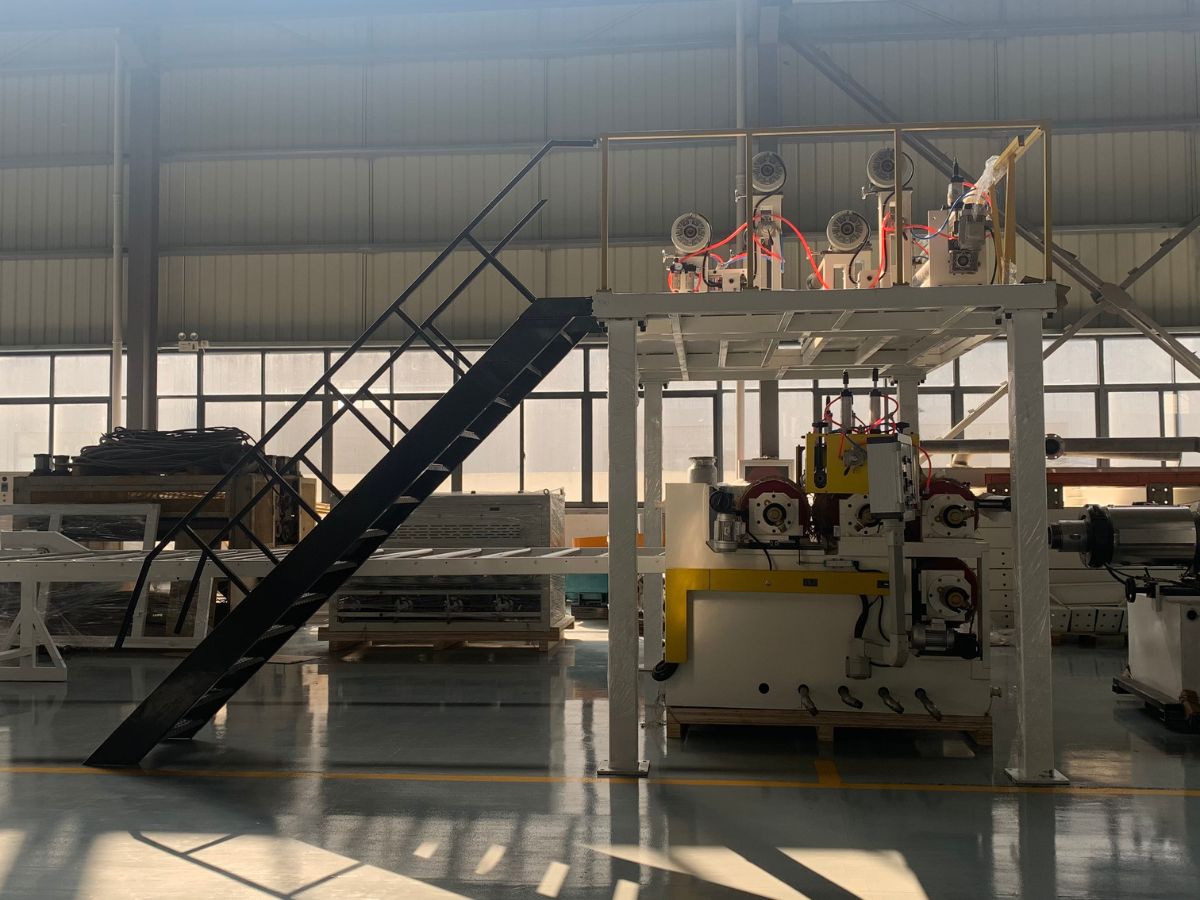
Film laminating device
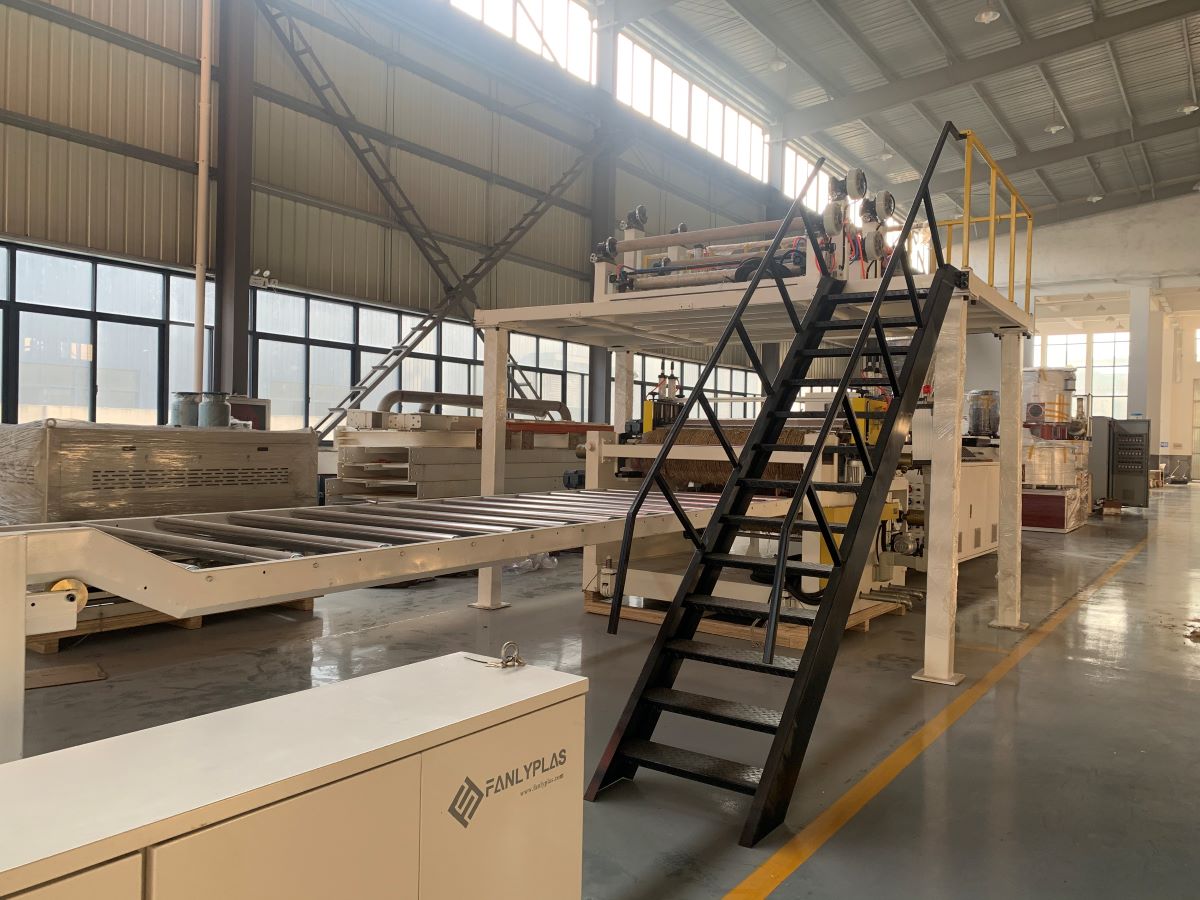
Cooling bracket and trimming cutter
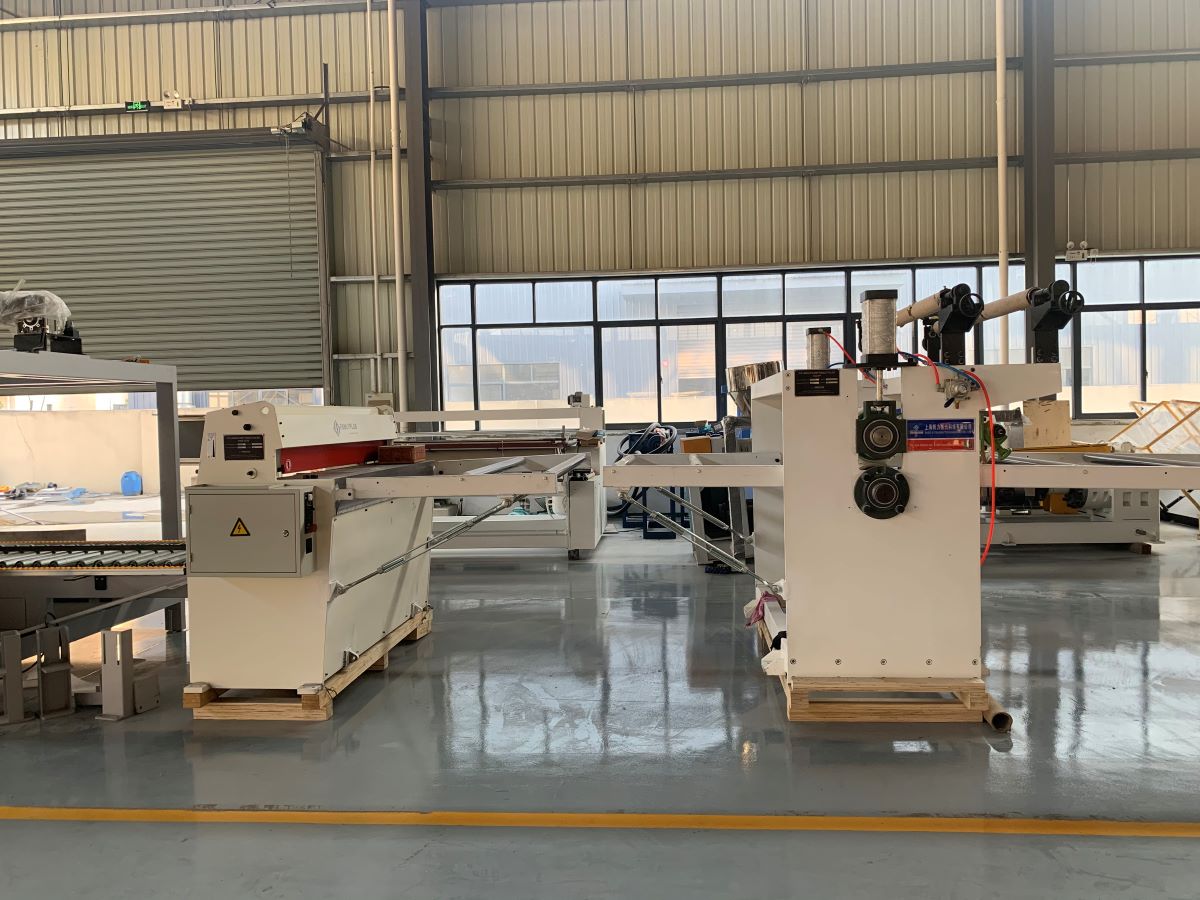
Haul off
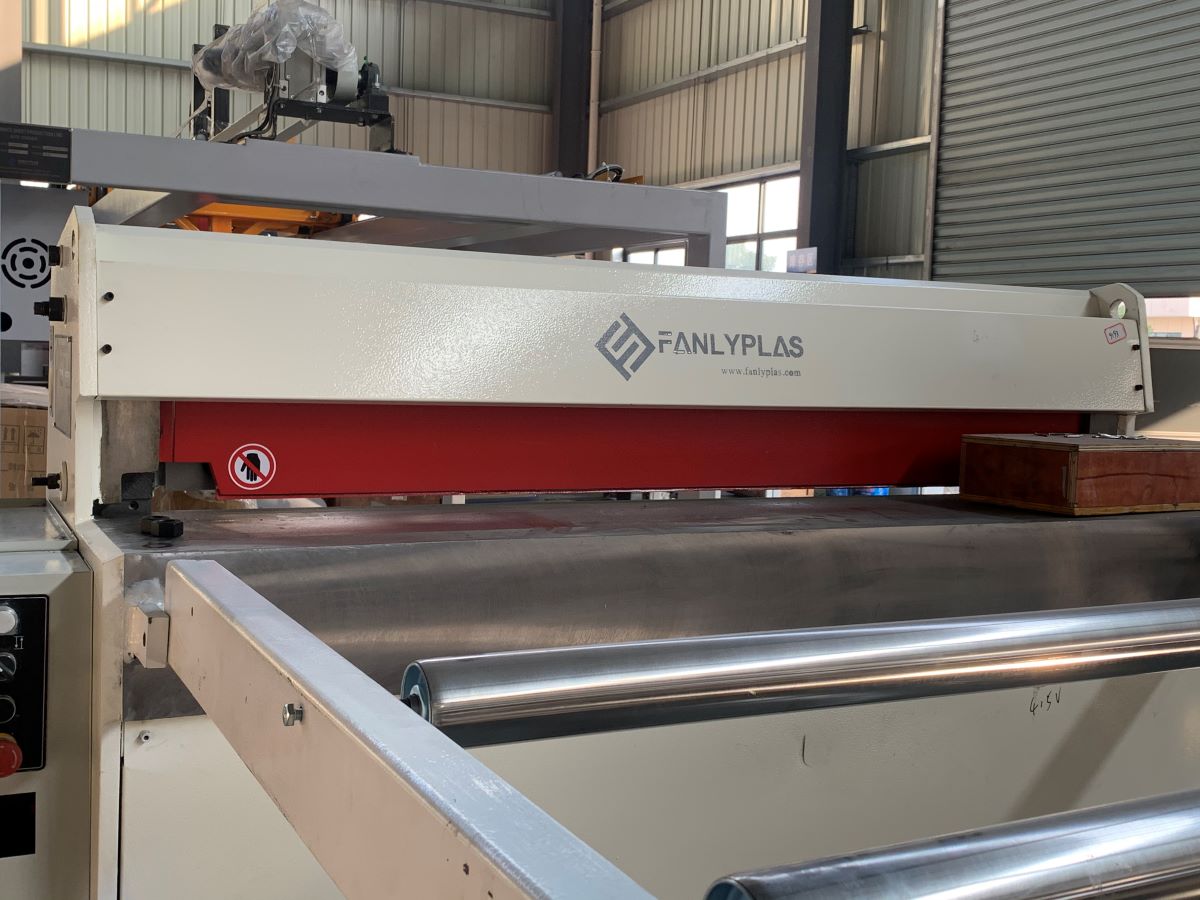
High speed shear utter
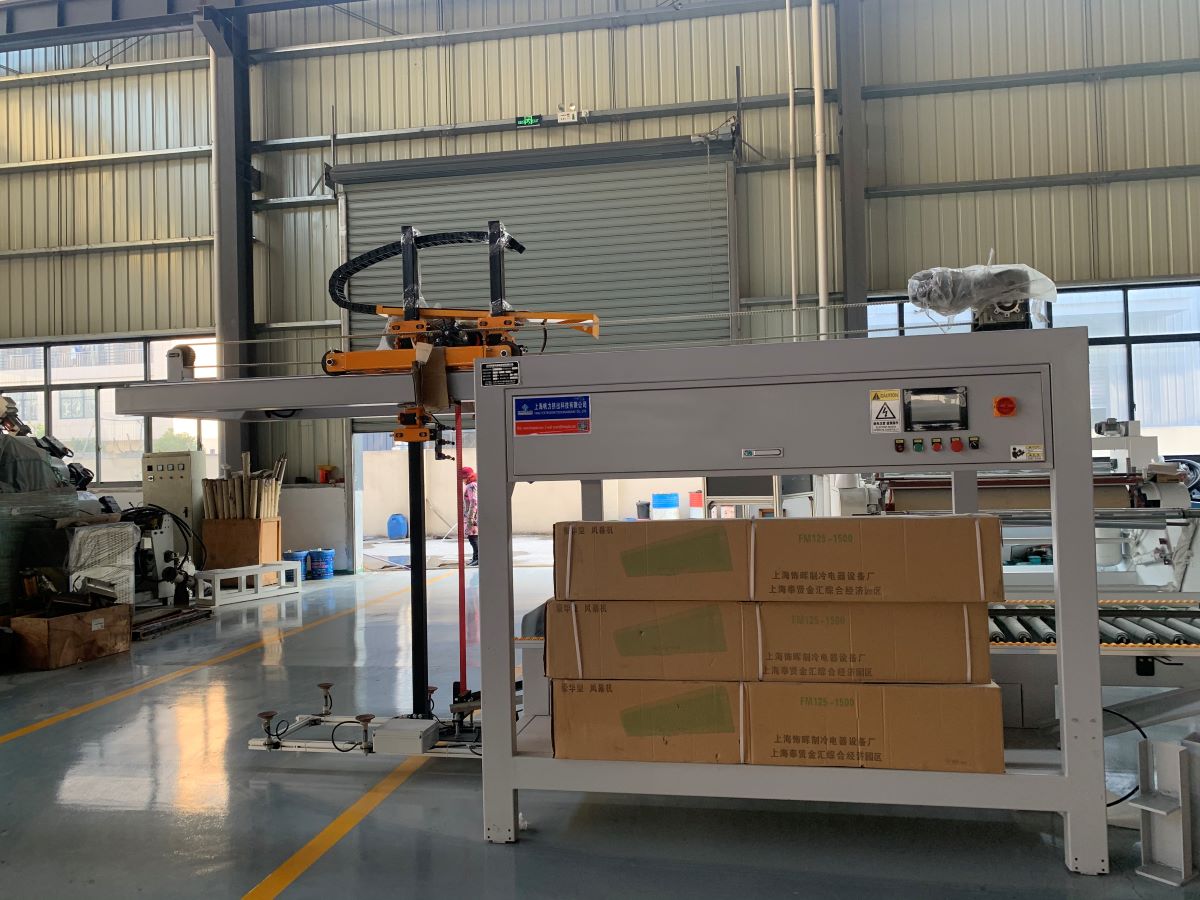
Auto stacker
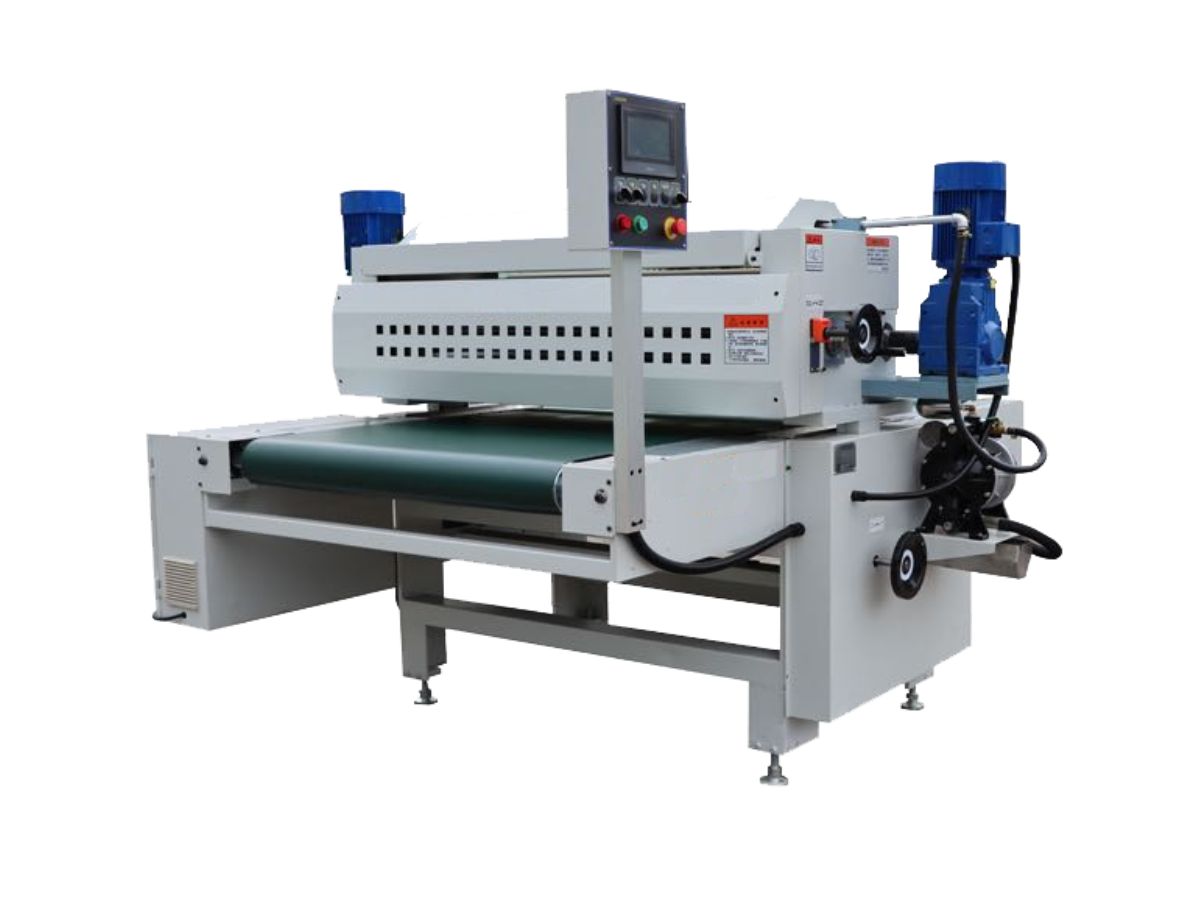
UV Coating line
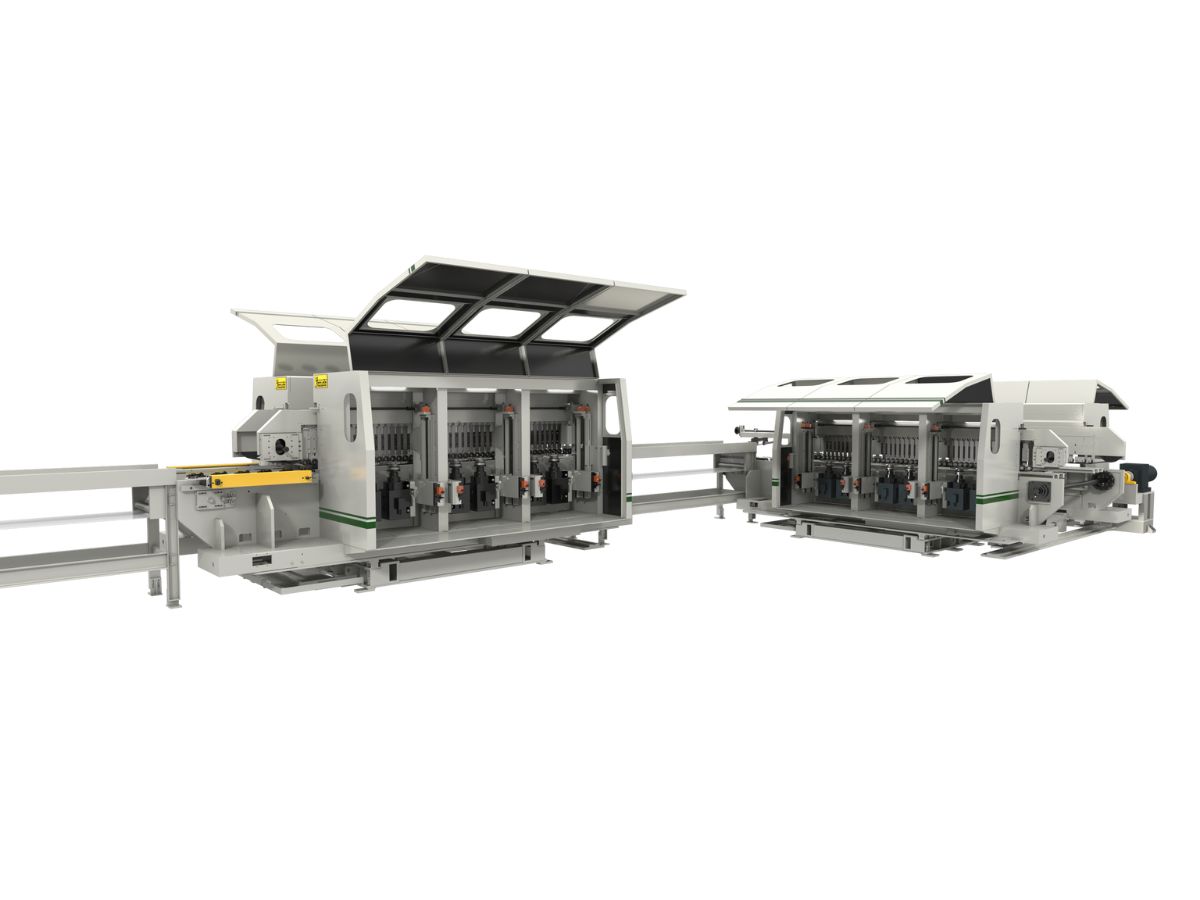
Slitting and Grooving line
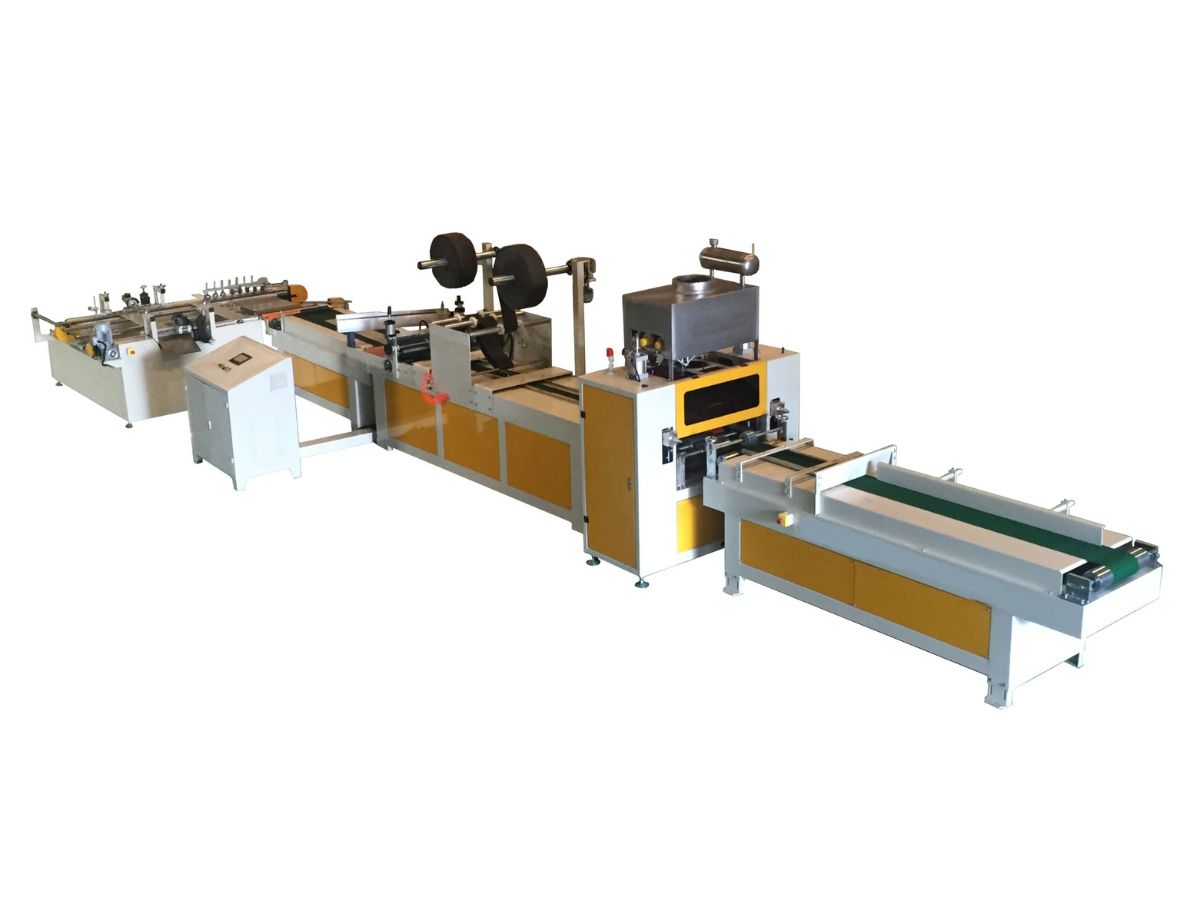
IXPE/EVA laminate
Features of FANLYPLAS SPC Flooring Production Line
1.The screw adopts the design of special mixing material function and high plasticization capacity. This guarantees the uniformity of plastic melting, coloring, and high output.
2.T-type die head adopts a double throttling design, which makes them more precise in adjusting the thickness of the sheet.
3.The arrangement of roller can be vertical, horizontal, or free adjusting type, which can give more selection based on different thickness of the sheet.
4.The double loop cooling system and mould temperature controller are adopted to control press-roller temperature, by which sheet thickness can be controlled accurately.
5.The automatic measuring meter instrument can set the length of the sheet.
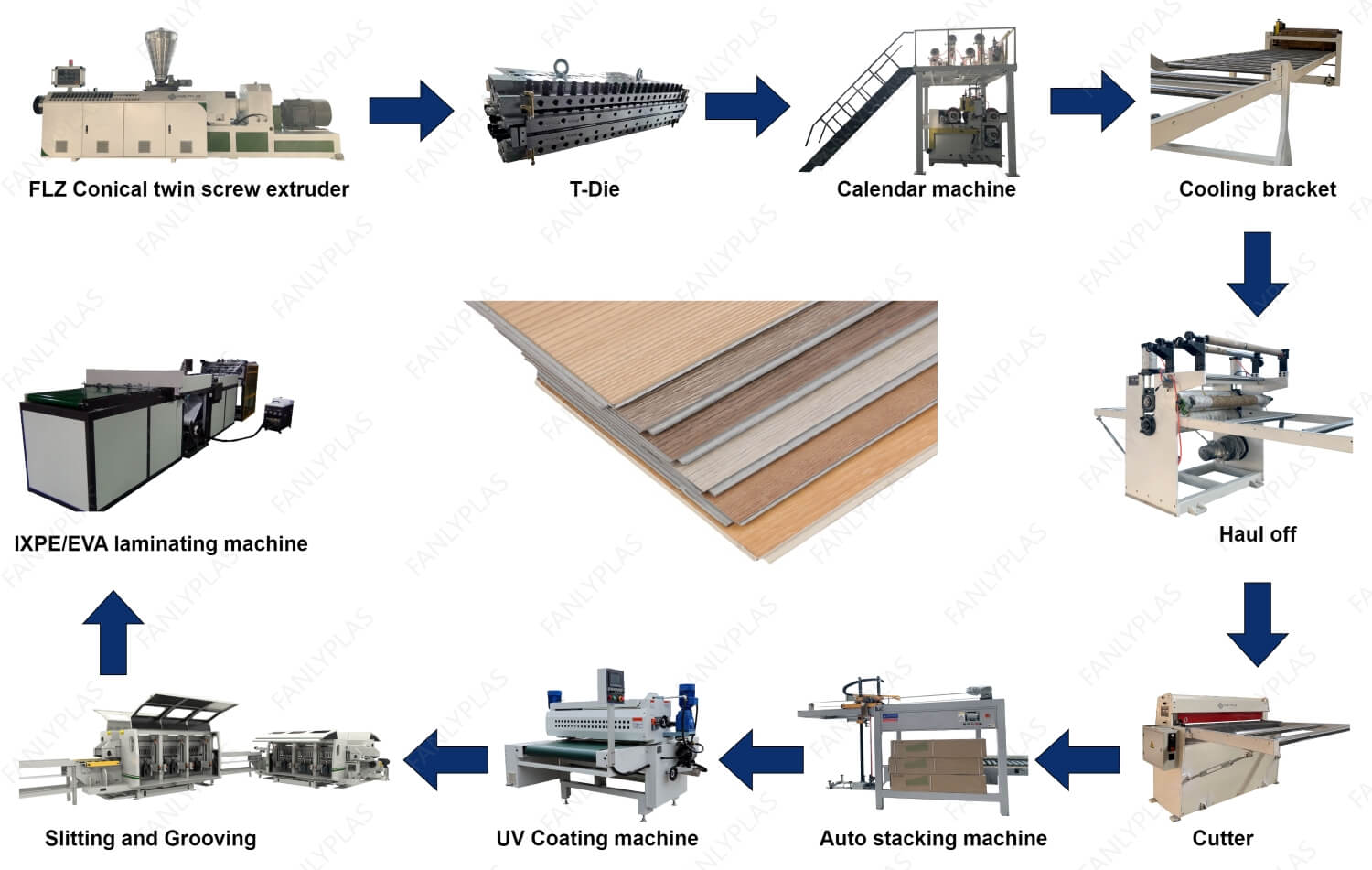
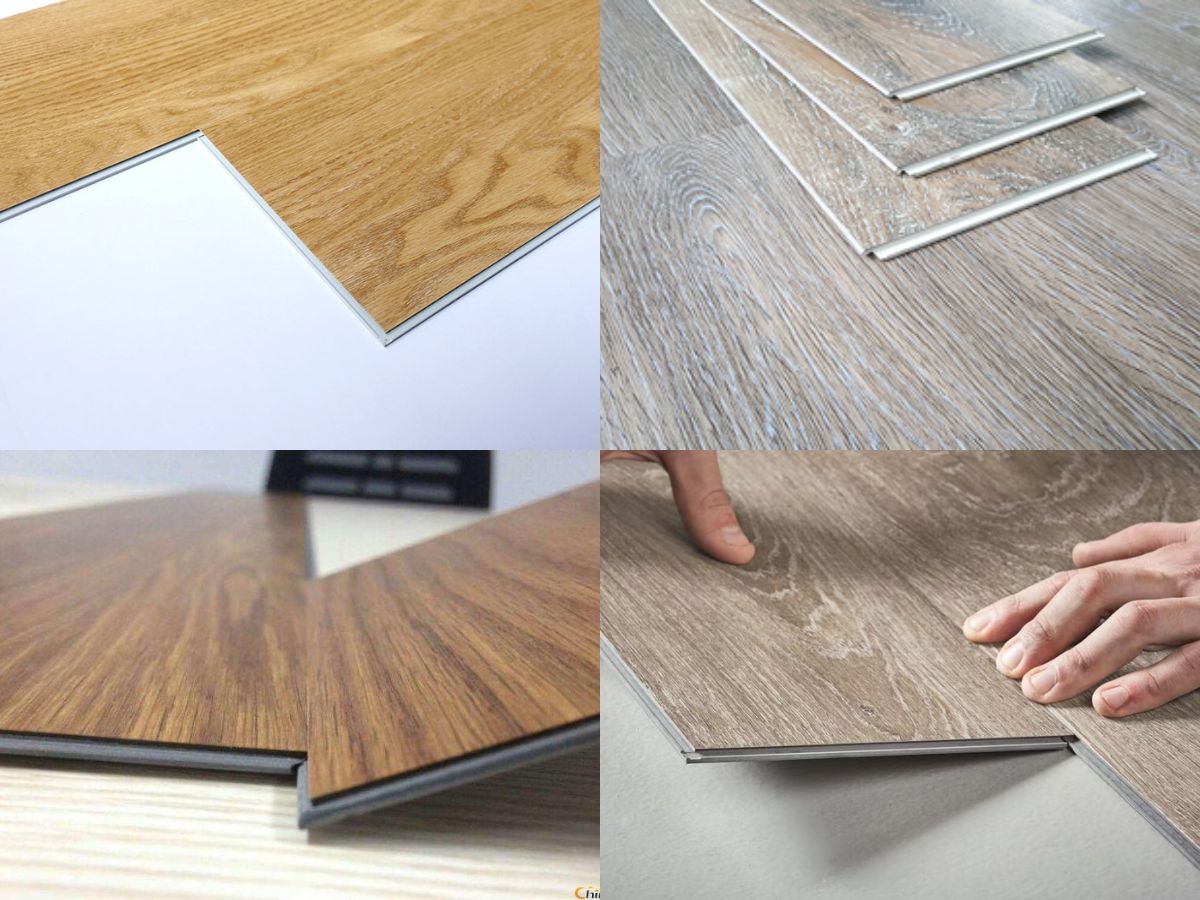
Characteristics and Applications of SPC Flooring
SPC flooring is made of stone-plastic composite, offering excellent stability and durability to resist scratches, impacts, and heavy loads, ideal for high-traffic areas. Its waterproof and moisture-resistant properties excel in wet environments like kitchens and bathrooms. Free from formaldehyde and harmful substances, SPC flooring is eco-friendly and meets international green standards. The advanced click-lock design ensures easy, glue-free installation, making it an aesthetic and practical choice for both residential and commercial spaces.
1.Residential Use:Ideal for bedrooms, living rooms, and kitchens, SPC flooring provides a slip-resistant, durable, and aesthetically pleasing solution for comfortable and safe home living.
2.Commercial Spaces:Widely used in offices, retail stores, and hotels, SPC flooring withstands heavy traffic with wear resistance and compression strength, while maintaining an elegant appearance.
3.Educational Institutions:Perfect for schools and kindergartens, SPC flooring is slip-resistant, wear-resistant, and easy to clean, ensuring safety and promoting a healthy learning environment.
4.Healthcare Facilities:Commonly used in hospitals and clinics, SPC flooring’s moisture-resistant, slip-resistant, and easy-to-clean features meet hygiene standards, providing a safe and reliable flooring solution.
FAQS
What is the production capacity of the SPC flooring production line?
We have two regular models to choose from, Model 110 and Model 115. Model 110 can produce 1000-1200 kg per hour, and Model 115 can produce 1300-1450 kg per hour.
Can the production line produce sheets of different sizes and thicknesses?
Yes, the line is designed to produce panels in various thicknesses (3-8mm) and widths between 960-980mm. Other sizes can also be custom made for you.
What raw materials are required for the production line?
The main raw materials are PVC (Polyvinyl chloride), Calcium powder and appropriate processing aids.
How long does it take to install and commission the production line?
Installation and commissioning typically take 10-15 days, depending on the complexity of the production line. Our engineers provide on-site support and training during this period.
What after-sales services do we offer?
We provide comprehensive after-sales services, including equipment maintenance, spare parts supply, remote troubleshooting and on-site technical support. In addition, we also provide operator training, including equipment operation and raw material guidance.
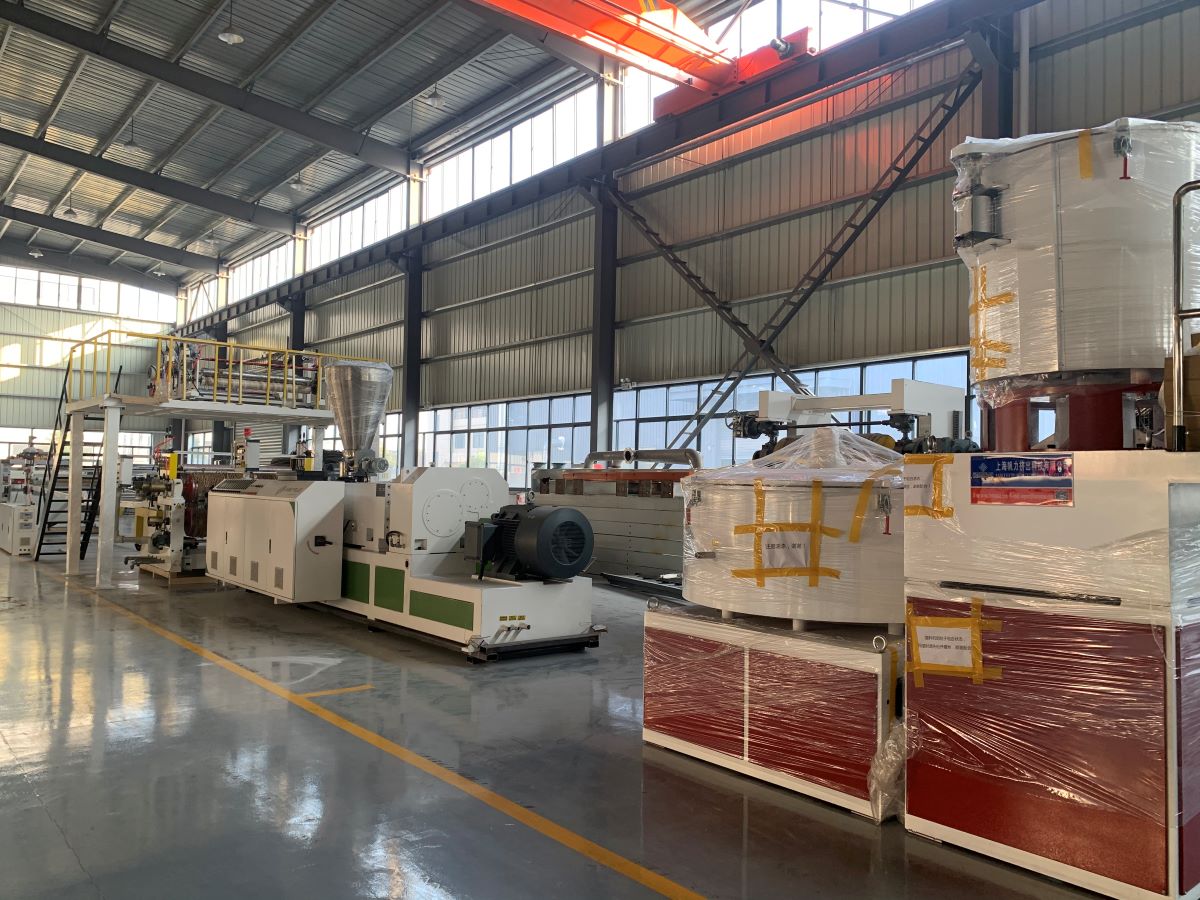
Get Extrusion Solutions Or Service Today?
Just leave your needs & questions here, we will back you in short time. (The more details you leave, the better quotation will reach you soon)
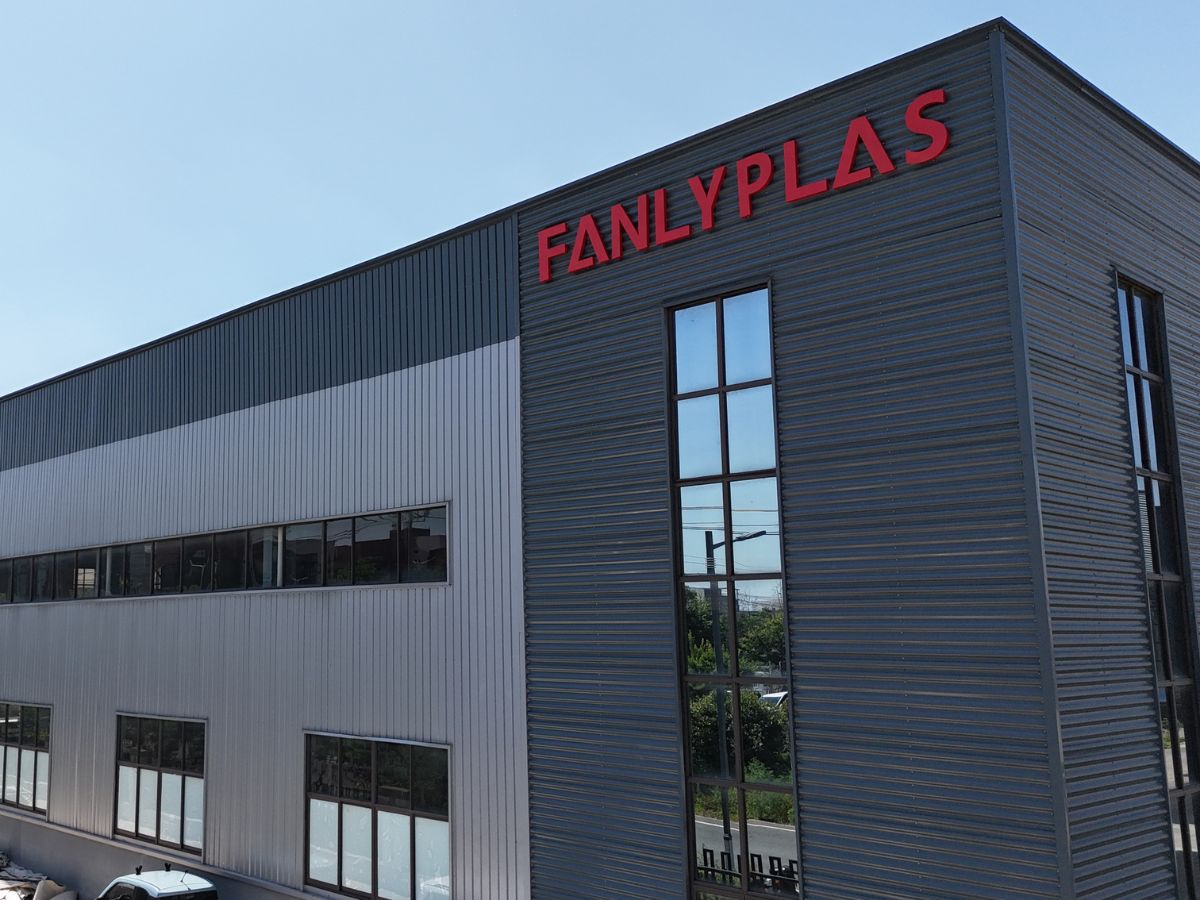